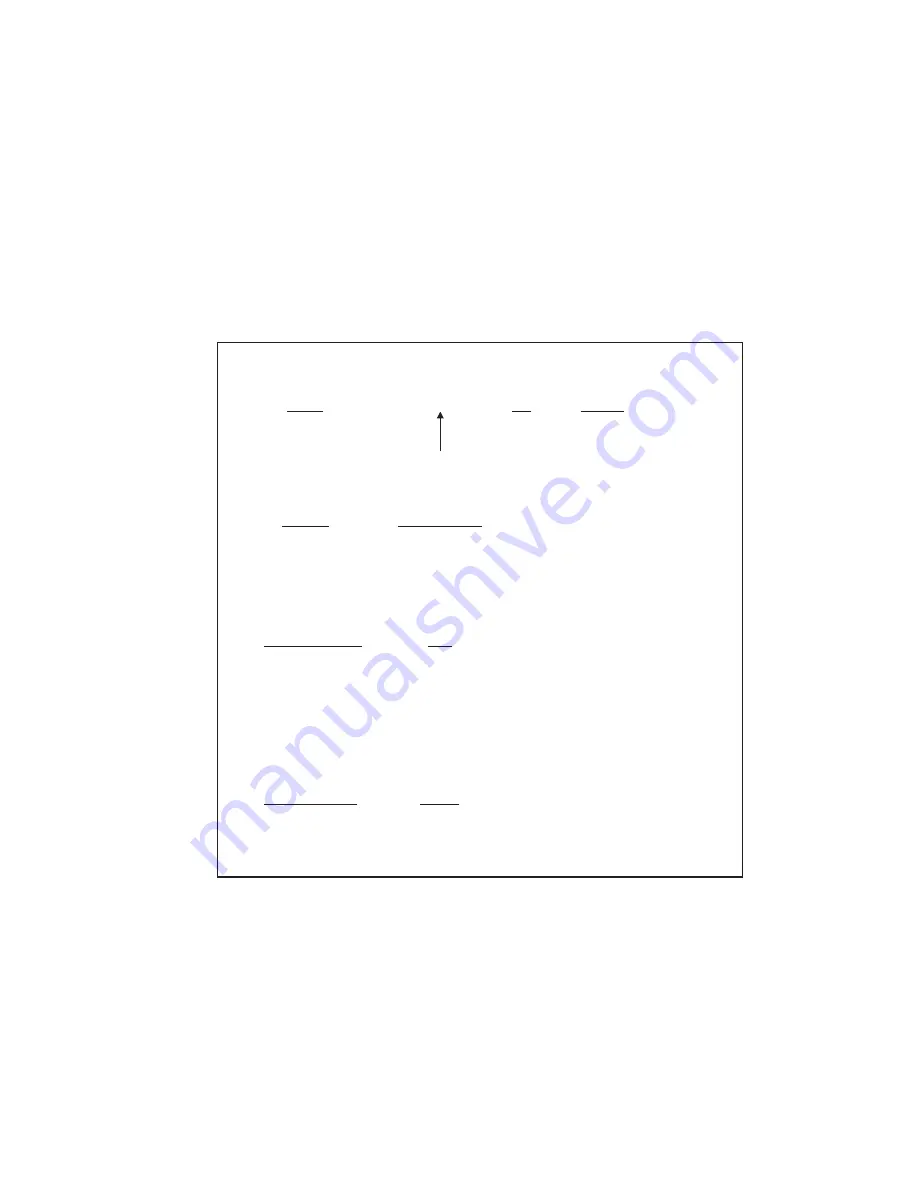
YZ Systems, Inc. • 3101 Pollok Drive • Conroe, Texas • USA • 77303 • P: 936.788.5593 • F: 936.788.5720
Page 45
NJEX 8300 ver.092001 ATEX Rev.
SSSSS
ECTION
ECTION
ECTION
ECTION
ECTION
7:
7:
7:
7:
7: C
C
C
C
C
ALIBRA
ALIBRA
ALIBRA
ALIBRA
ALIBRATING
TING
TING
TING
TING
S
S
S
S
S
IGN
IGN
IGN
IGN
IGNAL
AL
AL
AL
AL
I
I I
I
I
NPUTS
NPUTS
NPUTS
NPUTS
NPUTS
Calculation for Determining the Span Frequency
Pulse
x
max flow rate
CF=
Pulses
CF
Hr
Hr
As determined by the flow metering device
Example:
1 pulse
x
1,000,000CF
=
100,000 pulses/hr
10CF
Hr
Since pulses per hour is not an option for programming the N-300G divide by 60
minutes per hour to obtain pulses per minute.
100,000 pulses
x
1Hr
=
1,666.7 pulses/min.
Hr
60 min.
Since a maximum of 100 pulses per minute may be programmed into the N-
300G, you must now divide by 60 seconds per minute to obtain pulses per
second, if this value had calculated to less than 100 pulses per minute it could
have been programmed into the N-300G.
1,666.7 pulses
x
1 min.
=
27.7 pulses/sec.
min.
60 sec
Select PPS and set the span to 28 pulses per second.
Figure 113