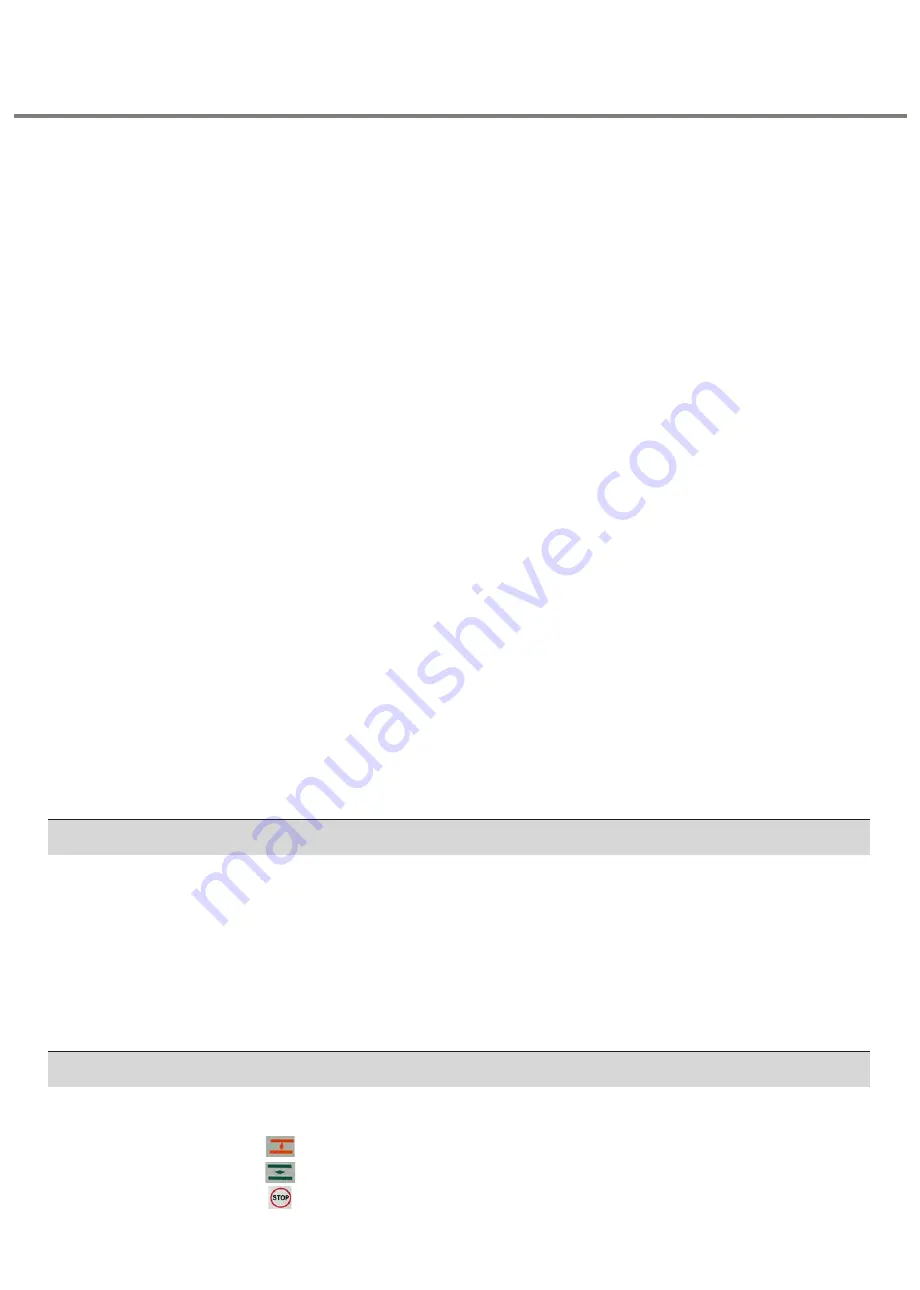
4
Operation
Prerequisites for safe and smooth operation:
•
Correct transport, proper storage, mounting and installation, as well as careful
commissioning.
•
Only operate the device if it is in perfect condition while observing these instructions.
•
Immediately report any faults and damage and allow for corrective measures.
•
Observe recognized rules for occupational health and safety.
•
Observe the national regulations.
Protective measures
The end user or the contractor is responsible for implementing required protective
measures on site, such as enclosures, barriers, or personal protective equipment for the
staff.
Maintenance
AUMA India multi-turn actuators require very little maintenance but they need to be tested
regularly for its correct functioning. After commissioning, check the actuator for damage to
paint finish. Do a thorough touch-up to prevent corrosion. Correct commissioning is a pre-
requisite for reliable service. Seals made of elastomers are subject to aging and must
therefore regularly be checked and, if necessary, exchanged. It is also very important that
the O-rings at the covers are placed correctly and cable glands fastened firmly to prevent
ingress of dust or water.
