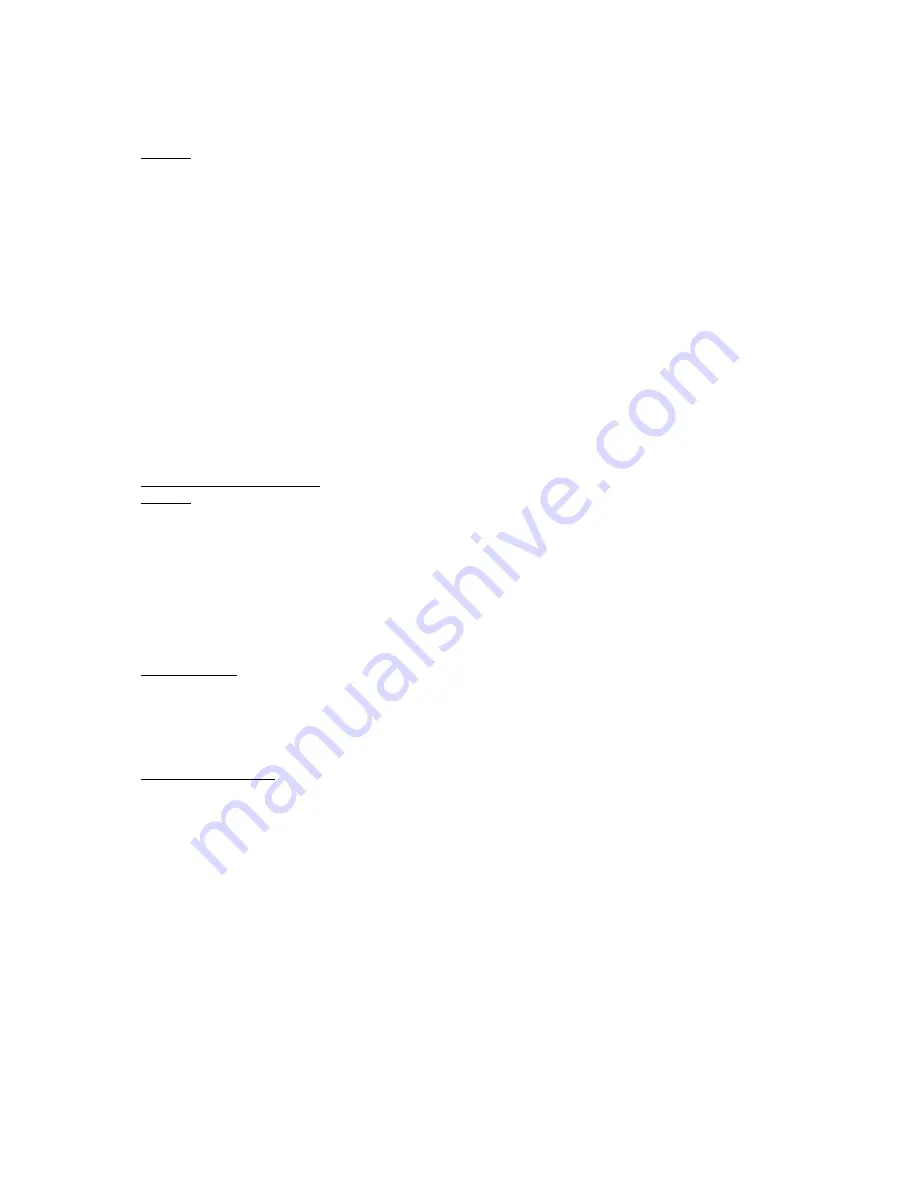
Document Q101, Revision W
(Printout Uncontrolled)
Page 4 of 23
4.0
QUALITY MANAGEMENT SYSTEM
General
ADTRAN has established a documented Quality Management System (QMS) to ensure control and continuous
improvement of the QMS processes. The QMS is set forth in this manual and is detailed in the reference procedures.
Referenced procedures also define the Product Life Cycle Model for all ADTRAN products, customer communication,
documentation requirements, internal auditing, manufacturing procedures, supplier evaluation and control,
performance measurements and implementing corrective and preventive action. The ADTRAN Quality Plan provides
an overview of the system.
The QMS within ADTRAN applies to interactions between, Engineering, Operations, Purchasing, Quality,
Sales/Marketing (includes Technical Support) and Training. The interaction of processes required for the QMS are
identified in Attachment 3.
The management of each functional group in the QMS is responsible for ensuring that quality consideration is an
integral part of all processes. Assuring compliance to the QMS, implementing actions necessary to achieve planned
results and continual improvement is a management responsibility.
The Purchasing organization is responsible for identifying and controlling all outsourced processes. Purchasing
ensures that these processes are identified within the QMS.
Documentation Requirements
(GEN05.1)
General
ADTRAN’s QMS documentation includes:
a)
ADTRAN’s Quality Policy and Quality Objectives,
b)
The Quality Manual,
c)
General Work Instructions, includes procedures required by TL9000,
d)
Departmental Work Instructions, includes procedures required by TL9000,
e)
Quality Records as required by ADTRAN and TL9000,
f)
Product and Service Documentation; and
g)
The Quality Plan
Quality Manual
This Quality Manual includes; the scope of the ADTRAN QMS, reference to documented procedures, and a
description of the interaction between the processes of the QMS. Corporate Quality Management maintains the quality
manual and ensures, as a minimum, an annual review. Acceptance by Top Management is recorded as the signature of
the Vice President of Quality.
Control of Documents
The documentation system requires operating policies and procedures to be documented, approved, periodically
reviewed and re-approved. Documentation changes are approved by the same organizations that approved the original
release. A description of the revision is included with each occurrence. (GEN05.1)
An Engineering Change Order (ECO) procedure defines the means of making changes to Engineering documentation,
as well as obtaining approvals. (GEN05.4)
The Document Control organization is responsible for distribution of new and changed documents.
Customer supplied documents and data are identified as such and controlled in the same manner as ADTRAN
documentation. (GEN05.1 and GEN05.12)
Each manager is responsible for ensuring that the most current revision of applicable documentation is available where
used.