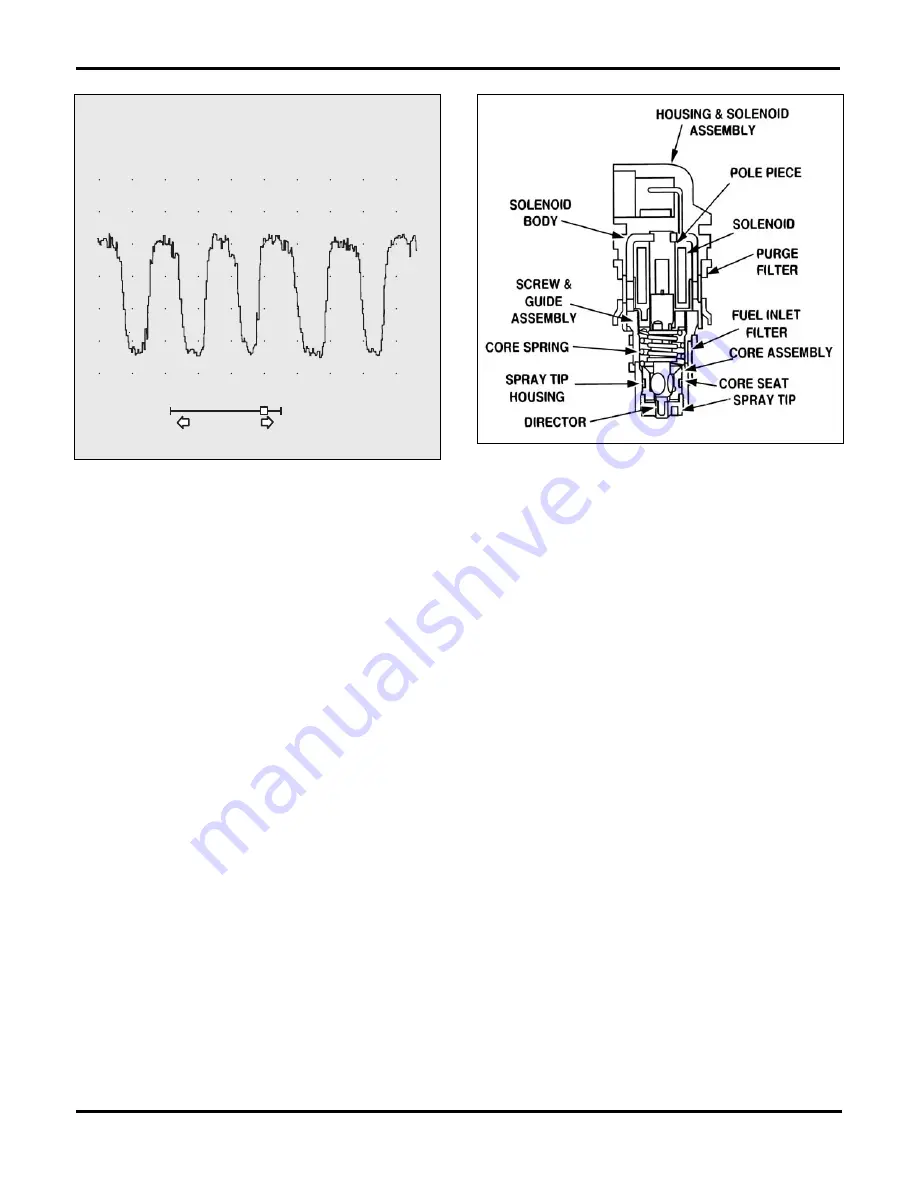
Chapter
C
: Fuel, Air Induction, and Exhaust Systems Diagnosis and Repair
65
Oxygen Sensor Replacement
To replace an HO2S, disconnect the sensor output lead
from the wiring harness. Spray manifold heat valve sol-
vent around the sensor threads and allow it to soak for
several minutes. Then use a special socket to unscrew
the sensor from the manifold. In some cases, it may be
easier to remove the sensor if the manifold is slightly
warmed. Clean any rust, residue, or corrosion from the
sensor hole threads with a thread-chasing tap. Most
new sensors come with the antisieze compound already
applied to the threads. When installing a used sensor,
coat the threads only with a compound specifically de-
signed for oxygen sensor use and recommended by the
manufacturer. Thread the sensor into the manifold and
torque to specifications, generally in the 20 to 35 ft-lb.
(15 to 25 Nm) range.
FUEL INJECTOR SERVICE
Most automotive fuel injectors are electronically actuat-
ed solenoids controlled by the PCM, figure 3-21. Some
older vehicles utilized hydraulic injectors but are rarely
seen on gasoline engines today.
Injector Testing
Electronic injectors are solenoid-operated actuators and
can be checked with a DMM or oscilloscope.
Before testing the injectors, make sure that:
• The fuel pump delivery pressure is correct
• The pressure regulator is functioning properly
• The battery is fully charged
• The charging system is working properly
• The PCM is receiving the supply voltage it requires
Current flow in an injector circuit varies by manufactur-
er and model year. Refer to the appropriate Service
Manual for the correct specifications. Many late-model
systems use a low-resistance injector in conjunction
with the PCM's ability to limit the current flow in the cir-
cuit. The initial current flow is high to rapidly energize the
solenoid and then once the injector opens, the PCM
ramps down the current. This design is sometimes
called "peak and hold" injection. The PCM regulates in-
jector activity by controlling the ground side of the cir-
cuit.
A weak or defective injector can often be detected by
performing a cylinder balance test. See Chapter One of
this book. Uneven balance may be caused by the injec-
tor or an ignition or mechanical problem. Eliminate all
other possibilities before replacing the injector.
An injector flow balance test can be performed while the
injectors are installed in the engine. A special balance
tester is required to turn the injector on for a precise time
period without running the engine, figure 3-22. The test
allows the injector to spray a measured amount of fuel
into the manifold, causing a drop in fuel rail pressure
that can be recorded and compared to specifications.
Any injector whose pressure drop exceeds specifica-
tions should be replaced.
1000
1200mV
BACK
SELECT
SEARCH
800
600
400
200ms/DIV
200
0
HOLD
800
RECALL
0.00
mV MAXIMUM
V
MINIMUM
Fig. 3-20.
Oscilloscope trace of a good HO
2
S that is switching
normally.
Fig. 3-21.
Typical fuel injector.
Содержание ASE-A8
Страница 2: ......