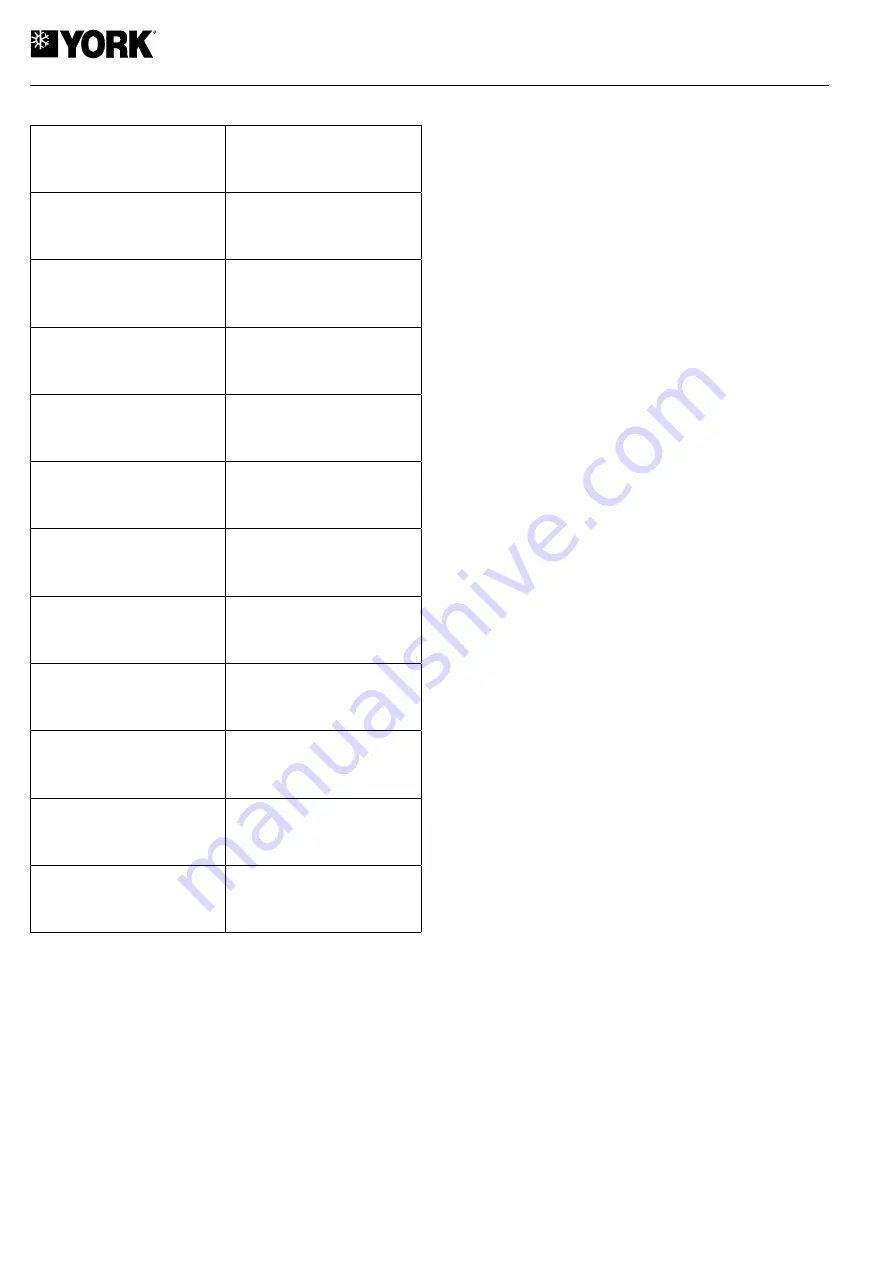
6
Compressors
Four hermetic Scroll compressors mounted on two tandems
on rails and antivibratory supports. Both tandems are con-
nected to two independent cooling circuits. Start-up is carried
out by four sequential FIFO starters. These compressors are
equipped with protection against high operating tempera-
tures. The sump heaters operate only when the compressor
is inoperative.
