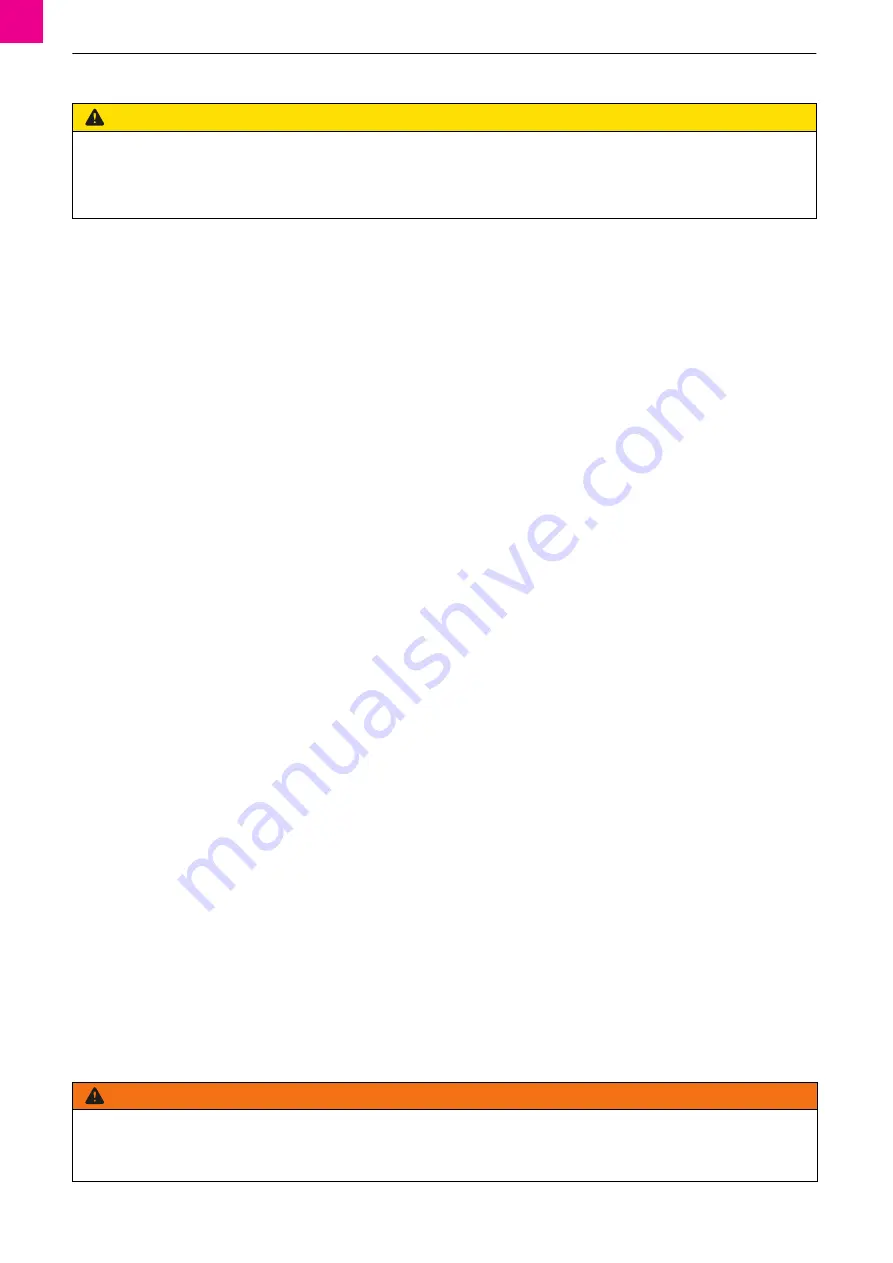
EN
-
6
5 Operation
ABITIG
®
Little
4.3
Equipping the welding torch, Fig. 1
A gas lens can also be used instead of the collet housing. Owing to its design, it will producealaminar gas flow.
4.3.1
ABITIG
®
Little 24 G/24 W/9/17/25:
1
Screw the collet housing with collet into the torch body.
A gas lens can also be used instead of the collet housing. Owing to its
design, it will producealaminar gas flow.
2
Screw the back cap with the tungsten electrode into the torch body.
3
Screw on the gas nozzle.
Step 2 is not required with the ABITIG
®
Little 24 G and 24 W
4.3.2
ABITIG
®
Little 150/260 W:
1
Insert the electrode holder into the torch body.
2
Screw the back cap with the tungsten electrode into the torch body.
3
Screw on the gas nozzle.
4.3.3
ABITIG
®
Little 90/180 W:
1
Insert the electrode holder into the torch body.
2
Screw the back cap with the tungsten electrode into the torch body.
3
Push on the gas nozzle.
4.4
Shortening the tungsten electrode
The electrode type is set by EN ISO 6848.
The electrode length depends on the torch type.
The welding performance is affected by the selection of the tungsten
electrode and by wear.Asmooth, groove-free sharpened end of the tungsten
electrode hasapositive effect on the welding result.
4.5
Sharpening tungsten electrodes, Fig. 3
Sharpening the tungsten electrode depends on wear and must therefore be
carried out when required.
► When sharpening the tungsten electrode, useasharpening device with
the following properties:
— Diamond disc
— Point sharpened longitudinally through the centre axis
— Automatic regulation of the tungsten electrode drive by gravity
— Can be set for all electrode diameters
— Offers continuous angle adjustment
4.6
Connecting the cable assembly
1
Plug the cable assembly connector into the welding power source and
secure it withaconnection nut.
2
Properly mount the connections for coolant supply/return, shielding gas
and control lead connector.
4.7
Connecting the coolant hoses
1
Connect the coolant supply (blue) and coolant return (red).
2
Check the coolant’s minimum fill level.
► Recommendation: Use ABICOR BINZEL coolants from the BTC range.
► To prevent damage to the welding device, do not use deionised or
demineralised water.
► Bleed the coolant circuit upon commissioning and when replacing the
cable assembly.
4.8
Bleeding the coolant circuit
1
Place the collection receptacle under the connection for the coolant
return (red).
2
Disconnect the coolant return hose from the cooling unit and hold it over
collection receptacle.
3
Seal the coolant return hose’s opening.
4
Abruptly open then seal the coolant return hose’s opening several times
until the coolant flows into the collection receptacle continuously and
without air bubbles.
5
Reconnect the coolant return hose to the cooling unit.
4.9
Connecting the shielding gas and setting the gas volume
The type and amount of shielding gas used depend on the welding task and
the gas nozzle geometry.
1
Select the appropriate shielding gas for the welding task.
2
Briefly open the valve on the gas supply then close it again to air-blast
away any dirt on the connector.
3
Connect the shielding gas to the welding device as per the
manufacturer’s instructions.
4
Adjust the shielding gas volume to the gas nozzle used and the welding
task and save the setting.
5 Operation
CAUTION
Risk of injury from the sharpened electrode
The sharpened electrode is pointed and can cause puncture injuries.
► Keep your hands away from the electrode tip.
► Hold the electrode tip away from your body.
► Wear the correct protective gloves.
WARNING
Risk of injury due to electromagnetic fields
The device can produce electromagnetic fields that could impact the proper function of cardiac pacemakers and implanted defibrillators.
► Do not use the device if you haveapacemaker or an implanted defibrillator.
► Only use the device in industrial zones in accordance with DIN EN 61000
-
6
-
3.