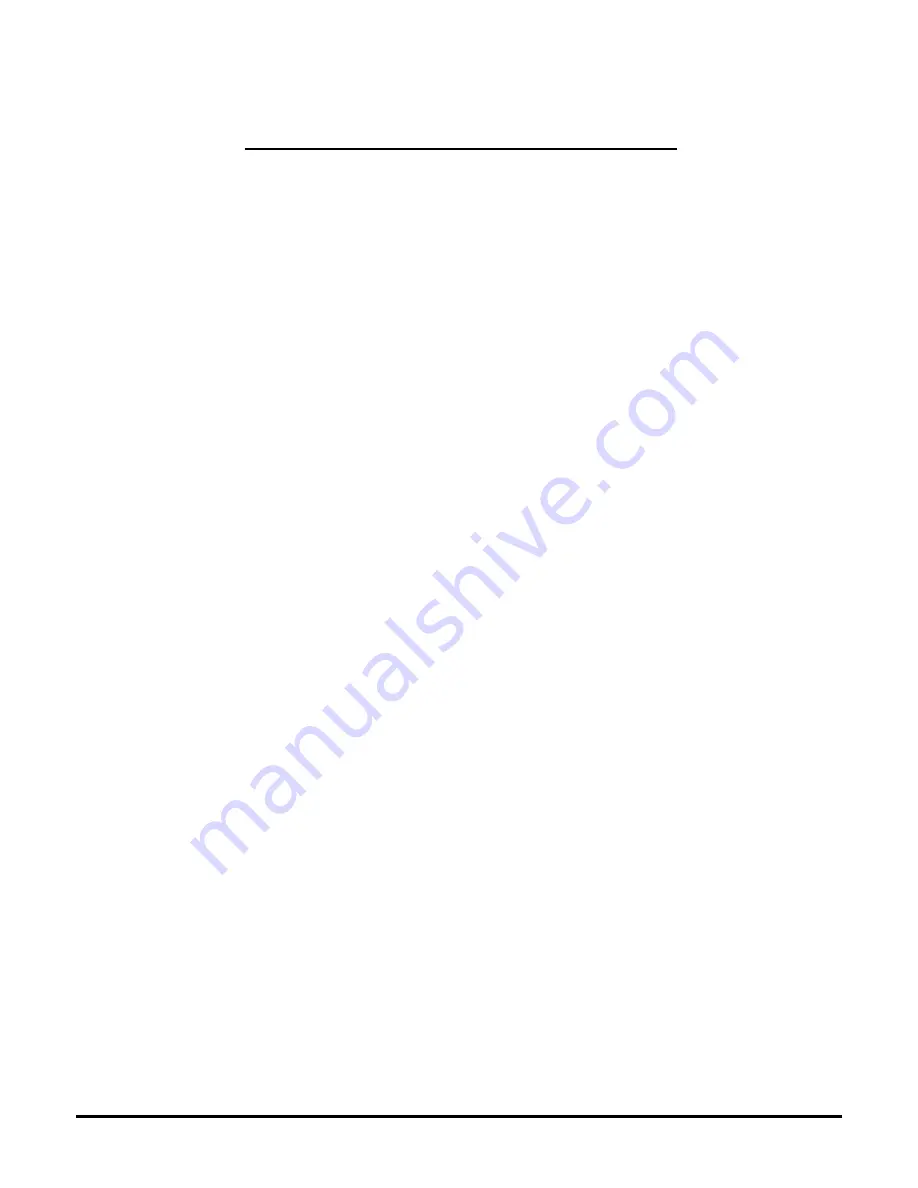
Chapter
B
IGNITION SYSTEM DIAGNOSIS AND REPAIR
This chapter discusses testing, repairing, and replacing
individual components of the ignition system. Most
modern ignition systems contain delicate, and expen-
sive, electronic components that can be destroyed by a
voltage surge. The high-voltage surge that results from
simply making or breaking a connection can cause
damage. When working on the ignition system, take
these precautions to avoid damage to the ignition sys-
tem and personal injury:
1. Unless the procedure specifically states otherwise,
switch the ignition off or disconnect the battery
ground cable before separating any ignition system
wiring connections.
2. Do not touch, or short to ground, any exposed con-
nections while the engine is cranking or running.
3. Do not short the primary circuit to ground without
resistance; the high current that results can dam-
age circuits and components.
4. Do not create a secondary voltage arc near the bat-
tery or fuel system components. This can cause an
explosion.
5. When testing the ignition system, follow the proce-
dure specified by the manufacturer.
SPARK DISTRIBUTION SYSTEMS
Early in the 20th Century the first electrical ignition sys-
tem, the self-starter for automobile was invented. This
type of ignition system is known as the Kettering system
consisting of points, condenser, and an ignition coil. It
became the standard in the automotive industry replac-
ing magnetos. A gear, chain, or belt from the engine dri-
ves the distributor. Inside this distributor is a spring
loaded contact switch known as the points. The points
ride on a revolving cam and open and close to fire a sin-
gle coil which produces the spark. Inside the distributor
is also the rotor which rotates to direct the spark to the
correct spark plug wire.
Distributor Type Ignition Systems (DI)
As vehicle emissions and fuel economy standards be-
came stricter the need for an ignition system that could
produce a hotter spark was required. The mechanical
points could not handle the required increase in current
flow. To solve this problem the first electronic ignition
systems replaced breaker points with a transistor. This
system uses the distributor to signal the
ignition con-
trol module
(ICM) when to fire the spark plug. The ICM
uses a power transistor to control the coil primary cur-
rent flow.
Distributorless Ignition Systems (DIS)
Most late-model vehicles no longer use a distributor to
control ignition timing and direct the secondary voltage
to the spark plugs. The ignition coil's primary circuit
control, originally in the distributor, has been replaced
by ignition timing commands from the PCM. The PCM
receives input from the crankshaft position sensor (CKP)
and uses the information to control ignition timing. The
CKP can be a magnetic pickup or a Hall effect sensor;
both discussed later in this chapter. The DIS system de-
sign eliminates many moving parts and maintains more
accurate control of the ignition timing during the life of
the vehicle.
Figure 2-1, provides a sample of ignition related symp-
toms, definitions, and probable conditions or causes of
specific conditions. Always use the appropriate Service
Manual when conducting actual diagnostics on a vehi-
cle.
IGNITION SYSTEM DIAGNOSIS
Although most ignition systems are incorporated into
the engine management system, ignition failures gener-
ally do not set trouble codes and ignition malfunctions
cannot be detected on the serial data stream. The steps
taken to isolate the source of an ignition system failure
vary by vehicle and symptom.
Most modern electronic ignition systems are incorpo-
rated into the PCM. The ignition, fuel injection, and
emission control systems are linked together and all
three are diagnosed simultaneously. Proper diagnosis
requires the use of a diagnostic scan tool. You may also
need to use a breakout box (BOB) and
digital multime-
ter
(DMM) to complete the diagnostic process. Refer to
the appropriate Service or Diagnostic Manual for the
34
Содержание ASE-A8
Страница 2: ......