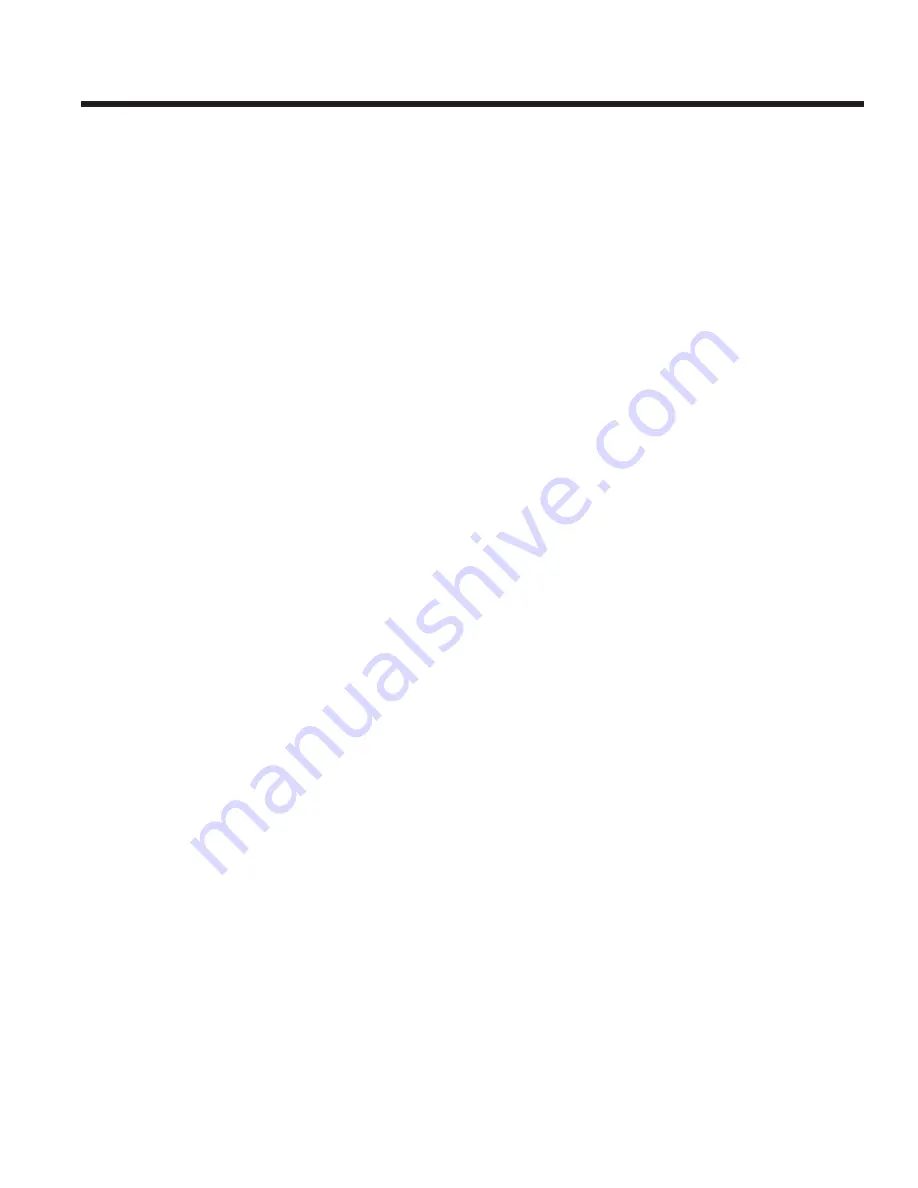
FORM 150.68-EG1 (0212)
3
JOHNSON CONTROLS
Product Description
YLPA air-to-liquid reversible heat pumps are completely
factory assembled with all interconnecting refrigerant
piping and wiring ready for fi eld installation. The unit is
pressure tested, evacuated, and fully factory charged
with refrigerant R410A and oil in each of the independent
refrigerant circuits. After assembly, an operational test is
performed with water fl owing through the heat exchanger
to ensure that each refrigerant circuit operates correctly.
