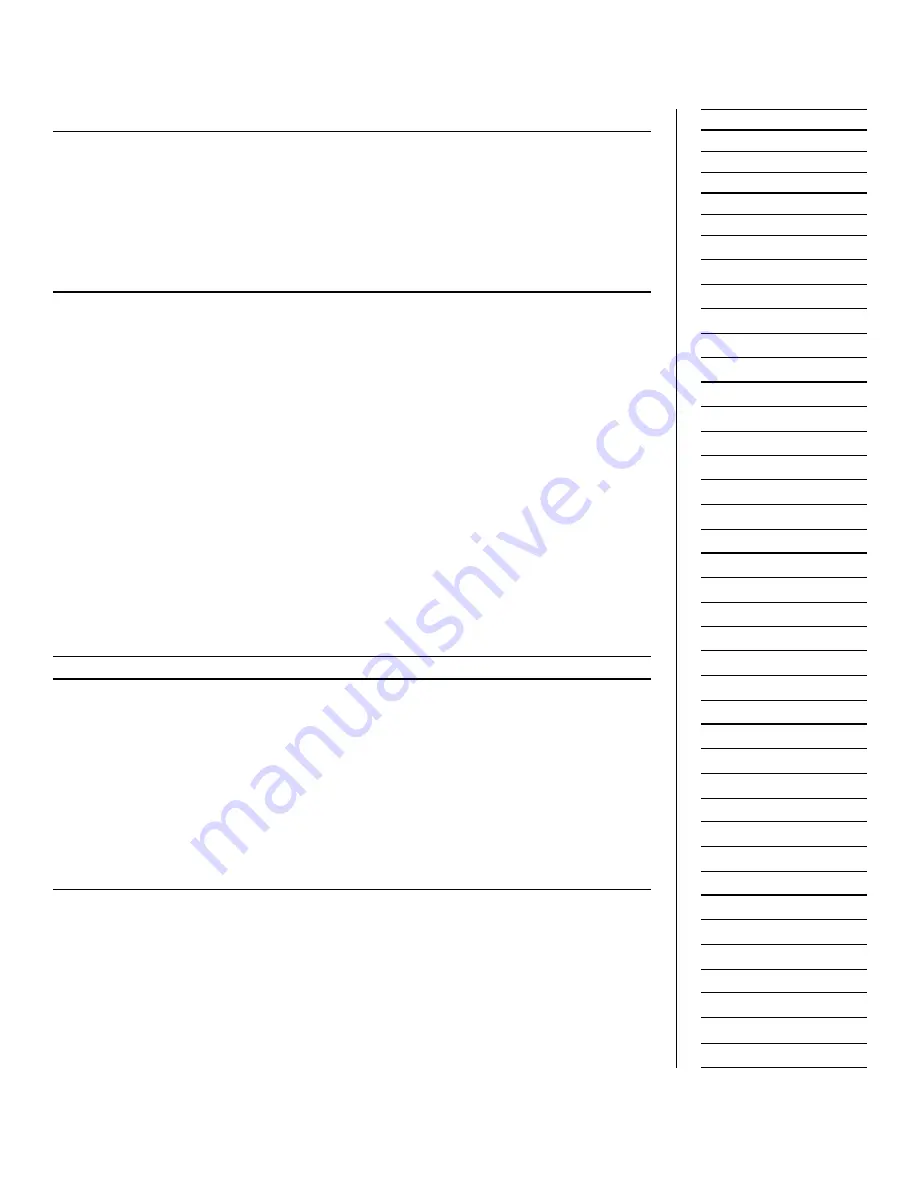
Level 2 Maintenance Training, Century Series
2-21
P/N 73-0028-00 Revision A
Level 2 Module 2
STUDENT GUIDE
LESSON 14 Valve Purging, CONTINUED
EXERCISE 2-11
Performing a purge procedure for the DP2000 Series
1.
Check that the valve pressure is at normal operating level (50-80psi).
2.
Check that the purge station location has been properly taught in FMW.
3.
Check that the priming port stopcock is in the closed position.
4.
Click RUN A PROGRAM.
5.
Click SETUP.
6.
Select PURGE NEEDLE for the DP2400.
Skip this step for all other pumps.
7.
Select DP2000-PRIME.
8.
Hold a plastic cup under the priming port
9.
Open the priming port stopcock.
10.
Close the priming port stopcock when you are confident that all the air has been removed
from the chamber.
11.
Select DP2000-REFILL from the Setup Menu.
12.
Hold the plastic cup under the priming port again.
13.
Momentarily open the stopcock
14.
Close the stopcock again.
15.
Select PURGE NEEDLE from the Setup Menu.
16.
Repeat the priming procedure if fluid drips from the needle tip.
17.
Perform a needle priming procedure.
EXERCISE 2-12
Performing a purge procedure for the DJ2000 Series
1.
Double-click on the DISPENSE.OUT application.
2.
Open the FMCONFIG.ini file.
3.
Change the Forward Time in the Prompted Setup Parameters to 130.
4.
Change the Reverse Time to 10.
5.
Close the FMCONFIG.ini file.
6.
Start FMW.
7.
Click RUN A PROGRAM.
8.
Click SETUP.
9.
Select Prompted Setup.
Содержание C702
Страница 6: ...Level 2 Maintenance Training Century Series iv P N 73 0028 00 Revision A ...
Страница 10: ...Level 2 Maintenance Training Century Series iv P N 73 0028 00 Revision A ...
Страница 26: ...Level 2 Maintenance Training Century Series 1 16 P N 73 0028 00 Revision A ...
Страница 50: ...Level 2 Maintenance Training Century Series 2 24 P N 73 0028 00 Revision A ...
Страница 66: ...Level 2 Maintenance Training Century Series 3 16 P N 73 0028 00 Revision A ...
Страница 78: ...Level 2 Maintenance Training Century Series 4 12 P N 73 0028 00 Revision A ...
Страница 80: ...Level 2 Maintenance Training Century Series APPENDIX P N 73 0028 00 Revision A ...
Страница 82: ...Level 2 Maintenance Training Century Series APPENDIX P N 73 0028 00 Revision A ...