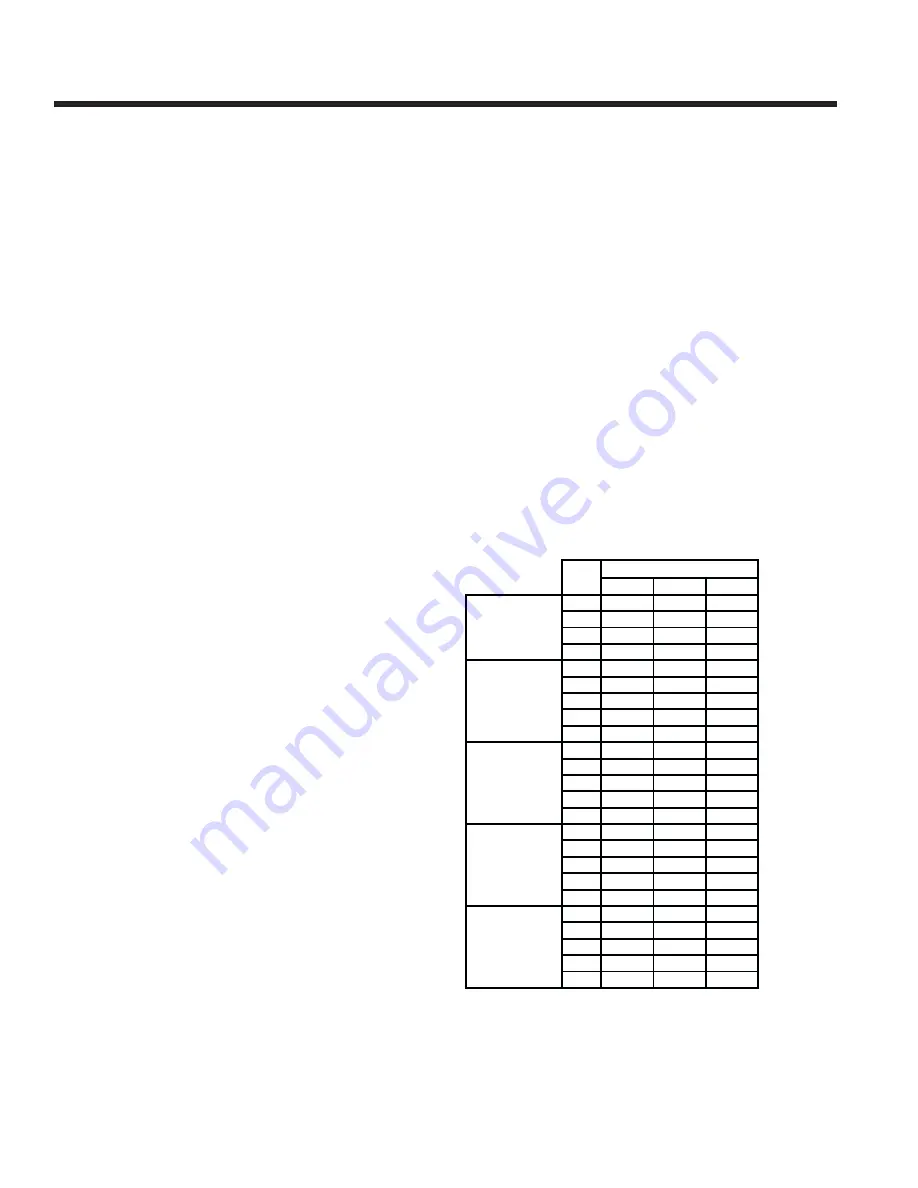
JOHNSON CONTROLS
8
FORM 150.68-EG1 (0212)
Application Data
LOCATION REQUIREMENTS
To achieve optimum performance and trouble-free service,
it is essential that the proposed installation site meet with
the location and space requirements for the model being
installed.
The clearances recommended are nominal for the
safe and effi cient operation and maintenance of the
unit and power and control panels. Local Health and
safety regulations, or practical considerations for service
replacement of large components, may require larger
clearances than those given in this manual.
OUTDOOR INSTALLATIONS
The units can be installed at ground level on a suitable at
level foundation easily capable of supporting the weight of
the unit, or on a suitable rooftop location. In both cases an
adequate supply of air is required. Avoid locations where
the sound output and air discharge from the unit may be
objectionable.
The location should be selected for minimum sun
exposure and away from boiler fl ues and other sources of
airborne chemicals that could attack the condenser coils
and steel parts of the unit.
If located in an area accessible to unauthorized persons,
steps must be taken to prevent access to the unit by
means of a protective fence. This will help to prevent the
possibility of vandalism, accidental damage, or possible
harm caused by unauthorized removal of protective
guards or opening panels to expose rotating or electrically
live components.
For ground level locations, the unit must be installed
on a suitable fl at and level concrete base that extends
to fully support the two side channels of the unit base
frame. A one-piece concrete slab, with footings extending
below the frost line is recommended. To avoid noise and
vibration transmission, the unit should not be secured to
the building foundation.
On rooftop locations, choose a place with adequate
structural strength to safely support the entire operating
weight of the unit and service personnel. The unit can
be mounted on a concrete slab, similar to ground fl oor
locations, or on steel channels of suitable strength. The
channels should be spaced with the same centres as
the unit side and front base rails. This will allow vibration
isolators to be fi tted if required. Isolators are recommended
for rooftop locations.
LOCATION CLEARANCES
Adequate clearances around the unit(s) are required
for the unrestricted air-fl ow for the ambient coils and to
prevent re-circulation of discharge air back onto the coils.
If clearances given are not maintained, air-fl ow restriction
or re-circulation will cause a loss of unit performance, an
increase in power consumption, and may cause the unit
to malfunction. Consideration should also be given to the
possibility of down drafts, caused by adjacent buildings,
which may cause re-circulation or uneven unit air-fl ow.
For locations where signifi cant cross winds are expected,
such as exposed roof tops, an enclosure of solid or
louvre type is recommended to prevent wind turbulence
interfering with the unit air-fl ow.
When units are installed in an enclosure, the enclosure
height should not exceed the height of the unit on more
than one side. Where accumulation of snow is likely,
additional height must be provided under the unit to ensure
normal air-fl ow to the unit.
Refer to the table below and the diagrams on the following
page for location clearances.
0115SE 0145SE 0170SE
A
47
47
47
B
32
32
32
C
32
39
47
D
55
55
55
A
47
47
47
B
32
32
32
C
32
39
47
D
106
126
126
E
55
55
55
A
47
47
47
B
32
32
32
C
32
39
47
D
91
118
126
E
55
55
55
A
47
47
47
B
47
47
47
C
32
32
32
D
32
39
47
E
67
75
83
A
47
47
47
B
47
47
47
C
32
32
32
D
32
32
32
E
55
55
55
YLPA
Arrangement
A5
Louvres on
2 walls
Dim.
(in)
Arrangement
A1
Solid Walls
Arrangement
A2
Solid Walls
Arrangement
A3
Louvres on
2 walls
Arrangement
A4
Solid Walls