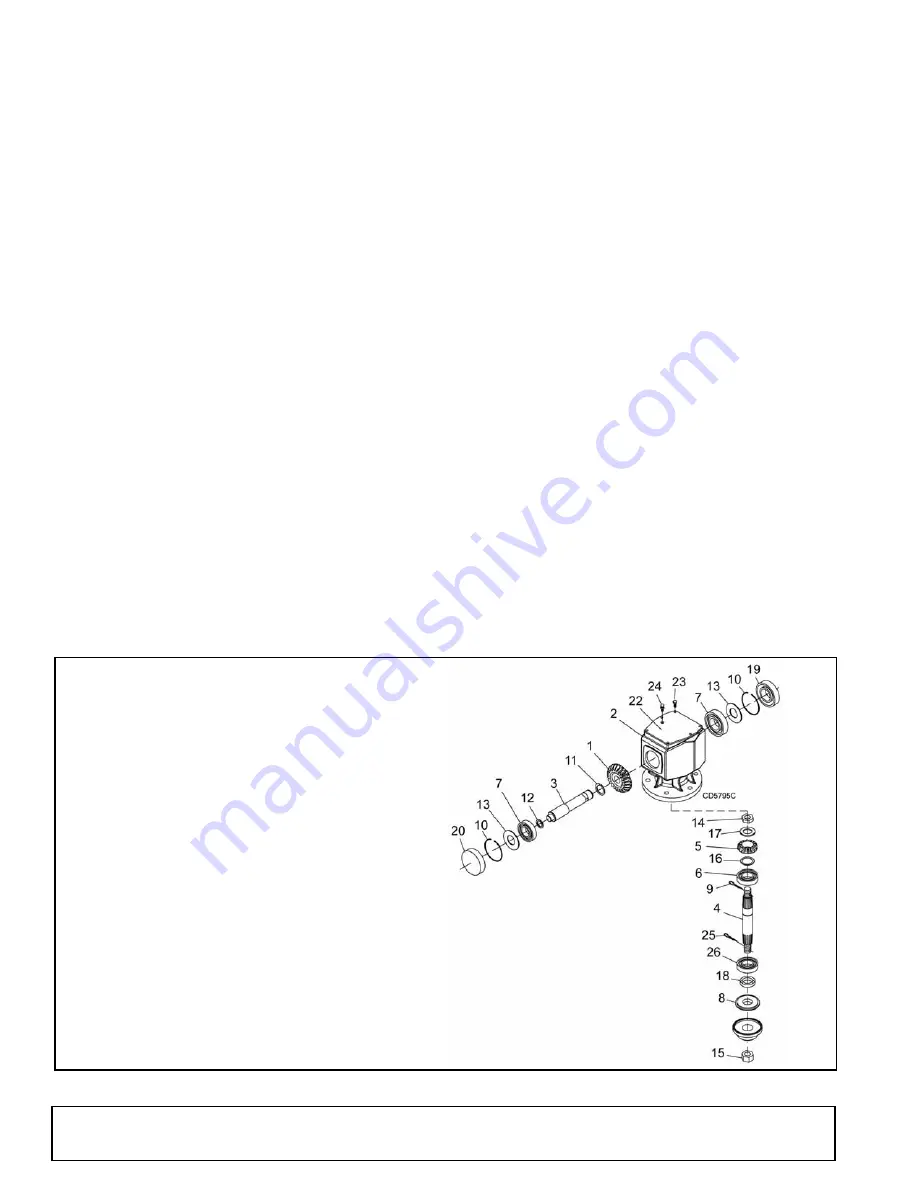
22
Dealer Service
MAN1279 (15/04/2019)
9.
Support housing in vise in a horizontal position.
10.
The castle nut (15), cotter pin (25), and hub are already removed with the
stump jumper/crossbar. Remove the protective seal (8), and oil seal (18).
11.
Remove cotter pin (9), castle nut (14), and shim (17) from output shaft
(4).
12.
Remove output shaft (4) by using a punch and hammer and tap on top to
drive down. Remove gear (5) and shim (16) from inside housing.
13.
Remove bottom bearing (26) by using a punch and hammer from the top,
outside the housing.
14.
Support housing upside down (top cover surface) and remove bearing (6)
by using a punch and hammer from the bottom side of the housing.
15.
Inspect gears for broken teeth and wear. Some wear is normal and will
show on loaded side. Forged gear surfaces are rough when new. Check
that wear pattern is smooth.
16.
Inspect vertical and horizontal shafts for grooves, nicks, or bumps in the
areas where the seals seat. Resurface any damage with emery cloth.
17.
Inspect housing and caps for cracks or other damage.
Assembly (Figure 13)
1.
Clean housing, paying specific attention to areas where gaskets will be
installed.
2.
Wash housing and all components thoroughly. Select a clean area for
gearbox assembly. Replace all seals, bearings, and gaskets. All parts
must be clean and lightly oiled before reassembling.
