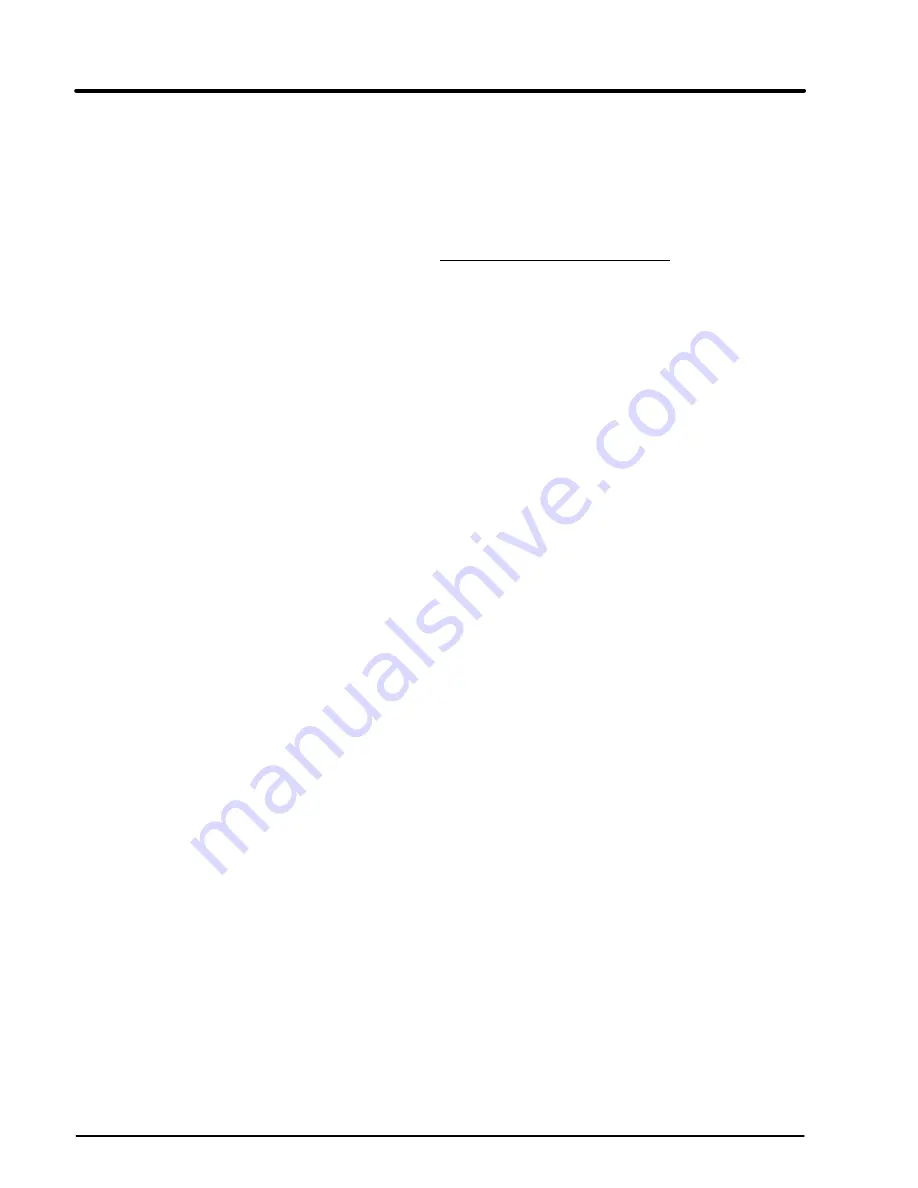
4-20 Programming and Operation
MN715J
Parameter Block Definitions
Level 2 Continued
Stop Brake Time
The maximum number of seconds that DC injection brake voltage
will be applied to the motor windings after a stop command. After the time
specified by this value, DC injection braking is automatically turned off. If DC
injection braking starts at a frequency less than the DC brake frequency
parameter, the stop brake time is calculated as follows:
Brake Time
+
Stop Brake Time X
Output Frequency at Braking
DC Brake Frequency
Brake on Start
If set to ON, turns DC injection braking ON for a period of time (Start
Brake Time) when a run command is issued. Braking will automatically turn off
and the motor will accelerate at the end of the start brake time.
Start Brake Time
The amount of time that DC injection braking will be applied after a
run command is issued. This will only occur if brake on start is set to ON.
Braking may cause the motor to overheat for applications that require frequent
starts/stops. Be careful in selecting this value. The start brake time should be
just long enough to ensure the motor shaft is not rotating when a start command
is issued.
PROCESS CONTROL
Process Feedback
The type of signal used for the process feedback in the PID
setpoint control loop.
Process Inverse
OFF – The process feedback signal is not inverted (no polarity
change).
ON – Causes the process feedback signal to be inverted. Used with reverse
acting processes that use a unipolar signal such as 4-20mA. If “ON”, the PID
loop will see a low value of the process feedback signal as a high feedback
signal and a high value of the process feedback signal as a low feedback signal.
Setpoint Source
The source input reference signal type to which the process
feedback will be compared. If “Setpoint CMD” is selected, a fixed value that is
entered in the Setpoint Command parameter (of the Level 2 Process Control
block) will be used.
Setpoint Command
The setpoint value for the PID loop that the control will try to
maintain. Used only when the setpoint source parameter is set to “Setpoint
Command”.
Set PT ADJ Limit
The maximum frequency correction value to be applied to the
motor (in response to the maximum process error). For example, if the max
output frequency is 60 Hz, the setpoint adjustment limit is 20%, the process error
is 100% and the maximum speed the motor will run in response to the setpoint
feedback error is
±
12 Hz. (60Hz x 20% = 12Hz or a total of 24 Hz total output
band-width centered around the effective setpoint frequency).
At Setpoint Band
The operating band within which the At Setpoint opto output is
active (turned ON). This feature indicates when the process is within the desired
setpoint range. For example, if the setpoint source is 0-10VDC and the at
setpoint band value is 10%, the at setpoint opto output will turn on if the process
is within (10 x 10% = 1)
±
1VDC of the setpoint.
Process PROP Gain
Sets the PID loop proportional gain or how much adjustment to
motor speed is made to bring the process to the setpoint.
Process INT Gain
The PID loop Integral gain or how much adjustment to motor
speed is made to correct for long term error.
Process DIFF Gain
The PID loop differential gain or how much adjustment to motor
speed is made for short term error.
Содержание ID15J101-ER
Страница 1: ...Series 15J Inverter Control 7 04 MN715J Installation and Operating Manual ...
Страница 5: ...iv Table of Contents MN715J ...
Страница 11: ...2 4 General Information MN715J ...
Страница 59: ...4 22 Programming and Operation MN715J ...
Страница 75: ...6 6 Specifications and Product Data MN715J ...
Страница 79: ...A 4 Dynamic Brake Hardware MN715J ...
Страница 86: ...Appendix C Remote Keypad Mounting Template MN715J Remote Keypad Mounting Template C 1 ...