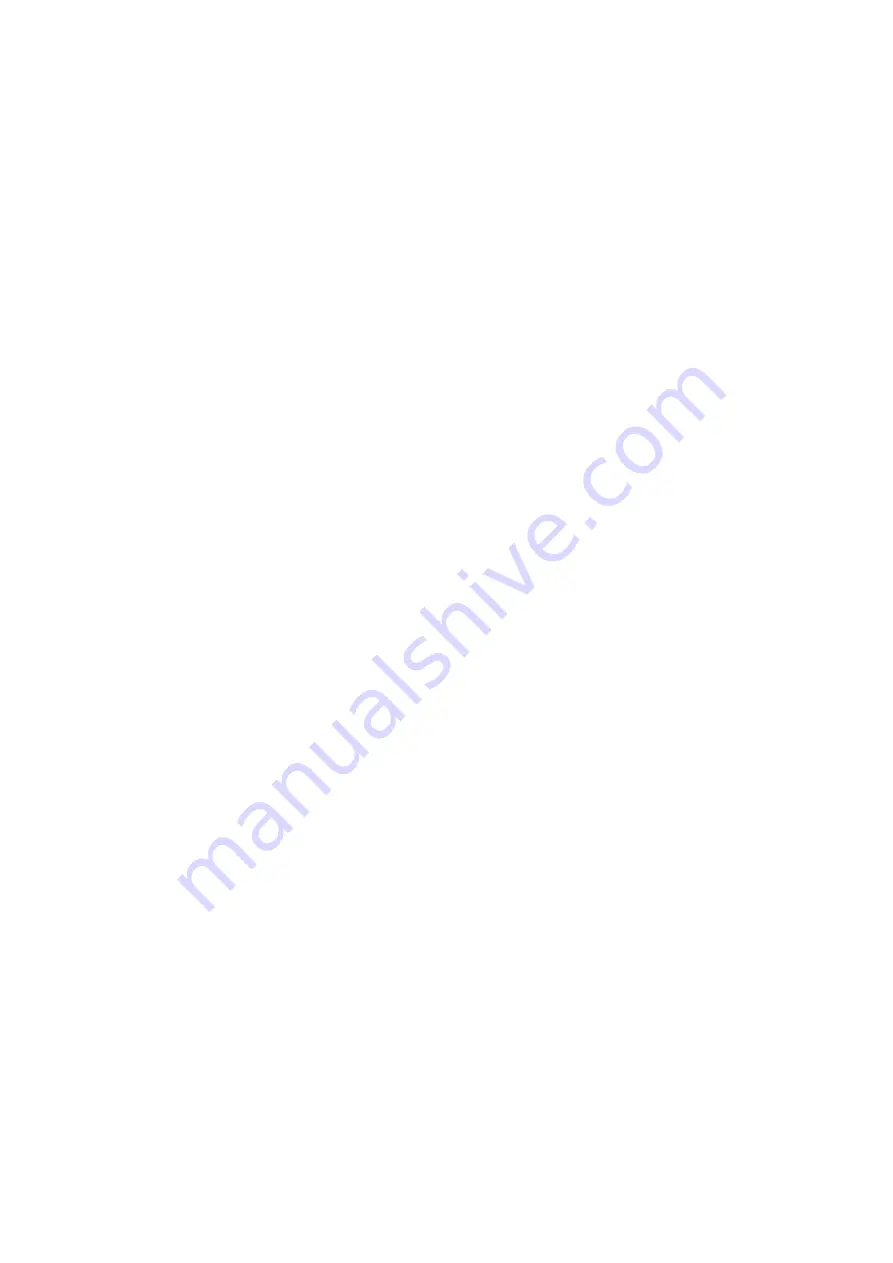
13
If, during adjustment, the torque is reached in the end-limit position, the torque must be left by means of a hand
wheel.
– The actuator is set to position Closed and position Closed is stored by long pressing of push-button C
(without
entering the Menu).
– The actuator is set to position Open and position Open is stored by long pressing of push-button O.
– The calibration routine is started by means of push-button P
(in remote control)
that, in the three-position
regulation, will measure actual inertial masses of the system and store them into the memory of the control
unit. In the two-position regulation, pressing of push-button P only cancels the error of Calibration.
– In recording the end-limit positions, signalling relays and the position transducer are also set.
– In case the actuator stroke is to be increased and the switching off is set to “from position”, the actuator will
switch off during shifting in position O or 100 %. To further change the position, press C or O, and, while
keeping it depressed, the actuator can be further shifted. After required position is reached, it is stored to
memory by pressing push-button C or O.
Parameters that can be changed by user are set by manufacturer as follows:
1. Tripping torques:
100% or required value
(it is not recommended to change the value
without consulting the supplier of the valve, etc.).
2. Relay 3 and relay 4:
signalization SZ 1 % and SO 99 % of stroke
3. Time of blocking:
2 – 8 s according to rate of actuator shifting
4. Position of blocking:
5 % of stroke from end-limit positions
(it is not recommend to change
the value by more than 10 %)
5. Characteristics of position transducer:
closed 4 mA, open 20 mA
6. Relay READY:
w not remote
In version CONTROL:
1. Setting of control signal:
closed 4 mA, open 20 mA
2. Insensitivity of actuator in regulation:
1 %
(it is not recommended to set insensitivity higher than 3 %)
3. Response in case of loss of control signal:
stop
4. Way of switch off in end-limit positions:
PO + PZ
Overview of MENU
BROWSING THROUGH MENU
– The setting regime is entered by pressing and keeping depressed push-button
MENU for at least 2 s; LED1
is then lit on.
– Shortly press
MENU to select the basic MENU – menu M1 to M8
(LED1 signalizes the menu number);
by short
pressing of P, O, C they are entered
(LED2 signalizes particular parameter).
– Shortly press P to select required value of the parameter. In case the parameter can be set to several values, they
are changed by short pressing of P
(number of blinking of LED2 indicates its value).
Keep pressing of P to record
the chosen parameter; the record is confirmed by lighting on of LED2.
– Shortly press
MENU to gradually set the required menu and parameters.
– After setting all required parameters, exit the setting menu by pressing and keeping depressed push-button
MENU for at least 2 s. The setting menu will also be left in case that no push-button is pressed within 1 mi-
nute.
MENU 1 – Setting of tripping torques
– After entering the menu by means of push-button C or O, select required torque.
– Shortly press P to select the set value of the parameter 50 – 100 %
(5 – 10 blinking of LED2)
and keep pressing
push-button P to store the parameter to memory.