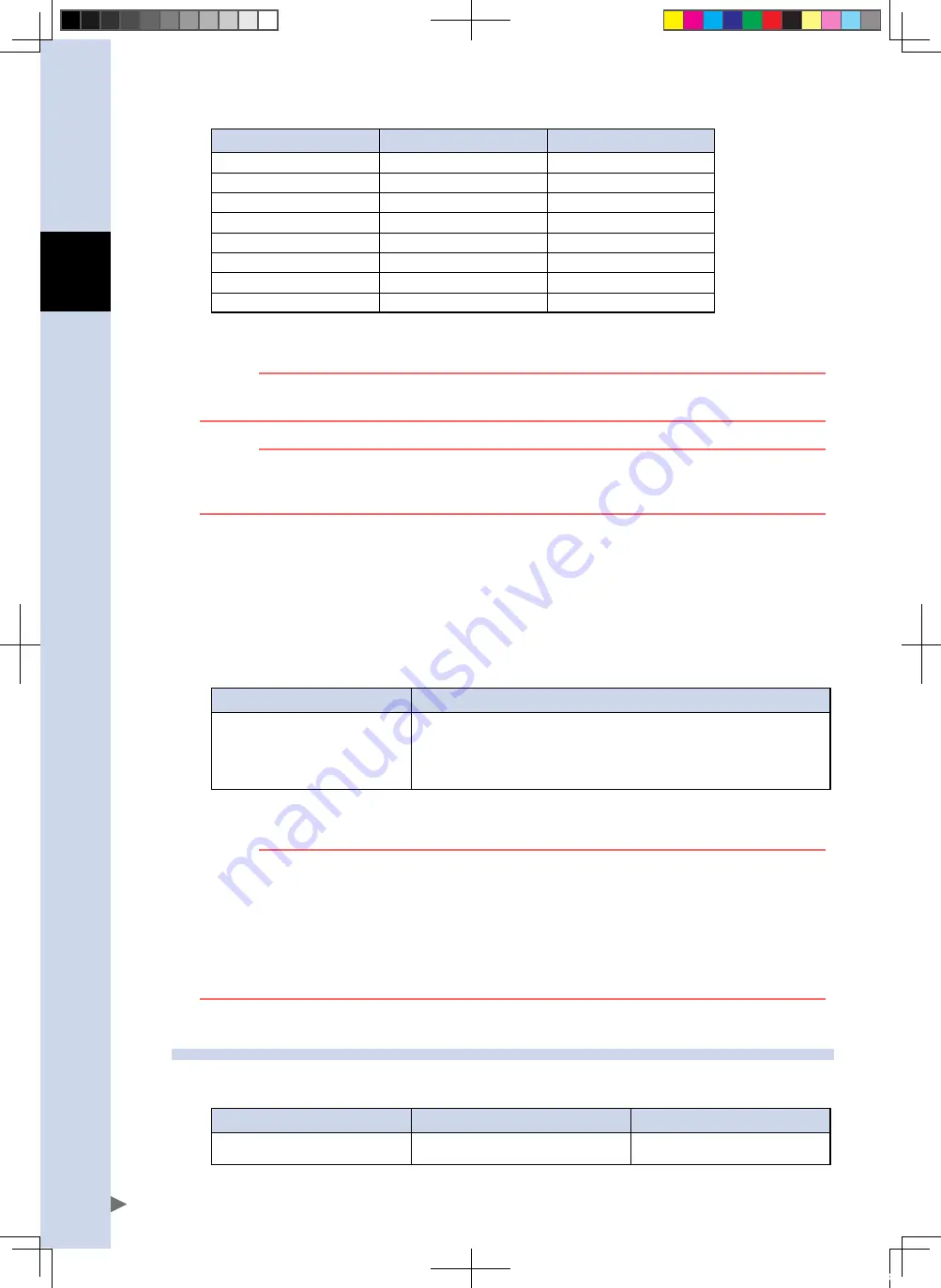
2
Periodic inspection
2-6
*1:
Bolt tightening torque
Bolt size
Tightening torque (kgfcm)
Tightening torque (Nm)
M3 button head bolt
14
1.4
M3
20
2.0
M4
46
4.5
M5
92
9.0
M6
156
15.3
M8
380
37
M10
720
71
M12
1310
128
■
Inspection to be performed with the controller turned on
w
WARNING
THE ROBOT CONTROLLER MUST BE INSTALLED OUTSIDE THE SAFETY ENCLOSURE, TO PREvENT A HAzARDOUS SITUATION
IN WHICH YOU OR ANYONE ENTER THE SAFETY ENCLOSURE TO INSPECT THE CONTROLLER WHILE IT IS TURNED ON.
w
WARNING
• BODILY INjURY MAY OCCUR FROM COMING INTO CONTACT WITH THE FAN WHILE IT IS ROTATING.
