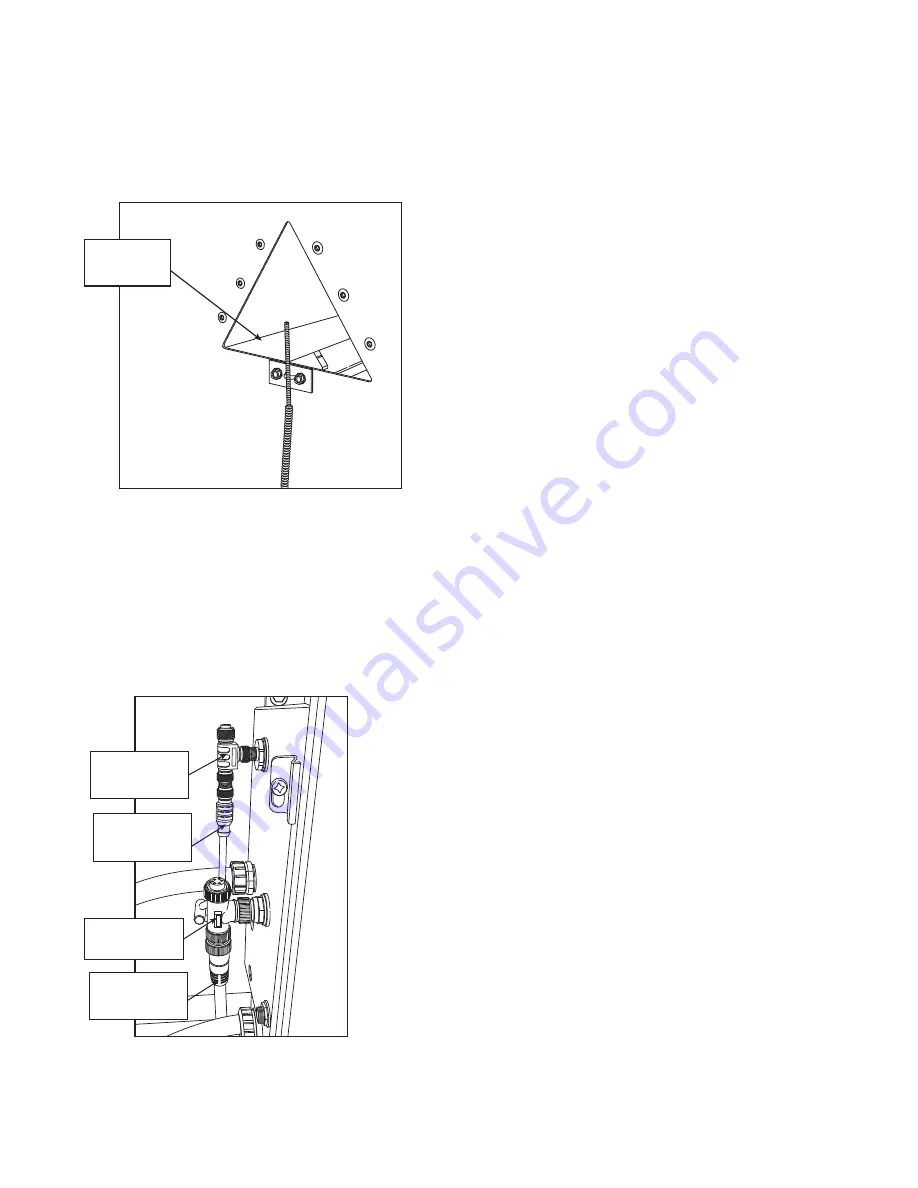
82
7713397 R2
4.7.4 Install the Dual Thermocouple Probe
The dual thermocouple probe is factory mounted for each dryer section. The probe measures temperature for
high-limit temperature control in each dryer section.
Figure 95.
Dual Thermocouple Probe
Dual Thermo-
couple Probe
4.7.5 Install Burner Box Cables*
*Shipped in the dryer crate.
• The yellow and gray cables and tees are used to connect the burner boxes to each other and to the main
electrical panel.
• Directly connect the gray cable to the top burner box. (Do not install the gray tee in the top burner box.)
Figure 96.
Burner Box Connections
GREY
CABLE
YELLOW
BURNER CABLE
TEE
GREY
COMMUNICATIONS
CABLE TEE
COMMUNICATIONS
YELLOW
BURNER
CABLE
CONTINUOUS-FLOW GRAIN DRYER – COMMANDER CONTROL
Содержание NECO D16106
Страница 2: ......
Страница 4: ...4 7713397 R2 CONTINUOUS FLOW GRAIN DRYER COMMANDER CONTROL...
Страница 121: ...7713397 R2 121 CONTINUOUS FLOW GRAIN DRYER COMMANDER CONTROL 8 LIMITED WARRANTY...