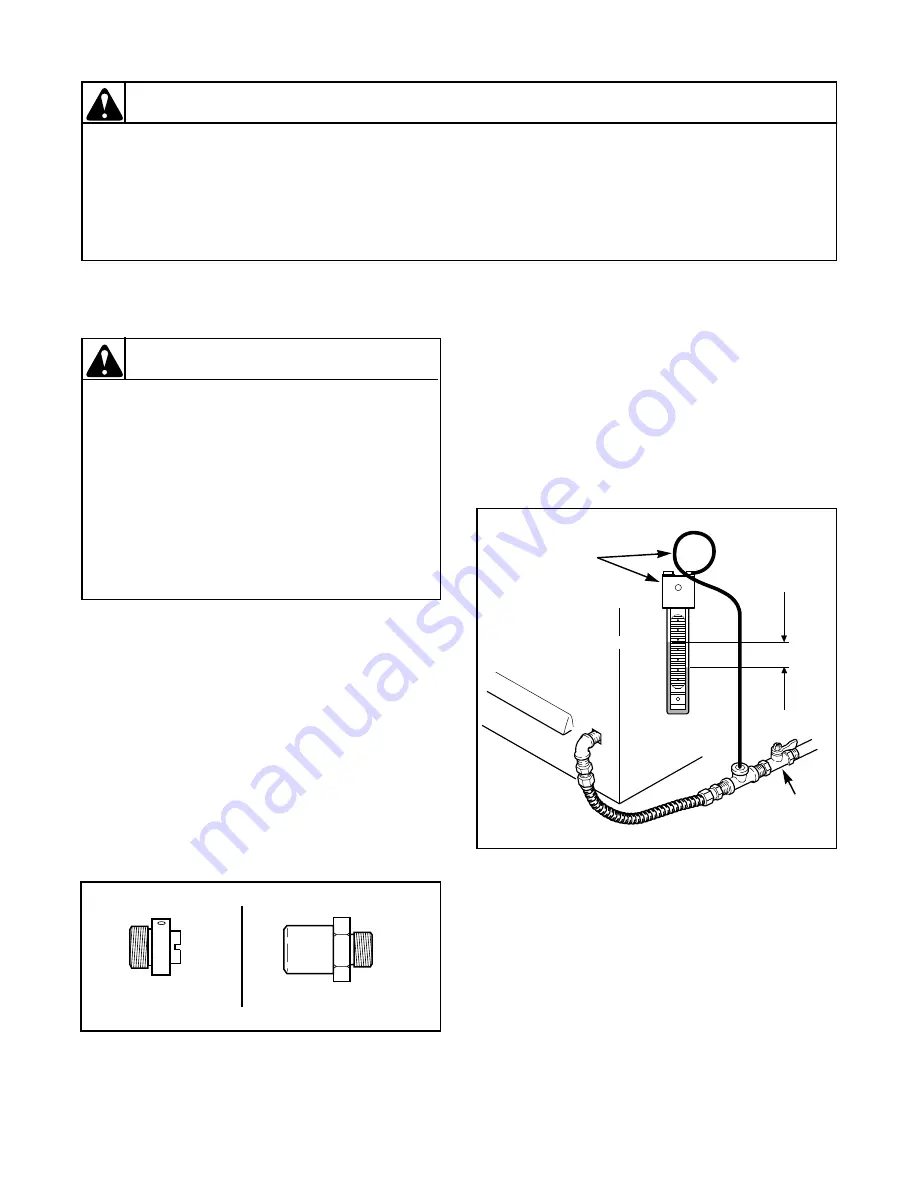
53277
45
Section 6 Gas Burner Conversion Procedures
To reduce the risk of electric shock, fire, explosion, serious injury or death:
• Disconnect electric power to the dryer(s) before servicing.
• Close gas shut-off valve to gas dryer(s) before servicing.
• Never start the dryer(s) with any guards/panels removed.
• Whenever ground wires are removed during servicing, these ground wires must be
reconnected to ensure that the dryer is properly grounded.
W001R1
WARNING
© Copyright, Alliance Laundry Systems LLC – DO NOT COPY or TRANSMIT
51. NO. 459P3 NATURAL GAS CONVERSION
KIT FOR “EG” MODELS/SERIES DRYERS
This kit consists of:
NOTE: Kit will convert one gas valve; 2 kits are
needed for converting upper and lower units.
Gas Input – 25,000 BTU/HR
NOTE: When converting the dryer gas valve to
Natural Gas, be sure the incoming gas supply line is
equipped with a pressure regulator (located ahead
of the dryer) that will maintain the gas supply to the
dryer at 6.5 ± 1.5 inches (16.5 ± 3.81 cm) water
column pressure, and a vent to the outdoors must be
provided. Remove pressure tap pipe plug and check
gas pressure by connecting a “U” tube manometer
(or similar pressure gauge) to the pressure tap.
Refer to Figure 44.
1 - 58768
Vent Screw
1 - 60417
Burner Orifice Spud (Metal
stamped #40
1 - 60512
Conversion Plate
1 - 60516
“Valve Converted to Natural Gas”
Sticker
2 - 60519
Natural Gas Stickers
1 - 4-88-26R1 Instructions
This conversion kit is to be installed by
AUTHORIZED DEALERS or DISTRIBUTORS
on their premises and in accordance with
the manufacturer’s instructions and all
codes and requirements of the authority
having jurisdiction. Failure to follow
instructions could result in serious injury
or property damage. The qualified agency
performing this work assumes
responsibility for this conversion.
W312
WARNING
55"
DRY966S
Vent Screw
Burner Orifice Spud
Figure 44
DRY961S
MANOMETER
6.5 ± 1.5
INCHES
PRESSURE
TAP