• WHEN REMOvING THE FAN COvER FOR INSPECTION, FIRST TURN OFF THE CONTROLLER AND MAKE SURE THE FAN
HAS STOPPED.
1
Turn on the controller.
Check that no one is inside the safety enclosure, and then turn on the controller.
2
Place a sign indicating the robot is being adjusted.
Place a sign indicating the robot is being inspected, to keep others from operating the controller,
programming box or operation panel.
3
Perform the inspection.
Check the following points from outside the safety enclosure.
Checkpoint
Procedure
Cooling fan at rear of controller
• Check if the fan rotates normally.
• Check if objects blocking the fan are located and remove if any are found.
• Check for abnormal noise from the rotating fan. If abnormal noise is heard, visually
check and remove the cause. If no cause is found, contact your distributor .
• Check for dust on the fan cover. Remove and clean if necessary.
■
Adjustment and parts replacement
w
WARNING
• AFTER INSPECTION, IF YOU NOTICE ANY ADjUSTMENT OR PARTS REPLACEMENT IS NEEDED, FIRST TURN OFF THE
CONTROLLER AND THEN ENTER THE SAFETY ENCLOSURE TO PERFORM THE NECESSARY WORK.
• AFTER THE ADjUSTMENT OR REPLACEMENT WORK HAS BEEN COMPLETED, INSPECT THE CHECKPOINTS STATED IN
"DAILY INSPECTION" IN THIS SECTION.
• IF THE REPAIR OR PART REPLACEMENT OF THE ROBOT OR CONTROLLER IS REQUIRED, CONTACT YOUR DISTRIBUTOR.
SUCH WORK NEEDS THE SPECIAL KNOWLEDGE AND SKILL. SO, THE REPAIR OR PART REPLACEMENT WORK OF THE
ROBOT OR CONTROLLER MUST BE PERFORMED ONLY BY PERSONS WHO HAvE THE REQUIRED QUALIFICATIONS
DESCRIBED IN “2. QUALIFICATION OF OPERATORS/WORKERS” IN SECTION 4.1 OF “SAFETY INSTRUCTIONS”.
2.4 Three-year inspection
Inspect the following points once every three years, and contact us if any problem is found.
Set an earlier inspection interval if parts are subject to long-term or frequent usage.
Checkpoint
Procedure
Remarks
Ball screw nut sections and linear guides
Check for wear and looseness in the ball
screw, nut and linear guide.
If any abnormality is found, contact
your distributor.
FLIP-X_maint_E_V1.50.indb 6
18/05/15 15:01
Summary of Contents for FLIP-X Series
Page 2: ...FLIP X_maint_E_V1 50 indb 2 18 05 15 15 00...
Page 40: ...FLIP X_maint_E_V1 50 indb 2 18 05 15 15 01...
Page 41: ...Chapter 1 Overview Contents 1 Overview 1 1 FLIP X_maint_E_V1 50 indb 1 18 05 15 15 01...
Page 42: ...FLIP X_maint_E_V1 50 indb 2 18 05 15 15 01...
Page 44: ...FLIP X_maint_E_V1 50 indb 2 18 05 15 15 01...
Page 46: ...FLIP X_maint_E_V1 50 indb 2 18 05 15 15 01...
Page 60: ...FLIP X_maint_E_V1 50 indb 2 18 05 15 15 01...
Page 72: ...FLIP X_maint_E_V1 50 indb 12 18 05 15 15 01...
Page 74: ...FLIP X_maint_E_V1 50 indb 2 18 05 15 15 01...
Page 104: ...FLIP X_maint_E_V1 50 indb 2 18 05 15 15 01...