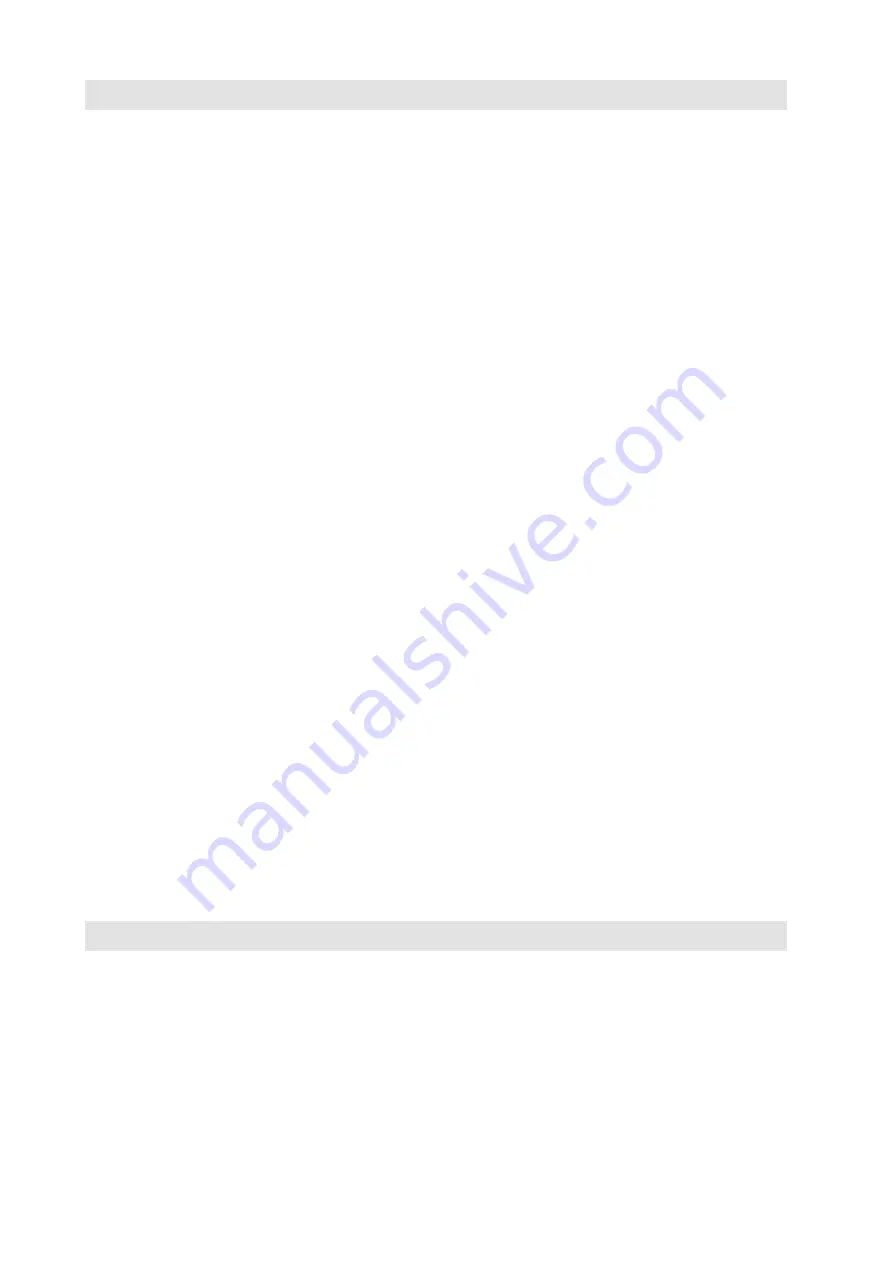
27
DMS2
Main properties of DMS2:
– Complete control of the actuator run of the two- and three-position regulation or connection to the industrial bus
Profibus.
– Synoptic signalization of operation and service data on the character LCD display 2 x 12.
– Autodiagnostics of error reports on the LCD display, memory of recent failures and number of occurrences of
respective failures.
– Setting of parameters by the PC program and by local control provided that the actuator is fitted with local control.
Basic outfit:
The control unit is the main part of the system DMS2; it comprises:
– Microcomputer and memory of parameters
– Position sensors
– 2 signalling LED
– Connectors for connecting the torque sensor, relay board, and two-position inputs, source board, communication
adapter, LCD display, and local control
Torque unit provides for scanning torque by the contactless sensor
Source unit – two types exist:
DMS2.ZAN for the two-position or three-position control of the actuator by binary signals “Open” and “Close” or by
analog signal 0
(4)
– 20 mA.
DMS2.ZPR for controlling the actuator by the industrial bus Profibus.
Both units include the feeding source for electronics, two relays for controlling the power switches
(contactors or
contactless switches)
of the electric motor, guarding of sequence of phases
(in case the actuator is fed by three-phase
voltage),
circuits for connecting the anticondensation heater, and input terminals for connecting the thermo-contact
from the electric motor. The units are fitted with the power terminal board for connecting the power supply. The units
are fitted with a connector for the display and local control.
Unit DMS2ZAN also contains:
– input circuits for the two-position and three-position control of the actuator and terminals for connecting external
control signals
– input of signal SAFE – information on external failure
– relay – total of five; four (signalling) can be set for reporting of position, torque, or other operation states of the
actuator; the fifth (Ready) is used for reporting of errors, warnings, and other states when the actuator cannot
faultlessly perform its function, and the terminals to which contacts of the relay are connected
– circuits of the feedback current signal – information on position of the actuator output shaft
Unit DMS2.ZPR also contains:
– circuits for communication with the superior control system through the industrial bus Profibus DP, input and output
terminals for connecting the bus, and termination resistors with a switch.
Display
unit
– two-row display, 2 x 12 alpha-numeric characters
Unit of push-buttons
– sensors of push-buttons
“open”, “close”, “stop” and the rotary switch “local, remote, stop”.
The actuator can be fitted with contactors or contactless switching of the electric motor; it can be fitted with an
electronic brake.
PROCEDURE OF SETTING PARAMETERS BY PROGRAM DMS2
Before putting the actuator into operation, it is necessary to set some parameters of the system by means of
program DMS2 on PC.
Before adjustment, check the actuator according to the paragraph ASSEMBLing And putting the ACTUATOR into operation.
Warning:
For safety reasons (reduced risk of damage to the actuator by wrong wiring), the system is delivered in the state of
the induced error of CALIBRATION when the functions are limited and, during controlling the actuator from program
DMS2, its run is stopped if any torque is induced.
Note:
The setting program is the same for electronics DMS2 ED. See the figure on page 13 for the main window and the
window of Selection of electronics.