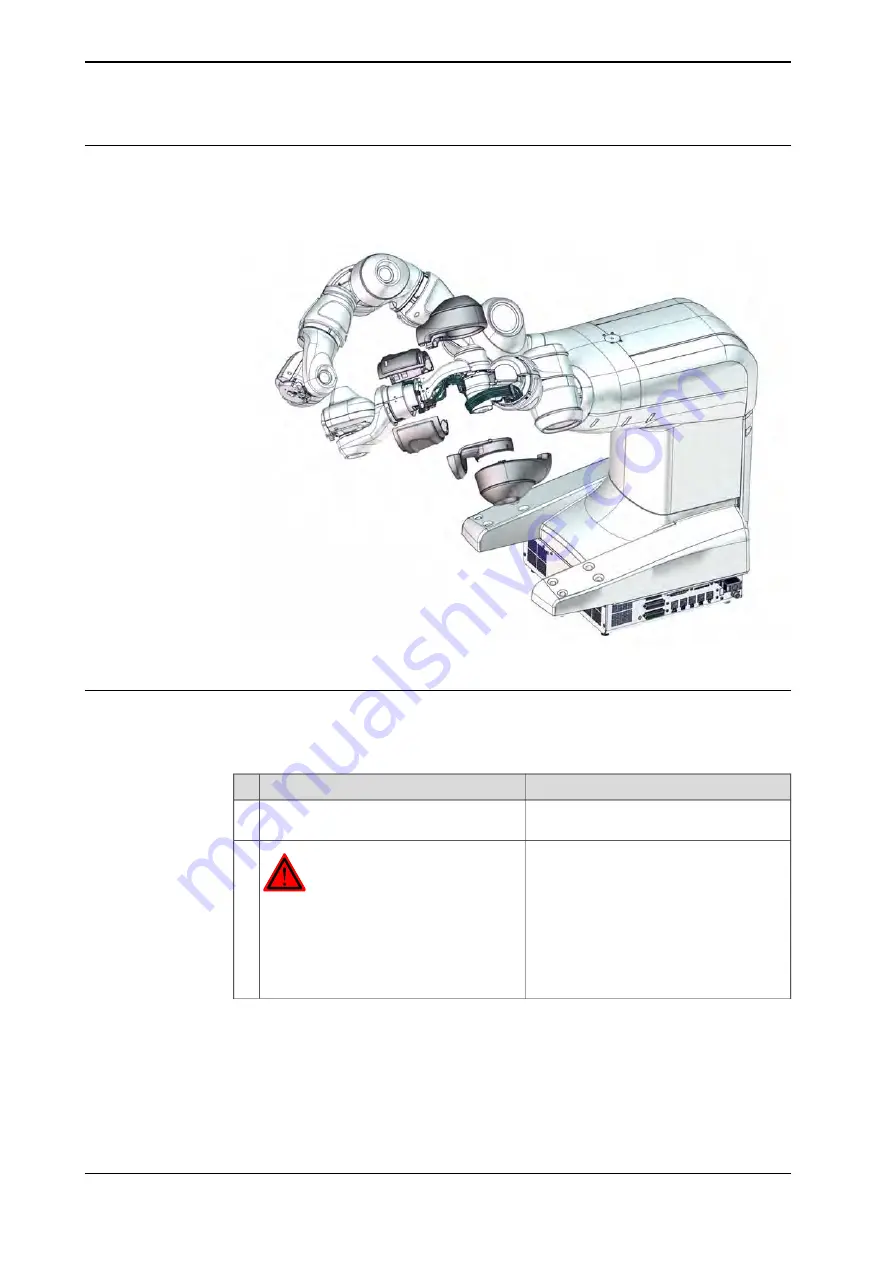
Covers to be removed for access
This figure shows an overview of which covers to remove to get access to the
spare part. Detailed instructions of how to remove the covers are found in the
removal procedure.
xx1500000491
Removing the hall sensor
Use these procedures to remove the hall sensor.
Preparations before removing the hall sensor
Note
Action
Jog the robot so that the covers can be
easily accessed and removed.
1
DANGER
Turn off all:
•
electric power supply
•
air pressure supply
to the robot, before starting the repair work
on the robot.
2
Continues on next page
256
Product manual - IRB 14000
3HAC052983-001 Revision: D
© Copyright 2015 - 2016 ABB. All rights reserved.
4 Repair
4.5.4 Replacing the axis-3 hall sensor
Continued
Содержание IRB 14000
Страница 1: ...Product manual IRB 14000 ...
Страница 2: ...Trace back information Workspace R16 2 version a5 Checked in 2016 09 08 Skribenta version 4 6 318 ...
Страница 8: ...This page is intentionally left blank ...
Страница 16: ...This page is intentionally left blank ...
Страница 416: ...This page is intentionally left blank ...
Страница 436: ...This page is intentionally left blank ...
Страница 440: ...This page is intentionally left blank ...
Страница 456: ......
Страница 457: ......