The unit structure is manufactured from heavy-gauge,
galvanised steel coated with baked-on powder paint
(Champagne (RAL 7006, Munsell No. 9.8YR4.36/1.2)).
YLPA heat pumps are designed in accordance with NFPA
70 (National Electric Code), ASHRAE/ANSI 15 Safety
code for mechanical refrigeration, ASME and rated in
accordance with ARI Standard 550/590.
COMPRESSORS
The unit has suction-cooled, hermetic scroll compressors.
High effi ciency is achieved through a controlled orbit and
the use of advanced scroll geometry. The compressors
incorporate a compliant scroll design in both the axial
and radial directions. All rotating parts are statically and
dynamically balanced. The compressor motors have
integral protection against overloads that will automatically
reset. Starting is direct on line, and soft start is available
as an option.
The compressors are switched On and Off by the
unit microprocessor to provide capacity control. Each
compressor is fi tted with a crankcase strap heater. All
compressors are mounted on isolator pads to reduce
transmission of vibration to the rest of the unit.
The motor terminal boxes have IP54 weather protection.
REFRIGERANT CIRCUITS
Two independent refrigerant circuits are provided on each
unit. Each circuit uses copper refrigerant pipe formed
on computer controlled bending machines to reduce the
number of brazed joints resulting in a high integrity and
reliable system.
Each circuit shall incorporate all components necessary for
the designed operation including: a suction accumulator;
a liquid receiver; a four way reversing valve which
changes the direction of the refrigerant fl ow and the
function of the heat exchanger when switching between
cooling and heating modes; service valves; isolation (ball/
angle) valves; pressure relief valves; a high absorption
removable core fi lter-drier; a sight glass with moisture
indicator; a cooling mode thermal expansion valve and a
heat pump mode thermal expansion valve. Suction lines
shall be covered with closed-cell insulation.
REFRIGERANT TO WATER HEAT EXCHANGER
The 2-pass dual circuit shell and tube type direct expansion
(DX) heat exchanger has refrigerant in the tubes and liquid
fl owing through the baffl ed shell. The waterside (shell)
design working pressure is 10 barg. The refrigerant side
(tubes) design working pressure is 45 barg. The refrigerant
side is protected by pressure relief valve(s).
The heat exchanger is equipped with a heater for frost
protection to -4°F (below this the ball valve in the discharge
line must be closed) and insulated with fl exible closed-
cell foam. Water connection to the heat exchanger is via
victaulic grooved connections. Victaulic groove to fl ange
converters are available as an option
AMBIENT COILS
The ambient coils are seamless copper tubes, arranged
in staggered rows, mechanically expanded into coated
aluminium fi ns. Integral sub-cooling is included.
The condenser fans have composite metal/plastic `sickle`
blades integrated into the rotor of an external rotor motor.
They are designed for maximum effi ciency and statically
and dynamically balanced for vibration free operation.
They are directly driven by independent motors, and
positioned for vertical air discharge. The fan guards
are constructed from heavy-gauge, corrosion resistant,
coated steel.
The IP54 fan motors are the totally enclosed air-over type
with permanently lubricated double-sealed ball bearings.
POWER AND CONTROL PANELS
All power and controls are contained in an IP 55 cabinet
with hinged and gasket sealed outer doors. The power
panel includes:
• Factory mounted non-fused disconnect switch
with external red/yellow, lockable handle to enable
connection of the unit power supply. The disconnect
switch can be used to isolate the power for servicing
and as a emergency stop.
• Factory mounted compressor contactors and
compressor fuses provide short circuit protection.
Overload protection for each compressor is provided
by inherent motor winding temperature sensing and
a trip module.
• Factory mounted fan contactors and fuses provide
short circuit protection. Overload protection for
each fan is provided by a inherent motor winding
temperature device.
• Factory mounted control transformer to convert the unit
supply voltage to 115 V - 1 Ø - 60 Hz for the control
system.
• Control supply fuses and connections for a remote
emergency stop device.