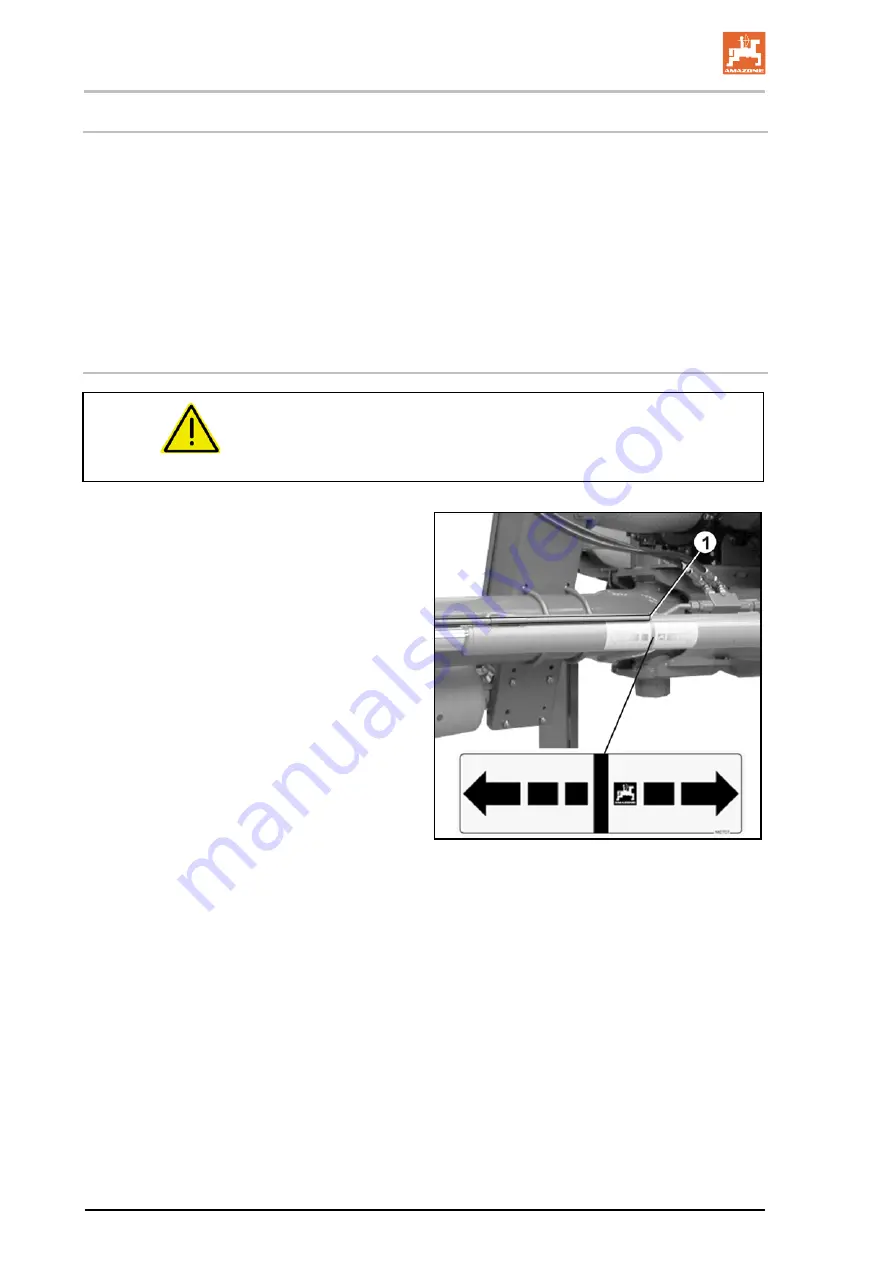
Structure and function
5.13
Tracking control via tractor control unit
When working on sloping terrain (sprayer slips off),
•
the
tractor control unit blue
can be used from the comfort of the tractor seat to manually steer the
steering drawbar so that it is tracking precisely.
When steering manually, hydraulic control reduces damage to the
crop, particularly with regard to drill crops (e.g. potatoes or vegeta-
bles) when driving or manoeuvring in and out of the drills.
Turning circle d
wk
> 18 m.
Transportation
DANGER
Risk of accident from the machine tipping over.
Move the steering drawbar to the transport position for transportation.
1. Actuate tractor control unit
blue
until the
drawbar is at the zero setting (Fig. 44/1).
Pay attention to the pointer and scale on the
hydraulic cylinder.
2. Universal drawbar: Secure the hydraulic
cylinder in position A, see page 75.
Fig. 41
80
BAG0021.14 05.19
Содержание UG 2200 Special
Страница 237: ...Liquid circuit 13 1 UG Special BAG0021 14 05 19 237 ...
Страница 238: ...Liquid circuit 13 2 UG Super 238 BAG0021 14 05 19 ...
Страница 242: ...Spray table Fig 182 242 BAG0021 14 05 19 ...
Страница 251: ...Spray table BAG0021 14 05 19 251 ...
Страница 252: ......