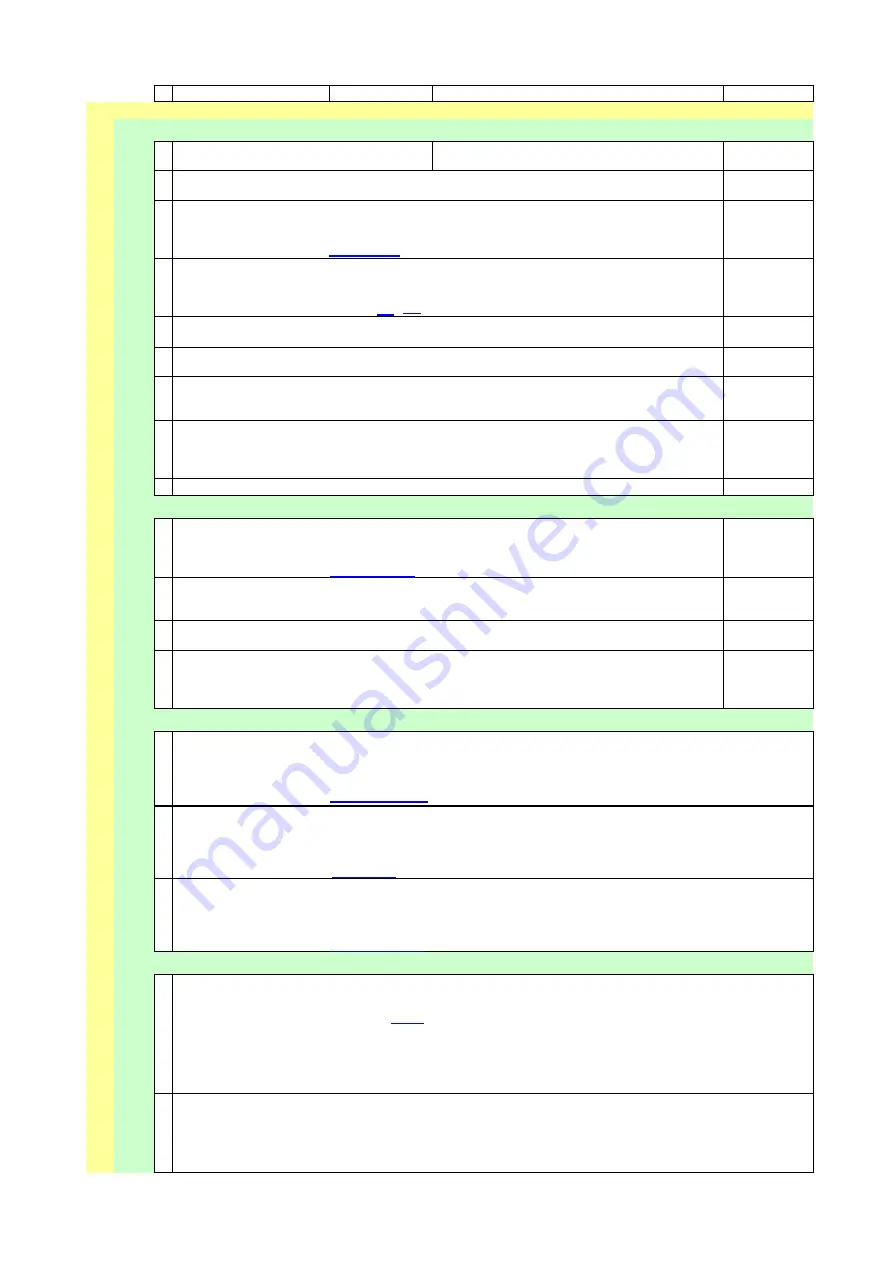
Planning and Installation Guide
Technical Description
V6
Phase
D
Point to be Checked
Further Details
Remark Hints
Drawing
4. Commissioning
4.1 Power Supply
4.1.1
Choose Master/Slave setting
Chose "Master" operation mode at the first device,
"Slave" at all other devices
4.1.2
Set phase angle to 0/90°
Choose a phase value (0°/90°) matching the orien-
tation in relation to the "Master" primary loop (=0°).
