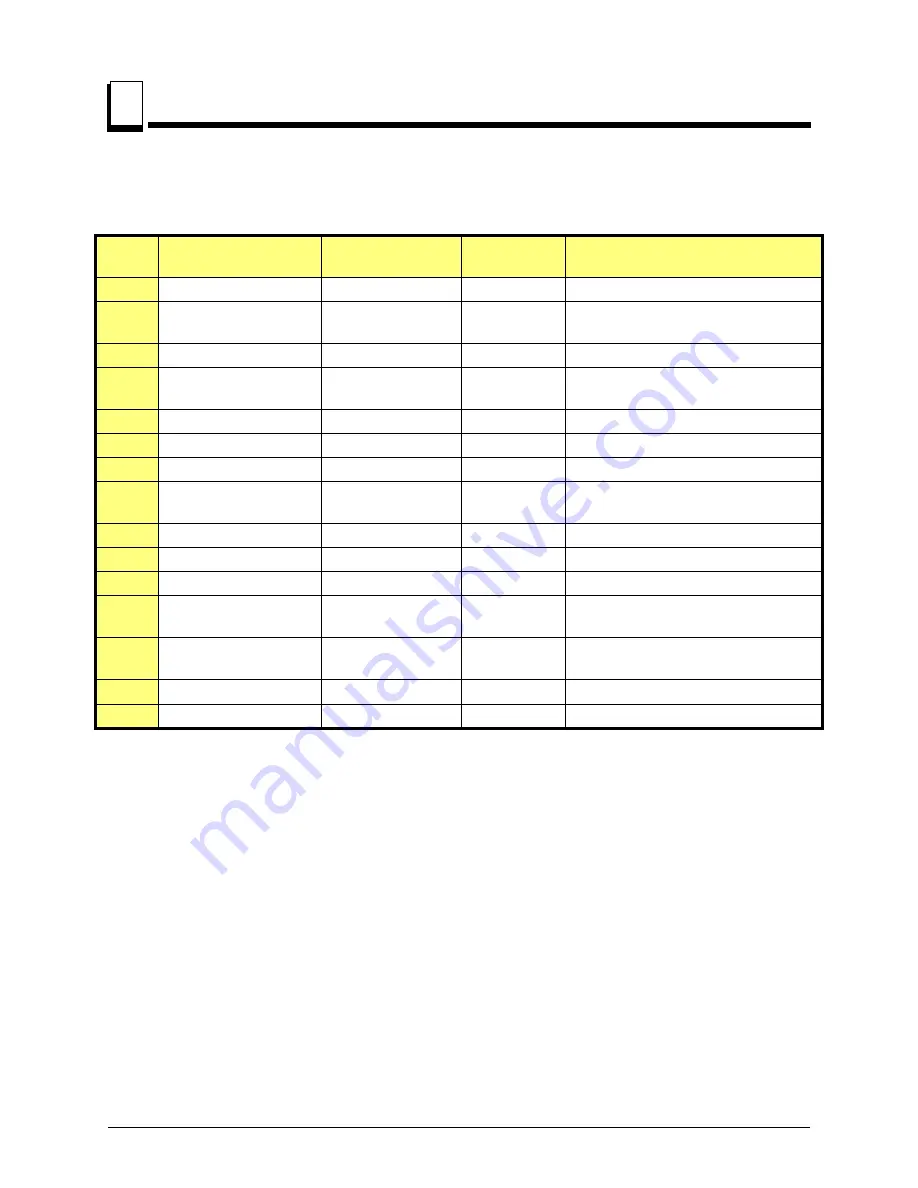
Hydraulic Information
Hydraulic Components
8
8-3
60HD-Rdoc072619
Hydraulic Information
8.3
Hydraulic Components
ID
Mfg. Part No.
Manufacturer
Wood-Mizer
Part #
Description
C1
017275
J-D Hydraulic
017275
Hyd. Cylinder, 3" Bore X 7" Stroke
C2
PMC-19410
Prince Mfg.
015050
Hyd. Cylinder, 1 1/2" Bore X 10"
Stroke
C3
034267
J-D Hydraulic
034267
Hyd. Cylinder, 2” Bore x 10” Stroke
C4
034736
J-D Hydraulic
034736
Hyd. Cylinder, 2 1/2" Bore X 6"
Stroke
C5, C6
014482
J-D Hydraulic
014482
Hyd. Cylinder, 1 1/2” Bore x 6” Stroke
C7, C8
042754
J-D Hydraulic
042754
Hyd. Cylinder, 3" Bore X 8" Stroke
F1
S28
Hyd. Filter Supply
P20301
Filter, Hydraulic Fluid Cartridge
G1
CF-1P-210A
Pressure Devices
Inc.
P10052
Gauge, 5000 PSI Hydraulic
P1, P2
M300-0230
Monarch Hyd.
P12701
Hydraulic Pump, With Motor (DC)
V1
HF37165-06
Scott Industrial Sys 025688
Valve, 7-Section Hydraulic Expndbl.
V2, V3
49005-700
Vonberg
015484
Sequence Valve, 700 psi
V4, V5
28001-503-6.5
Vonberg
038734
Valve, Hydraulic 6.5GPM Velocity
Fuse
V6
PV70-30A-6T-N-12DG Scott Industrial Sys 025840
Valve, 12VDC Proportional Flow
Control
M1, M2
08058-I
Monarch Hyd.
052807
Motor, Iksra Hydraulic Pump (DC)
M3
TG0475US080AABP
Parker
007331
Motor, Hydraulic Log Turner Chain
TABLE 8-1