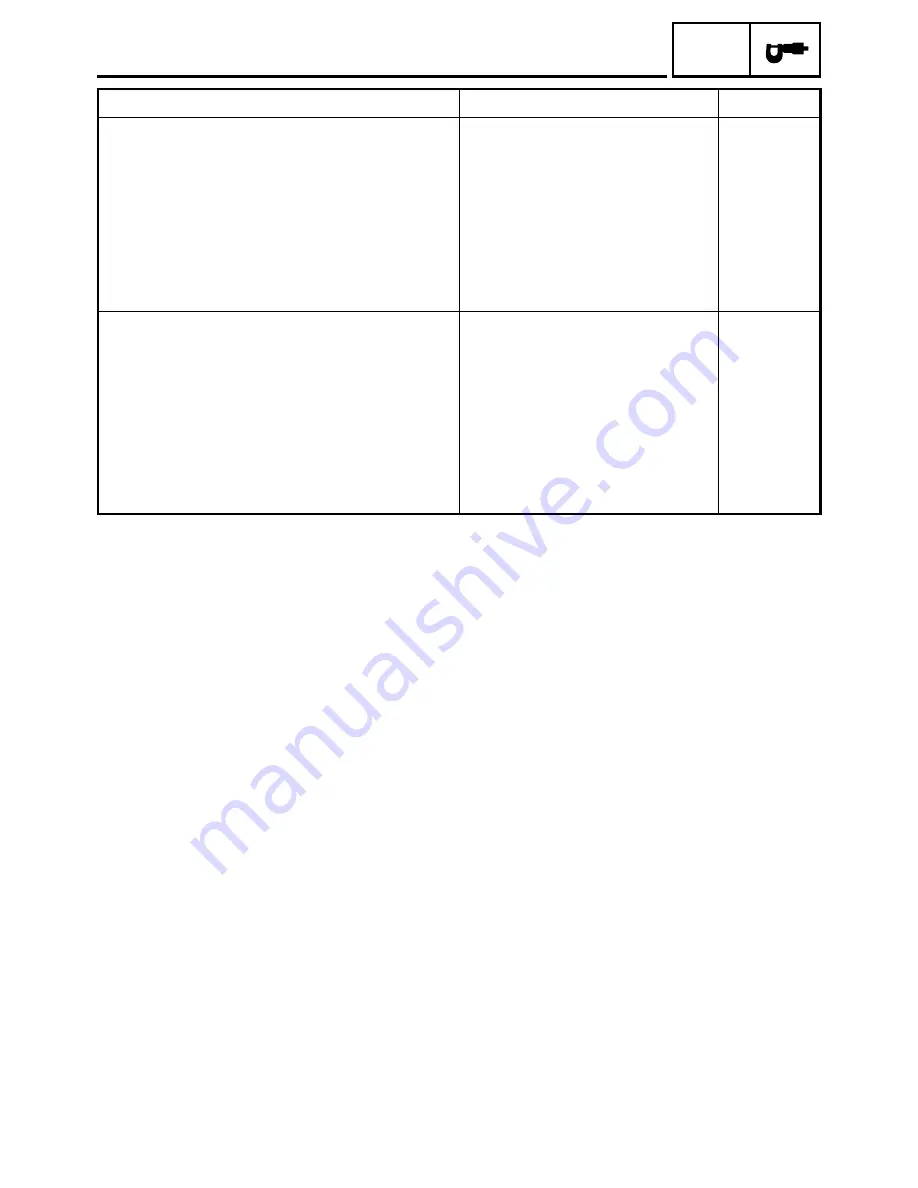
SPEC
2 - 9
MAINTENANCE SPECIFICATIONS
Lubrication system:
Oil filter type
Paper type
----
Oil pump type
Trochoid type
----
Tip clearance
0.12 mm or less
(0.0047 in or less)
0.20 mm
(0.008 in)
Side clearance
0.09 ~ 0.17 mm
(0.0035 ~ 0.0067 in)
0.24 mm
(0.009 in)
Housing and rotor clearance
0.03 ~ 0.10 mm
(0.0012 ~ 0.0039 in)
0.17 mm
(0.0067 in)
Cooling:
Radiator core size
Width
117.8 mm (4.6 in)
----
Height
220 mm (8.7 in)
----
Thickness
32 mm (1.26 in)
----
Radiator cap opening pressure
110 kPa (1.1 kg/cm
2
, 15.6 psi)
----
Radiator capacity (total)
0.6 L (0.53 Imp qt, 0.63 US qt)
----
Water pump
Type
Single-suction centrifugal pump
----
Item
Standard
Limit
www.PlanDeGraissage.org