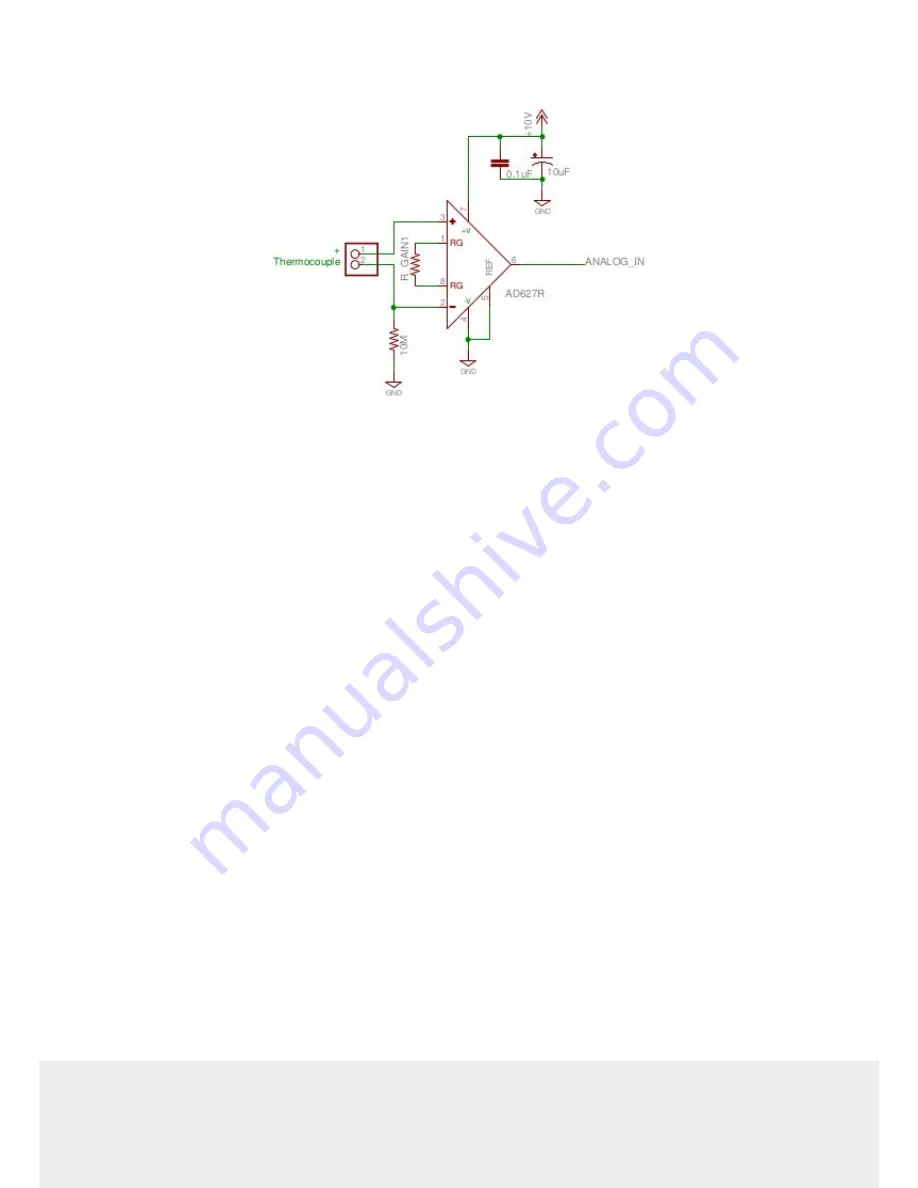
33
ZABER TECHNOLOGIES INC.
11. Troubleshooting X-Series Motion Devices
The following sections contain tips for troubleshooting common problems. If the device is unable
to communicate, and it is operating erratically, a manual factory reset can be performed through
the following steps. Note that this will reset most settings.
1. Power Off the device
2. Push and hold the knob for the first Axis (if applicable)
3. Power On the device
4. Continue to hold the knob in until the blue LED is lit (~5 seconds), then release.
The device has been returned to its factory defaults and can be configured as per the steps in
Initial Setup.