Indoor heat exchanger
Comprises a stainless steel plate exchanger with two refriger-
ant circuits and a common water circuit. Adequately insulated
by a layer of closed-cell elastomer foam. Includes an anti-
freeze heater monitored by the controller and a differential
pressure switch acting as a flow control switch. The refrigerant
side of said exchanger accepts an operating pressure of 52
bar, whereas the water side accepts 10 bar. When the unit
includes a hydro kit, maximum admissible pressure on the
water side is 6 bar (adjustment of the tank relief valve).
Outdoor heat exchangers
Made up of four notched aluminium fin coils and grooved cop-
per tubing mechanically expanded within the fin assembly.
Fans
Of the axial and low sound level type. Equipped with single-
phase motors with IP54 protection. These motors allow speed
control by means of a phase cut-out shifters controlled by
the unit controller. This allows unit operation at low ambient
temperatures (-18°C).
On heat pump units, the fan will remain inoperative during
defrosts.
Electric and control panel
Located at the front of the unit, and with IP44 protection. The
operating and control components are factory mounted, wired
and tested. The access door of this control panel is equipped
with a locking isolator that turns power supply off. Inside
we find the contactors for compressors and the pump, the
transformer, magneto-thermal protectors, the controller, two
speed controls, connecting strip and the keyboard-display
with the unit controls.
Control keyboard-display
This device is accessible through an external leak-tight plastic
cover. This is an easy-to-use remote control unit for a distance
of up to 500 m., and is accessed by means of a password.
For further information, please see Operating Instructions.
Cooling circuit
Made up of two circuits in parallel. Each circuit includes:
expansion valve, filter-dryer, liquid sight glass, high and low
pressure switches, service valves for isolating the condensing
unit, and Schrader valves on the high and low sides. The heat
pump model also includes, in addition, a four-way valve (en-
ergized in summer cycle and during defrosts), check valves,
heating circuit expansion valve and a liquid tank. The suction
tubing is coated with closed-cell elastomer insulation.
Unit with hydro kit (pack)
These units include a pack assembled with the components of
a hydro kit. This assembly is located within the unit frame and
does not increase the footprint of same. It includes the follow-
Features and advantages
Technical Specifications
These units are supplied completely factory-assembled and
with all refrigerant tubing and wiring ready for installation
on the job site. After mounting, these units must undergo
an operational test. Refrigerant leaks will also be checked
during this process.
Galvanized steel casing
The units are made of galvanized steel sheeting and anti-
corrosion nuts and bolts. Panels with ¼-turn locks can be
removed to access internal components.
The casing parts are painted with white RAL9002 oven-baked
polymerized enamel.
Features
Advantages
R-410A refrigerant
Does not harm the ozone layer.
Small footprint
Minimum space for installation.
Low height and weight
Space for installing on terraces.
Factory tested equipment
Operating quality control.
Accessibility
Easy maintenance.
Main switch
Operator safety.
Microprocessor for control and
alarms
Easy and safe operation.
Manufactured to ISO 9001
High quality level.
Variable speed fan
Low noise level and condensation
control.
Hydro kit
For installations with low water
volume.
Communications connection
Ideal for building management.
Summary of Contents for YCSA 120 T
Page 2: ......
Page 4: ......
Page 23: ...23 Minimum technical clearance ...
Page 24: ...24 Wiring diagram YCSA YCSA H 120 µC3 400 3 50 ...
Page 26: ...26 Wiring diagram YCSA YCSA H 120 µC3 400 3 50 ...
Page 27: ...27 Wiring diagram YCSA YCSA H 150 µC3 400 3 50 ...
Page 29: ...29 Wiring diagram YCSA YCSA H 150 µC3 400 3 50 ...
Page 30: ...30 Wiring YCSA YCSA H 120 and 150 T TP ...
Page 35: ...35 General wiring diagram ...
Page 48: ...www johnsoncontrols com ...