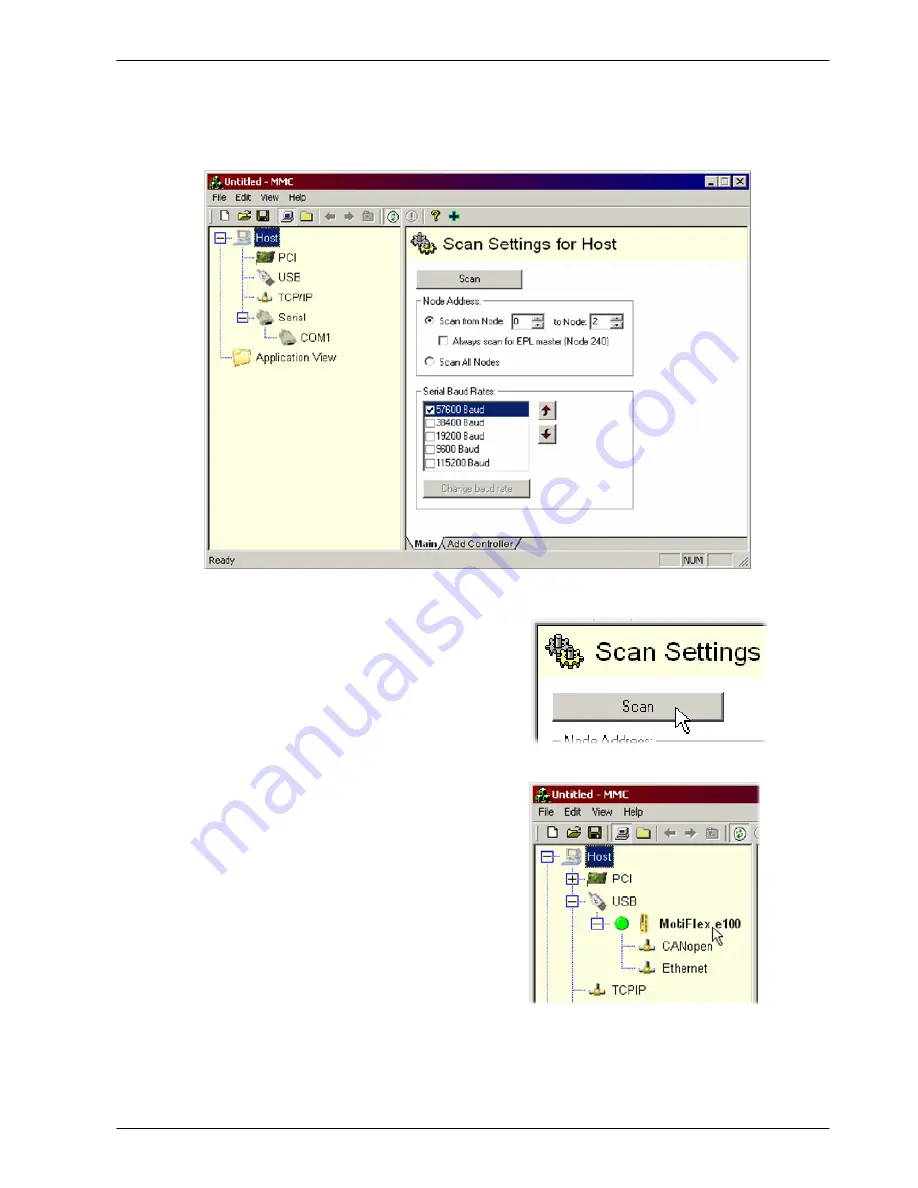
www.baldormotion.com
Configuration 6-7
MN1943
6.3.1 Starting MMC
1. On the Windows
Start
menu, select Programs, Mint Machine Center, Mint Machine Center.
2. In the controller pane, ensure that Host is
selected. In the information pane, click
Scan.
3. When the search is complete, click once
on ‘MotiFlex e100’ in the controller pane to
select it, then double click to open an
instance
of
Mint
WorkBench.
The
MotiFlex
e
100 will be already connected
to the instance of Mint WorkBench, ready
to configure.
Содержание MotiFlex e100
Страница 1: ......
Страница 2: ......
Страница 60: ...www baldormotion com 3 44 Basic Installation MN1943 ...
Страница 102: ...www baldormotion com 5 28 Input Output MN1943 ...
Страница 136: ...www baldormotion com 7 8 Troubleshooting MN1943 ...
Страница 172: ...www baldormotion com 8 36 Specifications MN1943 ...
Страница 188: ...www baldormotion com B 6 Control System MN1943 ...
Страница 204: ...www baldormotion com C 16 Mint Keyword Summary MN1943 ...
Страница 216: ...Index MN1943 ...
Страница 218: ...www baldormotion com Comments MN1943 Thank you for taking the time to help us ...
Страница 219: ......
Страница 220: ......