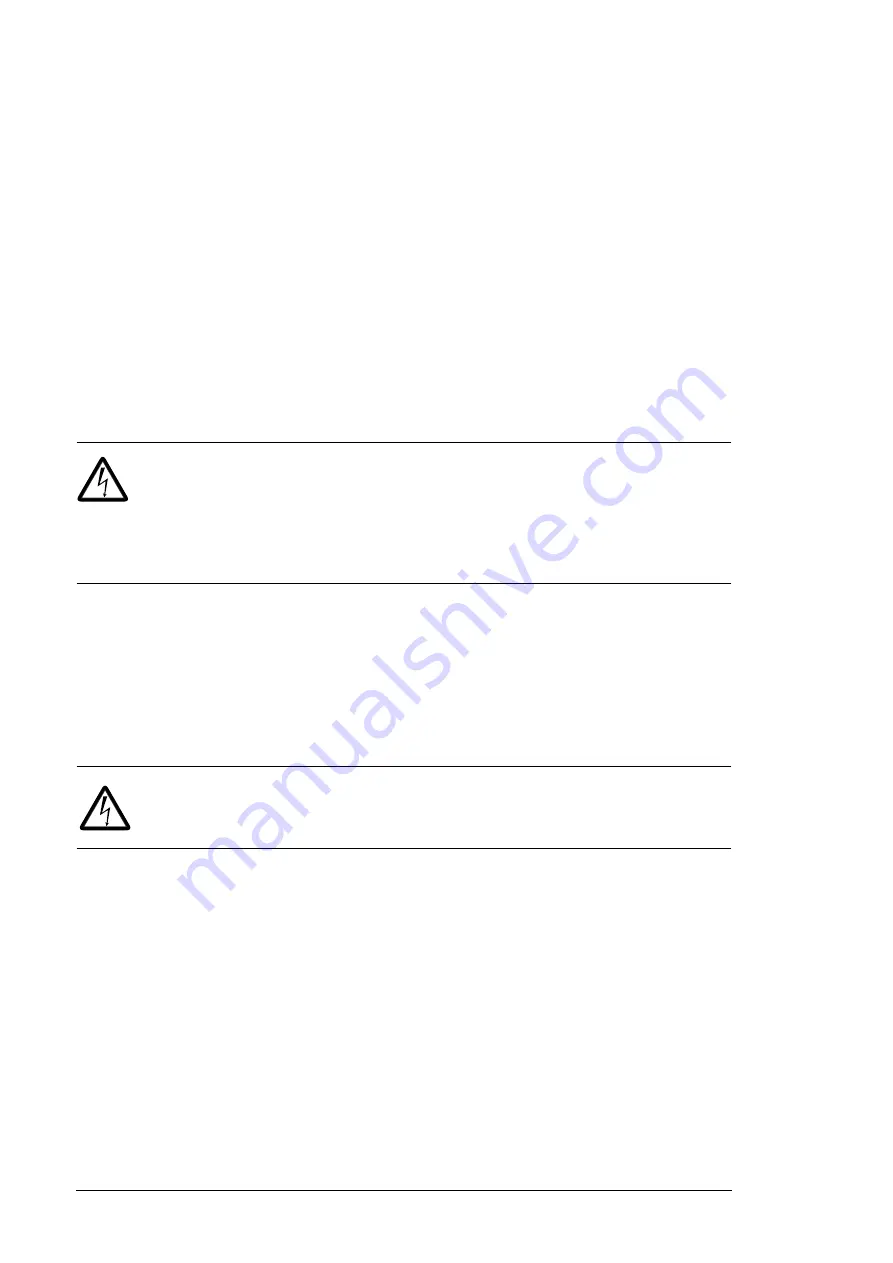
72 Guidelines for planning the electrical installation
Using a contactor between the drive and the motor
Implementing the control of the output contactor depends on how you select the drive to
operate. See also section
Implementing a bypass connection
.
When you have selected to use DTC motor control mode and motor ramp stop, open the
contactor as follows:
1. Give a stop command to the drive.
2. Wait until the drive decelerates the motor to zero speed.
3. Open the contactor.
When you have selected to use DTC motor control mode and motor coast stop, or scalar
control mode, open the contactor as follows:
1. Give a stop command to the drive.
2. Open the contactor.
WARNING!
When the DTC motor control mode is in use, never open the output
contactor while the drive controls the motor. The DTC motor control operates
extremely fast, much faster than it takes for the contactor to open its contacts.
When the contactor starts opening while the drive controls the motor, the DTC control will
try to maintain the load current by immediately increasing the drive output voltage to the
maximum. This will damage, or even burn the contactor completely.
Implementing a bypass connection
If bypassing is required, employ mechanically or electrically interlocked contactors
between the motor and the drive and between the motor and the power line. Ensure with
interlocking that the contactors cannot be closed simultaneously. The installation must be
clearly marked as defined in IEC/EN 61800-5-1, subclause 6.5.3, for example, "THIS
MACHINE STARTS AUTOMATICALLY".
WARNING!
Never connect the drive output to the electrical power network. The
connection may damage the drive.
Содержание ACS880-04F
Страница 1: ...ABB industrial drives Hardware manual ACS880 04F drive modules ...
Страница 4: ......
Страница 24: ...24 Introduction to the manual ...
Страница 46: ...46 Guidelines for planning the mechanical installation ...
Страница 102: ...102 Installation checklist ...
Страница 106: ...106 Fault tracing ...
Страница 135: ...Technical data 135 Declaration of Conformity ...
Страница 136: ...136 Technical data ...
Страница 140: ...140 Technical data ...
Страница 142: ...142 Dimension drawings Standard configuration IP20 UL Open Type ...
Страница 143: ...Dimension drawings 143 Drive module with options E208 and H370 IP20 UL Open Type ...
Страница 144: ...144 Dimension drawings Drive module with options 0B051 E208 0H371 IP00 UL Open Type ...
Страница 145: ...Dimension drawings 145 Drive module with options 0B051 E208 0H371 C217 IP00 UL Open Type ...
Страница 146: ...146 Dimension drawings Drive module with options 0B051 0H371 IP00 UL Open Type ...
Страница 147: ...Dimension drawings 147 Mounting plate 3AXD50000038119 ...
Страница 148: ...148 Dimension drawings 3AXD50000038119 ...
Страница 149: ...Dimension drawings 149 External control unit 3axd50000011687 ...
Страница 150: ...150 Dimension drawings ...
Страница 164: ...164 Safe torque off function ...