4.1.3
Set current chosen during
planning
(DIP-switch S1)
See "Planning and
Installation
Guidelines"
Chapter 4.2
Set the appropriate current value matching the size of
the connected primary loop(s) for each power supply.
4.1.4
Document chosen current
value and associated pace
maker distance in application
documentation
See "Planning and
Installation
Guidelines"
Chapter 1.3 / 4.2
4.1.5
Optional: Connect alarm
output
Connect to an input of the control system/ PLC.
Contact opens in case of malfunction of power supply
4.1.6
Tighten all PG "Threads" ,
Put caps on unused ones
To achieve IP65 class
4.1.7
Switch-on the main switch /
fuse
The operation LEDs of the power supplies start to blink
green. After ~15 sec. constantly green
(check manual if red LED are on/blinking)
4.1.8
Check correct function
Use a sensor w. communication module to check
power (orange LED if tri green LED if
unconfigured)
!
The communication module needs up
to 8 sec. to start-up or stop operation.
4.1.9
Mount the cover
4.2 Configure PLC/FBP
4.2.1
- Copy the *.gsd -file for the
fieldbus plug into the GSD
subdirectory of the host
software
See "Technical
Description for
(FBP)
FieldBusPlug"
The *.gsd file contains a description of the node, I/O
and diagnostic data for the PLC (and is a readable text
file). It can be found on the Documentation CD
4.2.2
Start the host software, (or
actualize the directory to
choose the *.gsd File from)
4.2.3
- Map the wireless input
module into the fieldbus
by assigning the node address in the host software
4.2.4
- In the host software, select
the WDI100 as the I/O for
that node and set I/O
addresses
by turning on the auto address feature or manually
address with the auto addressing turned off
4.3 Settings of Input Module WDI100 (SET Menue)
4.3.1
Set field bus address on WDI See "Planning and
Installation
Guidelines"
Chapter 3.8
FIELDBUS ADDR
4.3.2
Set Cell-ID, set the desired
ID-number for this Cell
(1-60)
See "Planning and
Installation
Guidelines"
Chapter 3.8
CELL-ID
Make sure to not have double Cell-IDs in a radius of
~16m !!
4.3.3
Set "FIELDBUS ADDR" to
LOCAL
See "Planning and
Installation
Guidelines"
Chapter 3.8
CFG LOCAL / FB
Locally stored configuration is used instead of getting
configuration for the sensors and CELL-ID from the
field-bus/PLC. (May overwrite your local setting
otherwise!)
4.4 Configure Sensors
4.4.1
Configure sensors in the
(CFG Menu)
See "Planning and
Installation
Guidelines" p. 2
4.4.2
Check correct sensor
function (RUN Menu)
- Go to CFG Mode (press ESC and OK simultaneously from RUN
mode), select CFG, (press OK to enter CFG mode)
- Choose sensor address (1-120) (to be given to a certain sensor, only
free addresses are available) Assign address: I. Press OK (address
blinks), II. Press membrane switch on unconfigured sensor (green LED =
on), it will receive selected address and Cell-ID.
- The next free address is blinking on the WDI100: Press another
sensor's membrane switch to assign this address, ....
- Choose the sensor to be triggered with /\ \/ (in RUN mode of WDI)
- Trigger the sensor head with a metal object
-Observe status change in RUN mode on WDI display
- Check Wink function by pressing OK in the RUN mode or by pressing
a membrane switch of a sensor WSIX
- Leave RUN Mode: hold ESC and press OK at the same time
- Select the SET Mode on the WDI100 panel (with /\ or \/ buttons)
- Select FIELDBUS ADDR, set fieldbus address for the WDI100/FBP to
the same address that was selected in the controller or PLC
- FieldBusPlug LED(s) change Red -> Green: communication OK
Wireless Proximity Switches / issued: 09.2004
Checklist A 3 / 3