3.
Insert both output bearings (6) in the housing, using a round tube of the
correct diameter and a hand press.
4.
Slide output shaft (4) through both bearings (26 & 6) until it rests against
bearing (6).
5.
Slide shim (16) over output shaft (4).
6.
Press gear (5) onto output shaft (4) and secure with shim (17), castle nut
(14), and cotter pin (9).
7.
Apply grease to lower seal lips (18) and press seal (18) over output shaft
(4), using a tube of the correct diameter. Be sure not to damage the seal
lip.
8.
Press in housing so that seal is recessed. Press protective seal (8) until
seated flush with housing. Verify that the seal (8) is seated correctly.
9.
Press bearing (7) into the housing, using a round tube of the correct
diameter and a hand press. Secure with shim (13) and snap ring (10).
10.
Secure snap ring (11) on input shaft (3) if not already secure.
11.
Place gear (1) through top of housing and align gear (1) and gear (5) so
that gear teeth are a match.
12.
While holding gear (1) in place, slide input shaft (3) through gear (1) and
bearing (7). Align splines on shaft (3) and gear (1).
13.
Slide shim (12) over input shaft (3) and press bearing (7) onto input shaft
(3), using a round tube of the correct diameter and a hand press.
14.
Slide shim (13) over input shaft (3) and secure with snap ring (10).
15.
Check input shaft end float by moving the input shaft (3) by hand. If end
float is higher than 0.012", insert shim between input shaft (3) and rear
bearing (7). Repeat until end float is less than 0.012". Check rotational
torque by hand. The torque should be less than .25 N-m (2.2 lbs-inch.)
16.
Check that the gear backlash is between 0.15 and 0.406 mm (0.006 and
0.016 in). You should not have to adjust the backlash.
17.
Press in input oil seal (19), using tube of correct diameter. Be careful not
to damage seal lip.
18.
Press oil cap (20) on to cover the rear of housing, using a tube of the
correct diameter.
19.
Place top cover (22) on top of housing and secure with six cap screw
(23).
20.
Check gearbox housing for leaks by plugging all holes except one. Apply
.275 bar (4 psi) compressed air and immerse the gearbox in water to
verify that there are no leaks.
21.
Remove gearbox from water and dry off with compressed air. Add SAE
80W or 90W EP oil until it runs out of side level hole. Tighten all plugs.
Reinstallation
NOTE:
Gearbox is heavy: do not attempt to move without mechanical assis-
tance.
1.
Set gearbox on cutter and fasten with bolts and nuts. Torque bolts to
406.75 N-m (300 lbs-ft).
2.
Attach crossbar (Crossbar Installation, page 25).
Figure 13
. Gearbox
1.
Crown gear
2.
Gearbox housing
3.
Input shaft
4.
Output shaft
5.
Gear, pinion
6.
Bearing
7.
Input bearing
8.
Protective seal
9.
Cotter pin
10.
Snap ring
11.
Snap ring
12.
Shim, 45.3 x 2.5
13.
Shim, 70.3 x 84.7
14.
Nut
15.
Castle nut
16.
Shim, 50.3 x 70.3
17.
Shim
18.
Oil seal (Vertical Shaft)
19.
Oil seal (Horizontal Shaft)
20.
Cap
22.
Top cover
23.
Cap screw 8 mm x 16 (8.8)
24.
Vent plug
25.
Cotter pin
26.
Bearing
Summary of Contents for BATWING BW20.50QE
Page 1: ...OPERATOR S MANUAL BATWING ROTARY CUTTER Rev 22 10 2019 BW20 50QE BW20 60QE BW20 70QE MAN1279...
Page 10: ...10 Declaration of Conformity MAN1279 15 04 2019...
Page 45: ...Common Components 45 MAN1279 15 04 2019 NOTES...
Page 46: ...46 50 Series Parts MAN1279 15 04 2019 CENTER FRAME ASSEMBLY BW20 50QE...
Page 50: ...50 50 Series Parts MAN1279 15 04 2019 WING CENTER GEARBOX ASSEMBLY BW20 50QE...
Page 55: ...50 Series Parts 55 MAN1279 15 04 2019 NOTES...
Page 56: ...56 60 Series Parts MAN1279 15 04 2019 CENTER FRAME ASSEMBLY BW20 60QE...
Page 60: ...60 60 Series Parts MAN1279 15 04 2019 WING CENTER GEARBOX ASSEMBLY BW20 60QE...
Page 66: ...66 70 Series Parts MAN1279 15 04 2019 CENTER FRAME ASSEMBLY BW20 70QE...
Page 70: ...70 70 Series Parts MAN1279 15 04 2019 WING CENTER GEARBOX ASSEMBLY BW20 70QE...
Page 90: ...10 Declaration of Conformity MAN1279 15 04 2019 10 D claration de conformit MAN1279 15 04 2019...