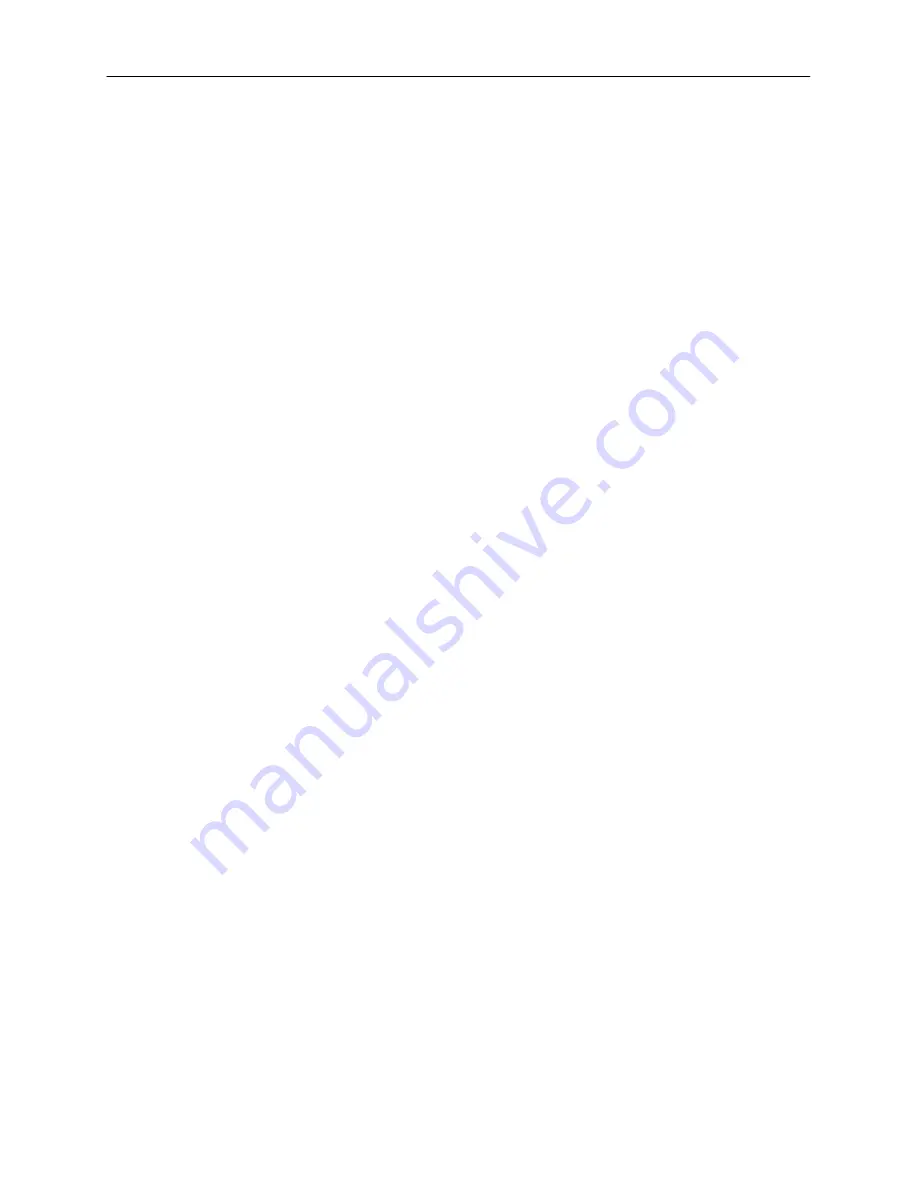
Troubleshooting
Guide
9|
Page
•
The
flow
adjustment
valve
could
be
obstructed
due
to
hard
water
scale
or
debris,
causing
lower
than
expected
water
flow.
Verify
water
flow
with
a
graduated
container
or
with
the
remote
temperature
controller,
if
one
is
installed.
•
The
output
thermistor
could
be
compromised.
This
component
may
be
checked
by
entering
the
Diagnostics
Mode
on
a
remote
controller,
if
one
is
installed.
Turn
power
off
to
the
unit
and
run
cold
water
through
it;
check
to
see
if
the
inlet
and
outlet
temperatures
read
the
same
on
the
remote.
For
instructions
on
how
to
do
this,
refer
to
the
Maintenance
Sheet,
packaged
with
every
water
heater
and
located
behind
the
front
panel
of
the
unit.
TEMPERATURE
FLUCTUATES
WHEN
A
FIXTURE
IS
OPENED
•
Make
sure
the
unit
is
installed
properly
using
the
Proper
Installation
section
(p.
6)
of
this
guide.
•
Check
the
flow
and
temperature
right
at
the
unit
at
the
pressure
relief
valve.
If
the
flow
rate
and
temperature
are
correct
at
the
PRV,
then
the
problem
resides
elsewhere
in
the
plumbing
line.
The
following
could
be
plumbing
line
problems:
o
Check
for
cross
plumbing
between
cold
water
lines
and
hot
water
lines.
See
the
Procedures
section
(p.
21)
for
instructions.
o
Check
to
see
that
a
check
valve
is
installed
between
the
pump
discharge
and
the
connection
to
the
cold
water
supply.
Inspect
the
check
valve
for
proper
operation.
If
there
isn’t
one
installed,
or
if
it
is
malfunctioning,
cold
water
may
be
back
‐
feeding
into
the
system.
o
Problems
with
a
recirculation
system:
Check
that
a
check
valve
is
installed
between
the
pump
discharge
and
the
connection
to
the
cold
water
supply.
Check
to
see
if
the
pump
is
operating
properly.
Check
for
air
cavitation.
The
pump
will
be
very
hot
or
chattering.
Check
the
directional
indicator
on
the
pump
flange.
Check
the
sizing
of
the
pump
–
a
minimum
flow
of
2
gpm
is
required.
•
Check
gas
supply
o
Verify
the
gas
supply
lines
are
sized
for
the
maximum
Btu/h
demand,
as
indicated
in
the
Proper
Installation
section
(p.
6)
of
this
guide
(See
the
specification
page
p.3
at
the
beginning
of
this
manual
for
gas
input
rating).
o
For
LP
models,
there
may
not
be
enough
gas
left
in
the
propane
tank.
o
Verify
that
the
supply
gas
pressure
is
within
specification,
not
only
when
the
heater
is
in
standby,
but
while
the
heater
is
running
on
maximum
fire
as
well.
This
may
be
caused
by
a
malfunctioning
gas
supply
regulator.
•
Venting
o
Verify
that
the
exhaust
venting
is
installed
to
manufacturer’s
specification.
o
Verify
that
the
vent
run
does
not
exceed
the
maximum
limit
(50
ft.)
•
The
filter
on
cold
water
inlet
should
be
clean;
look
for
signs
of
hard
water
scaling.
•
Check
to
make
sure
that
the
clear
tube
between
the
proportional
gas
valve
and
the
bottom
of
the
combustion
chamber
is
connected.
•
On
well
systems
or
even
on
some
city
water
systems,
water
pressure
fluctuations
(especially
on
low
flow)
of
8
to
10
psi
will
result
in
flow
rate
fluctuations,
which
will
in
turn
result
in
minor
temperature
fluctuations.
•
Flow
sensor
or
water
control
valve
may
be
compromised.
Contact
the
Technical
Department.