We recommend additionally:
•
If operated seldom, perform a test run about every 6 months. This ensures that the
actuator is always ready to operate. The version of actuators discussed in this
manual have an option for Partial Valve Stroke Test (PVST) to check if the actuator is
healthy.
•
Approximately six months after commissioning and then every year check bolts
between actuator and valve for tightness. If required, tighten by applying appropriate
torques.
•
The gear housing is filled with lubricant in the factory. This filling lasts for several
years of service.
•
Corrosion of paint damage parts must be prevented through touch up.
Any device modification requires the consent of the manufacturer.
1.2 Range of application
AUMA India actuator controls are exclusively designed for the operation of AUMA India
actuators. Other applications require explicit (written) confirmation by the manufacturer.
The following applications are not permitted.
•
Motor control
•
Pump control
No liability can be assumed for inappropriate or unintended use.
Observance of these operation instructions is considered as part of the device's
designated use.
1.3 References and symbols
The following references and symbols are used to provide information of the basic
actuator commands to the customer. They are:
Symbol for CLOSED (valve closed)
Symbol for OPEN (valve open)
Symbol for STOP (valve stop)
Storage
√
Store in well-ventilated, dry room.
√
Protect against floor dampness by storage on a shelf or on a wooden pallet.
√
Cover to protect against dust and dirt. Apply suitable corrosion protection agent to
bare surfaces.
√
In case gearboxes are to be stored for a long period (more than 6 months). Protect
bare surfaces, in particular the output drive parts and mounting surface, with long-
term corrosion protection agent.
√
Check for corrosion approximately every 6 months. If first signs of corrosion show,
apply new corrosion protection.
Type of enclosure is mentioned on the name plates.
Packaging
√
Our products are protected by special packaging for the transport ex-works.
√
The packaging consists of environmentally friendly materials which can be easily
separated and recycled.
√
For the disposal of the packaging material, we recommend approved disposal
agency.
√
We use the following packaging materials: Wooden material boards (OSB) /
cardboard / paper, PE sheet.
1.1.4 Qualification of staff
Assembly, electrical connection, commissioning, operation and maintenance must be
carried out exclusively by suitably qualified personnel having been authorized by the end
user or contractor of the plant only. Prior to working on this product, the staff must have
thoroughly read and understood these instructions and, furthermore, know and observe
officially recognized rules regarding occupational health and safety.
Work performed in potentially explosive atmospheres is subject to special regulations
which have to be observed. The end user or contractor of the plant is responsible for
respect and control of these regulations, standards and laws.
1.1.5 Commissioning
Prior to commissioning, it is important to check that all settings meet the requirements of
the application. Incorrect settings might present a danger to the application, e.g. cause
damage to the valve or the installation. The manufacturer will not be held liable for any
consequential damage. Such risk lies entirely with the user.
1.1.6 Operation
Prerequisites for safe and smooth operation:
•
Correct transport, proper storage, mounting and installation, as well as careful
commissioning.
•
Only operate the device if it is in perfect condition while observing these instructions.
•
Immediately report any faults and damage and allow for corrective measures.
•
Observe recognized rules for occupational health and safety.
•
Observe the national regulations.
Weather proof actuators with 3.XMP-SIL &
Data logging
Содержание SA3-SA100
Страница 18: ...18 Weather proof actuators with 3 XMP SIL Data logging...
Страница 19: ...19 Weather proof actuators with 3 XMP SIL Data logging...
Страница 20: ...20 Weather proof actuators with 3 XMP SIL Data logging...
Страница 21: ...21 Weather proof actuators with 3 XMP SIL Data logging...
Страница 22: ...22 Weather proof actuators with 3 XMP SIL Data logging...
Страница 23: ...23 Weather proof actuators with 3 XMP SIL Data logging...
Страница 25: ...25 Weather proof actuators with 3 XMP SIL Data logging...
Страница 28: ...28 Weather proof actuators with 3 XMP SIL Data logging...
Страница 31: ...31 Weather proof actuators with 3 XMP SIL Data logging...
Страница 41: ...41 Wiring Diagram for SIL with Pro bus DP Weather proof actuators with 3 XMP SIL Data logging...
Страница 42: ...42 Wiring Diagram for SIL without Pro bus DP Weather proof actuators with 3 XMP SIL Data logging...
Страница 43: ...43 Wiring Diagram for SIL without Pro bus DP Weather proof actuators with 3 XMP SIL Data logging...
Страница 44: ...44 SIL Certi cate Weather proof actuators with 3 XMP SIL Data logging...
Страница 46: ...46 Weather proof actuators with 3 XMP SIL Data logging...
Страница 47: ...47 Weather proof actuators with 3 XMP SIL Data logging...