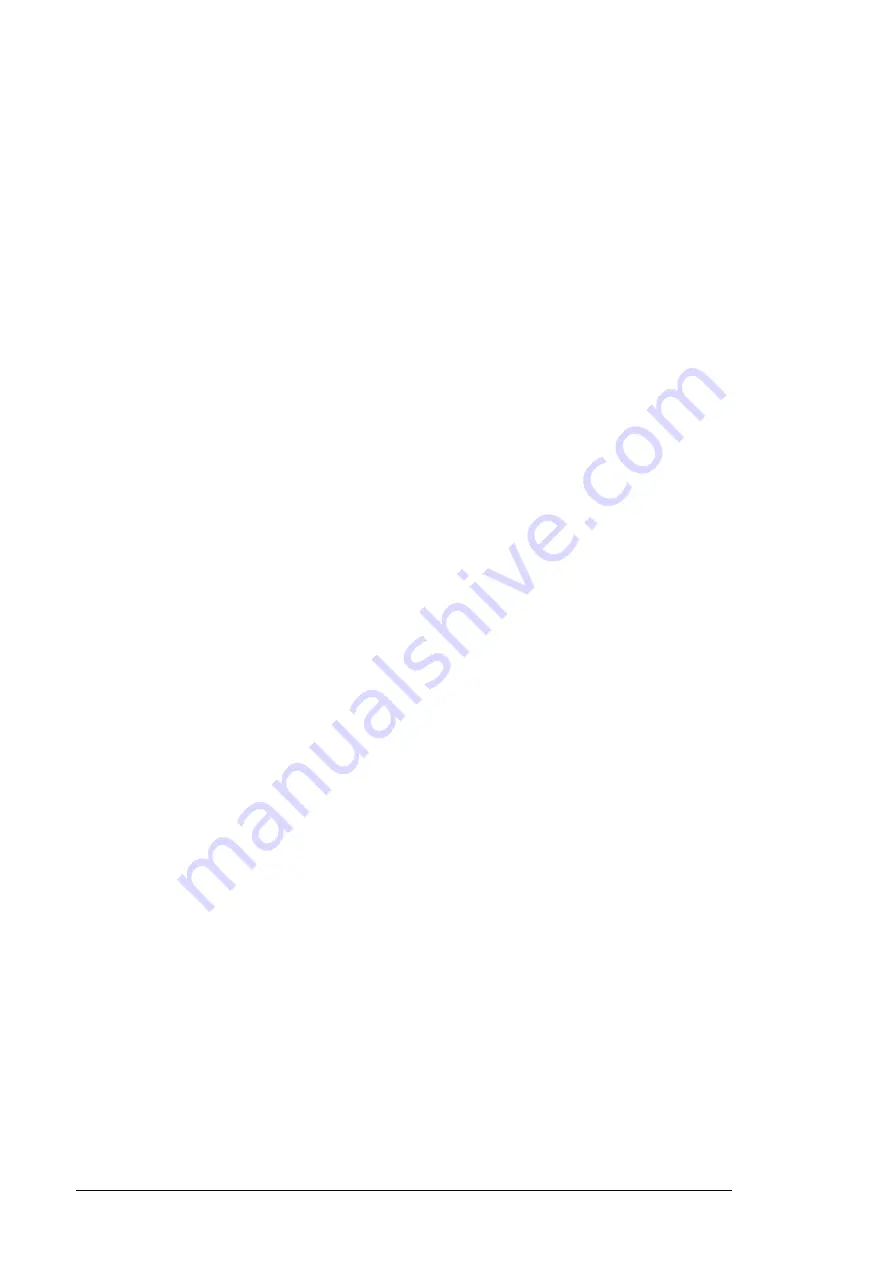
114 Tracing the source of warnings, limits and faults
Faults
The converter protects itself with many functions. When a protection function is activated,
the converter is immediately stopped (tripped) to avoid damages. A fault does not
necessary mean that there is any material failure in the converter.
How to identify the fault and what to do in a specific fault situation
Both RMIO and NDCU board contains a fault logger. The latest faults and warnings are
stored together with the time stamp at which the event was detected. The fault logger
collects 64 of the most recent available pieces of information concerning faults (such as
fault, warning, reset and system messages) into the fault buffer in the RAM memory. The
latest 16 inputs are stored to the flash memory at the beginning of an auxiliary power
supply loss if an in24 V power supply is used.
Both RMIO and NDCU board also contains data loggers 1 and 2. They are used to monitor
signals and to store them for later retrieval and analysis. The contents of the data loggers
are stored to the RAM memory.
The fault logger can be browsed in DriveWindow under the
Fault
tab and the data loggers
under the
Data logger
tab. For more information, refer to
DriveWindow user’s manual
[3BFE64560981 (English)].
Compare the warning and fault messages of the fault logger to the messages listed in the
firmware manual. Most warning and fault causes can be identified and corrected using the
information in the fault tracing tables.
Before contacting ABB, see section
Warning and fault messages
Refer to
•
ACS800 IGBT supply control program firmware manual
[3AFE68315735 (English)]
•
ACS800 grid-side control program firmware manual
[3AUA0000075077 (English)]
•
ACS800-67(LC) doubly-fed induction generator control program firmware manual
[3AUA0000071689 (English)].
Содержание ACS800-67
Страница 1: ...ABB wind turbine converters System description and start up guide ACS800 67 wind turbine converters ...
Страница 4: ......
Страница 76: ...76 Start up with medium voltage stator ...
Страница 99: ...Practical examples 99 1 4 4 3 2 5 6 7 ...
Страница 106: ...106 Practical examples Counterclockwise rotation at drive end D end Power cabinet Encoder ...
Страница 118: ...118 Tracing the source of warnings limits and faults ...
Страница 120: ...Contact us www abb com windconverters 3AUA0000095094 Rev B EN 2017 12 31 ...