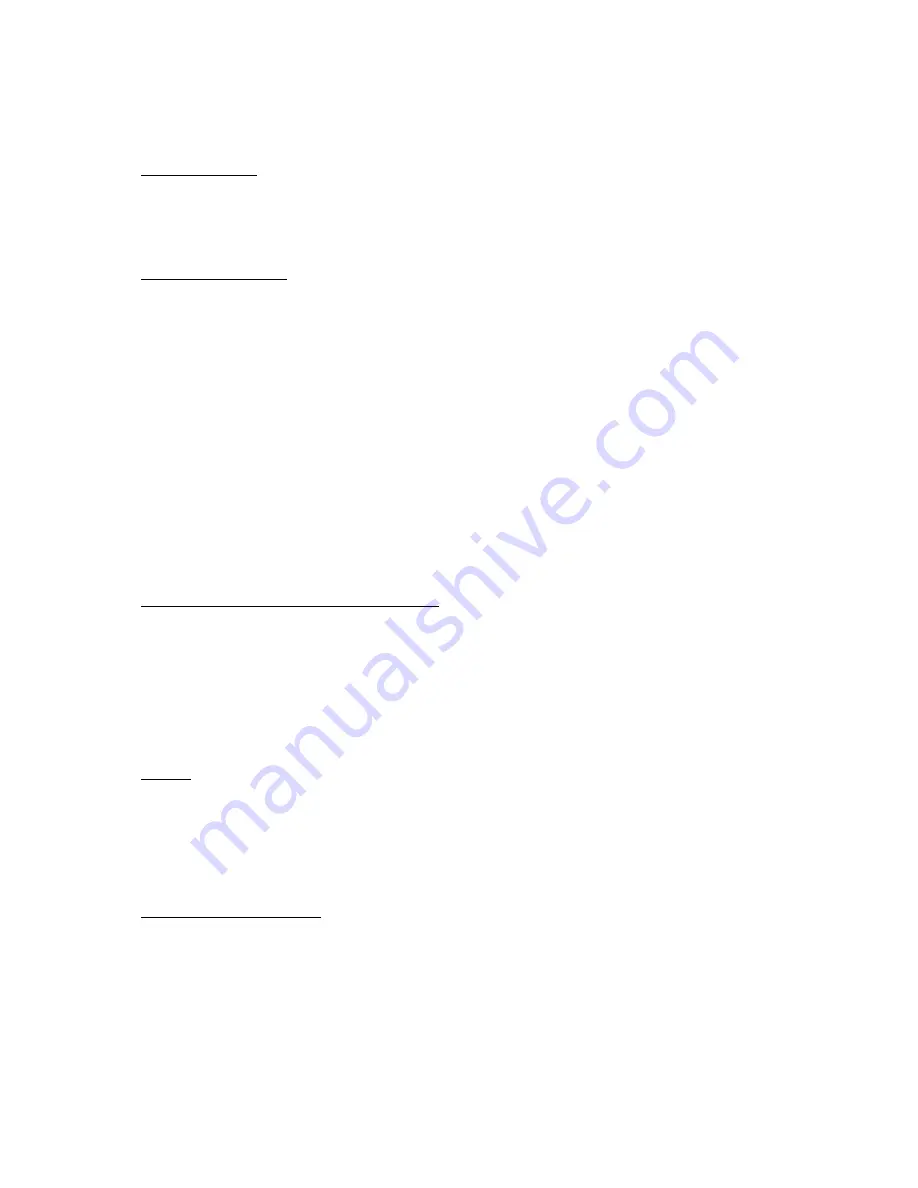
Document Q101, Revision W
(Printout Uncontrolled)
Page 12 of 23
during the manufacturing process. Traceability is then maintained within ADTRAN’s Management Information
System by part number for data collection purposes, trace design changes, and for product recalls.
Customer Property
Each customer-supplied product is assigned a unique ADTRAN part number. Definition of the supplied product is also
required so that Component Inspection can confirm the product meets specified requirements. The unique ADTRAN
part number allows for separation in storage and maintenance, if required. Procedures are in place to ensure that Sales
and Marketing notify the customers of product issues. (GEN07.1)
Preservation of Product
Material handling includes methods and equipment required to move or store purchased, in-process, manufactured, or
completed material. Adequate handling methods and procedures are proposed and used to prevent damage, loss,
deterioration or degradation of the product. These procedures may include the use of special boxes, containers, and
Electrostatic Discharge (ESD) controls. Manufacturing Engineering is responsible for preparing and implementing
handling procedures with Quality Engineering approval. (GEN15.1)
ADTRAN documentation defines the steps to be taken for proper handling of ESD sensitive material and assemblies,
both within ADTRAN and when transported to and from our subcontractors. (GEN09.5)
Quality Assurance performs Out-of-Box audits, per documented procedure(s), to confirm product, labeling and
packaging quality. (QA10.5)
The Materials manager has the responsibility for technical direction of material storage to minimize the possibility of
damage, corrosion, deterioration, or contamination.
Handling and storage practices are defined in ADTRAN’s Stockroom procedure(s). A first-In, First-out (FIFO)
inventory control system is used. Items with definitive shelf life are stipulated and controlled. (GEN09.5, GEN15.1)
Control of Monitoring and Measuring Equipment
ADTRAN uses an outside service to perform equipment calibration a minimum of two times a year. Each service
results in calibration of a portion of the equipment requiring calibration. Primarily, each piece of equipment will be
calibrated once each year. The frequency may be changed for specific equipment based on history.
The Corporate Quality department maintains a listing of all equipment requiring calibration. The listing is reviewed by
Quality on a regular basis. In addition, process audits require confirmation of calibration status of equipment. All
inspection, measuring, and test equipment that do not require calibration are identified as such. (GEN11.1, GEN11.6)
8.0
MEASUREMENT, ANALYSIS AND IMPROVEMENT
General
Statistical techniques and team tools are used throughout ADTRAN processes to assure process controls and
continuous improvement, as well as verification of results. This data is reviewed regularly to determine appropriate
changes required to cause consistent improvement.
Metrics are collected and submitted to the Quest Forum by the Customer Quality Engineer, or designated individual,
per the TL9000 Quality Management System Measurements handbook (current release). (GEN21.3)
Monitoring and Measurement
Methods have been established to collect data from customers concerning their satisfaction with ADTRAN products
and services. This data is reviewed continuously by Sales and Marketing, and during Management Reviews of the
QMS.
ADTRAN collects data on delivery and customer response times. This data is reviewed weekly and/or monthly by the
responsible management and during management review.