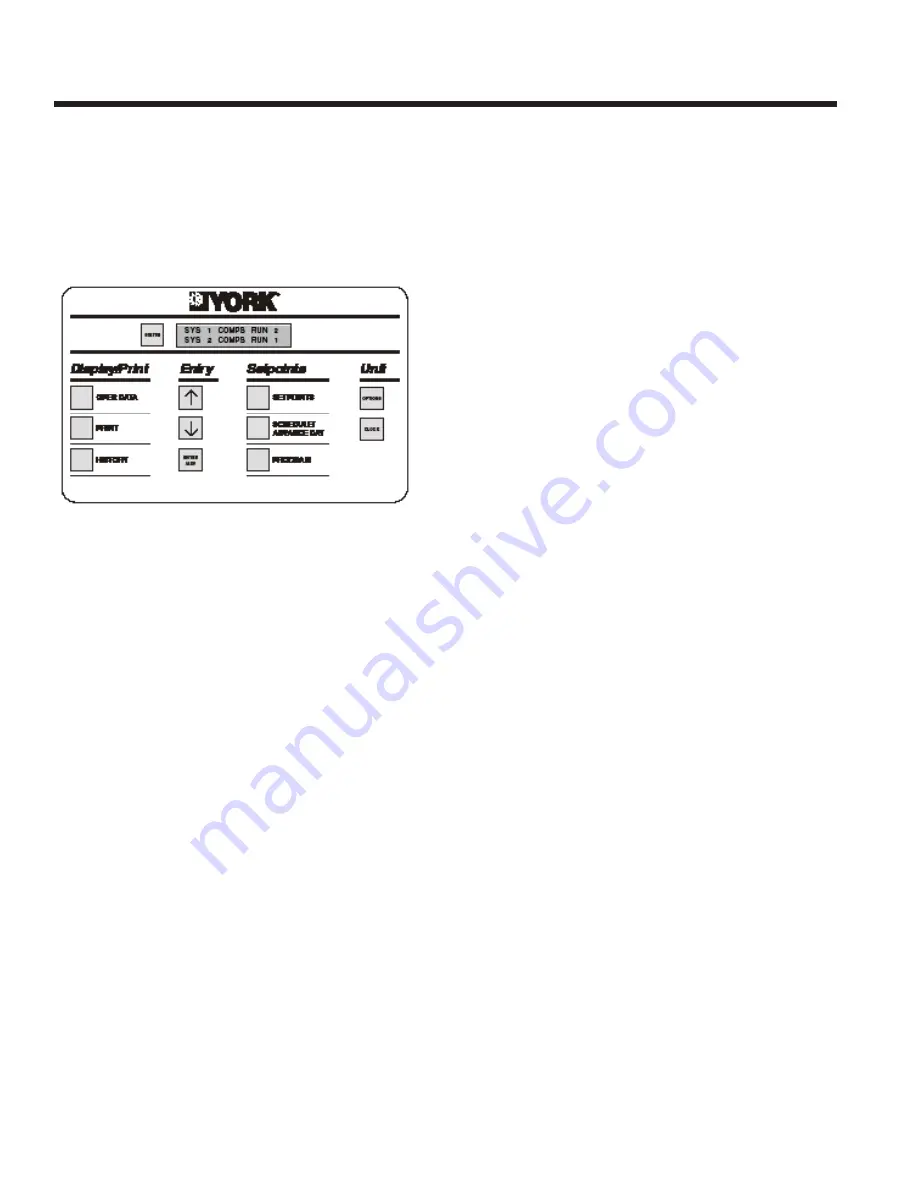
JOHNSON CONTROLS
4
FORM 150.68-EG1 (0212)
Microcomputer Control Center
The control panel includes:
• A Liquid Crystal Display (two display lines of twenty
characters per line) with Light Emitting Diode
backlighting for easy viewing
• A Colour coded 12-button keypad
• Customer terminal blocks for control inputs and liquid
fl ow switch.
The microprocessor control includes:
• Automatic control of compressor start/stop,
anticoincidence and anti-recycle timers, pump and
unit alarm contacts. Automatic reset to normal unit
operation after power failure.
• Remote water temperature setpoint reset via analog
input or a pulse width modulated (PWM) input signal
or up to two steps of demand (load) limiting.
• Software is loaded into the microprocessor controller
via a SD card, with programmed setpoints retained in
a lithium battery backed real time clock (RTC) memory.
• Forty character liquid crystal display, with description
available in fi ve languages (English, French, German,
Spanish or Italian)
Programmable setpoints:
• Chilled liquid temperature setpoint and range
• Hot liquid temperature setpoint and range
• Remote reset temperature range
• Set daily schedule/holiday for start/stop
• Manual override for servicing
• Low ambient cutout
• High ambient cutout (heating only - fi xed)
• Low liquid temperature cutout
• Low suction pressure cutout
• High discharge pressure cutout
• Anti-recycle timer (compressor start cycle time)
• Anti-coincident timer (delay compressor starts)
Displayed Data:
• Leaving liquid temperature
• Air coil defrost temperatures
• Low leaving liquid temperature cutout setting
• Low ambient temperature cutout setting
• Ambient air temperature
• Metric or Imperial data
• Discharge and suction pressure cutout settings
• System discharge and suction pressures
• Anti-recycle timer status for each system
• Anti-coincident system start timer condition
• Compressor run status
• No load condition
• Day, date and time
• Daily start/stop times
• Holiday status
• Automatic or manual system lead/lag control
• Lead system defi nition
• Compressor starts & operating hours (each
compressor)
• Status of evaporator heater and fan operation
• Run permissive status
• Number of compressors running
• Mode solenoid valve status
• Load & unload timer status
• Liquid pump status
System Safeties:
• Cause individual compressors to perform auto shut
down and require manual reset in the event of 3 trips
in a 90-minute time period
• High discharge pressure
• Low suction pressure
• High-pressure switches
• Motor protector
Unit Safeties:
They are automatic reset and cause compressor to shut
down
• Low leaving chilled liquid temperature
• Under voltage
• Loss of liquid fl ow (through fl ow switch)
For each system a common alarm contact for:
• Low leaving chilled liquid temperature
• Low voltage
• Low battery
• High discharge pressure (per system)
• Low suction pressure (per system)
• Compressor motor protection