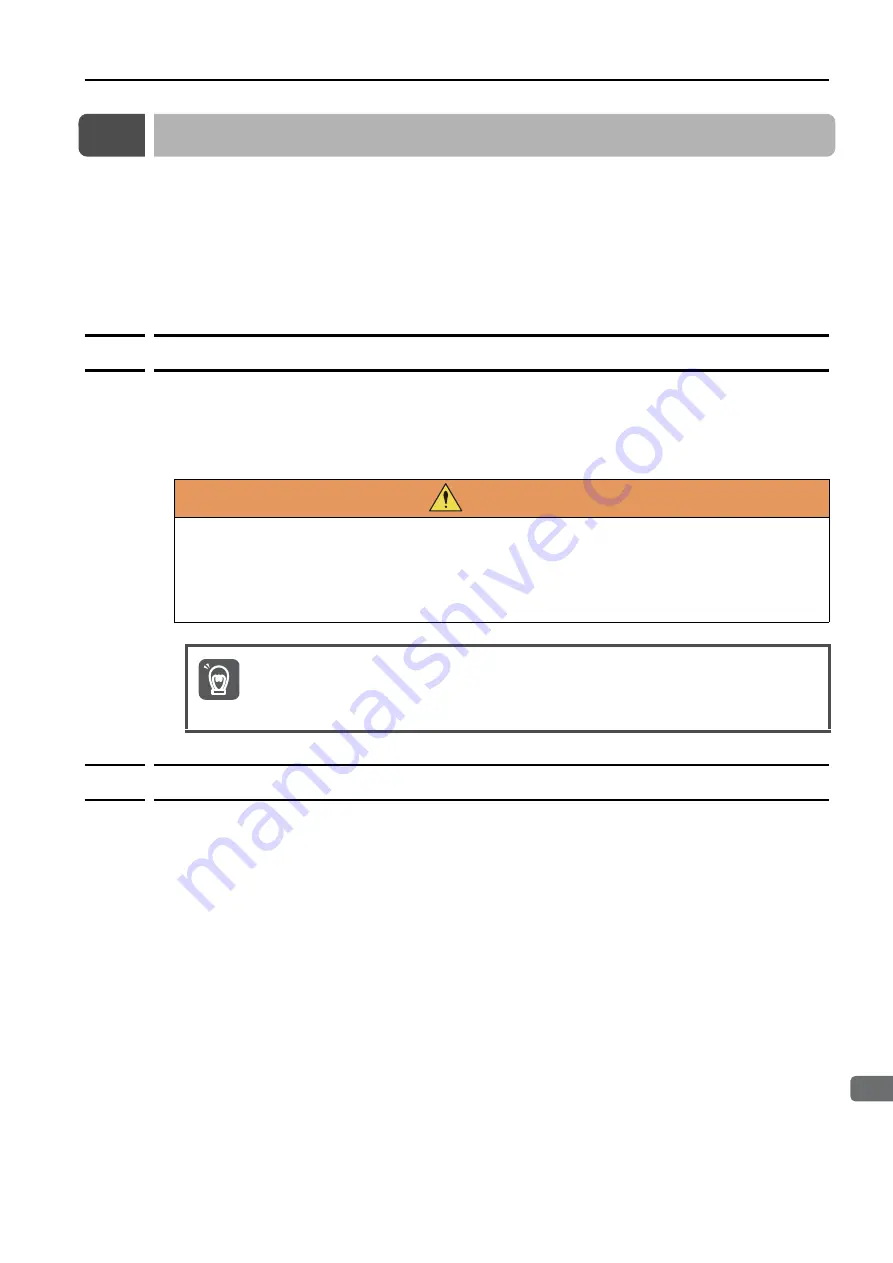
2.2 Speed Ripple Compensation
2.2.1 Outline
2-7
2
T
uning
2.2
Speed Ripple Compensation
This section describes speed ripple compensation.
This functionality is supported by the following SERVOPACKs.
•
Σ
-7S SERVOPACKs with Analog Voltage/Pulse Train References
•
Σ
-7S SERVOPACKs with MECHATROLINK-II Communications References
•
Σ
-7S SERVOPACKs with MECHATROLINK-III Communications References
•
Σ
-7W SERVOPACKs with MECHATROLINK-III Communications References
2.2.1
Outline
Speed ripple compensation reduces the amount of ripple in the motor speed due to torque rip-
ple or cogging torque. You can enable speed ripple compensation to achieve smoother opera-
tion.
To enable speed ripple compensation, you must set up ripple compensation on the Sig-
maWin+.
2.2.2
Setting Up Speed Ripple Compensation
Restrictions
Systems for Which Execution Cannot Be Performed
There are no restrictions.
Systems for Which Adjustments Cannot Be Made Accurately
Systems for which there is not a suitable range of motion
Preparations
Check the following settings before you execute speed ripple compensation.
•
The main circuit power supply must be ON.
•
The servo must be OFF.
•
There must be no alarms or warnings.
•
There must be no hard wire base block (HWBB).
•
The parameters must not be write prohibited.
WARNING
Speed ripple compensation requires operating the motor and therefore presents hazards.
Observe the following precaution.
Confirm safety around moving parts.
This function involves automatic operation. Make sure that you can perform an emergency
stop (to turn OFF the power supply) at any time.
Execute speed ripple compensation only after adjusting the gains.
•
Reset speed ripple compensation after you replace the Servomotor or SERVOPACK.
•
Execute speed ripple compensation after jogging to a position that ensures a suitable
range of motion.
Important
Summary of Contents for SERVOPACK Sigma 7S Series
Page 1: ......