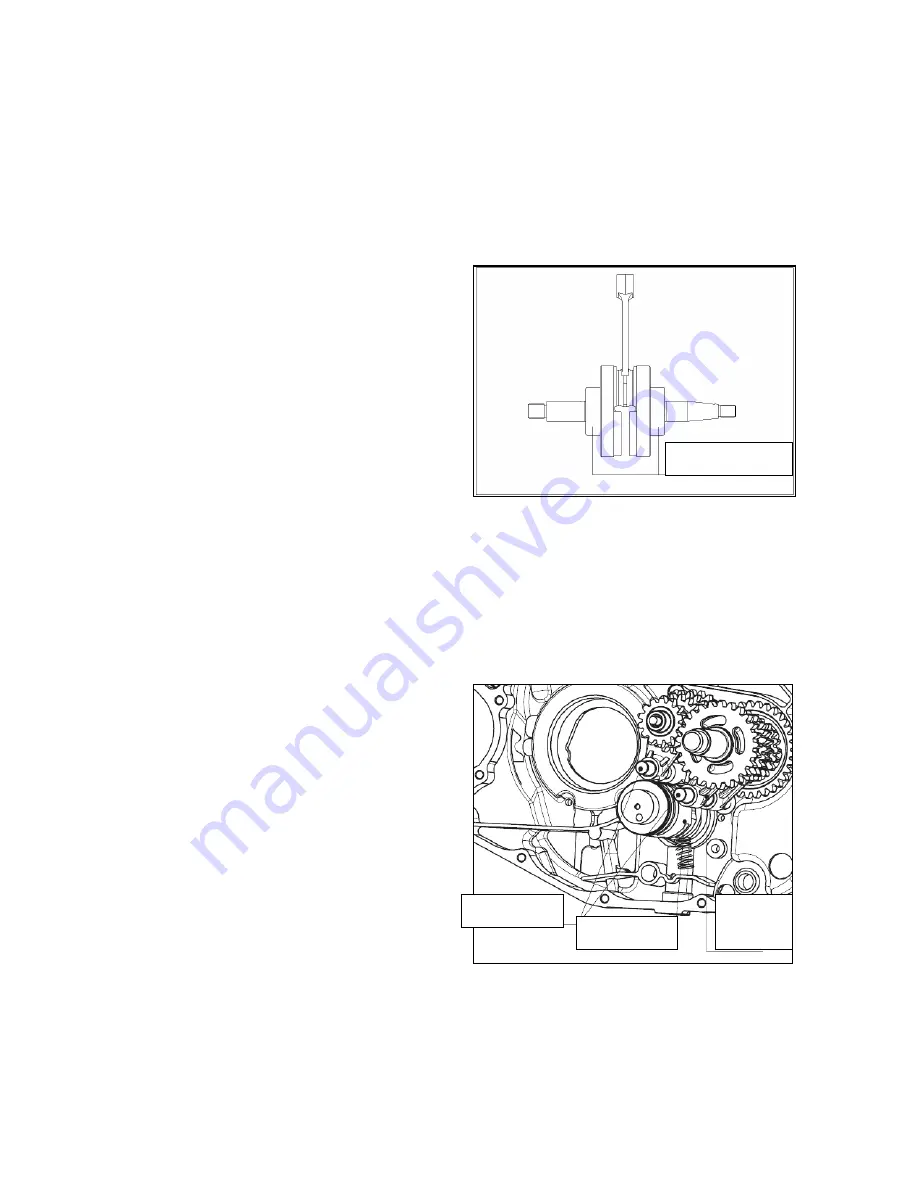
162
Check if the crank shaft is noisy or loose while restoring.
Replace it if so.
Note: both the crank connecting rod and the gearshift mechanism are installed on the crank case.
Draw out the shifting fork.
Remove the gearshift drum.
Remove the gearshift fork.
Crank shaft bearing
Gearshift drum
Gearshift
fork
Shifting fork
Summary of Contents for RKV 200
Page 1: ...1 RKV 200 Motorcycle Service Manual...
Page 18: ...18...
Page 44: ...44 Symptom Electric horn mutes Diagnosis procedures...
Page 143: ...143...
Page 144: ...144...
Page 158: ...158 Gearshift drum Shifting fork Shift rail Principal shaft assembly Vice shaft assembly...
Page 171: ...171 Complete QJ200 2A Schematic Circuit Diagram...