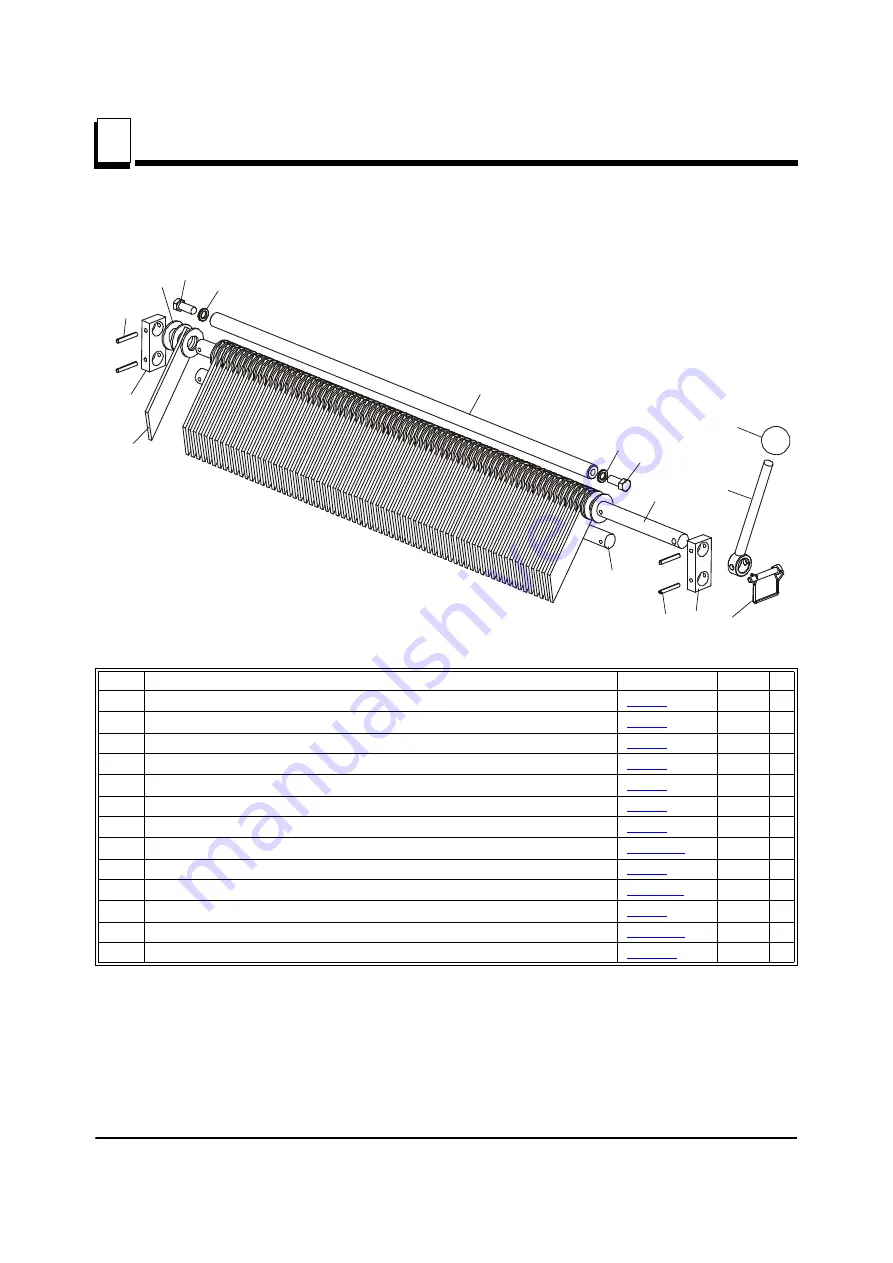
Replacement Parts
Kickback Assembly
5
5-23
IE
doc122719
Replacement Parts
5.18 Kickback Assembly
REF
DESCRIPTION
(
Indicates Parts Available In Assemblies Only)
PART #
QTY.
KICKBACK ASSEMBLY, INDUSTRIAL EDGER
039261
1
1
Handle Weldment, Kickback Lift
039213
1
2
Knob, 5/8-18 Ball
P04211
1
3
Pin, 3/8 x 2 1/4" SQ Wire Lock
014151
1
4
Shaft, Kickback Upper
039073
1
5
Shaft, Kickback Lower
039074
1
6
Block, Kickback Link
039106
2
7
Pin, 1/4 x 1 3/4" Roll
F05012-53
4
8
Finger, 1/4" Kickback
038238
70
9
Washer, 1" ID SAE Flat
F05011-28
145
10
Rod, Kickback Stop
039387
1
11
Bolt, 1/2-13x1 1/4" Hex Head Grade 5
F05008-37
2
12
Washer, 1/2" Split Lock
F05011-9
2
IE0018B
1
2
3
4
5
10
12
12
11
11
6
6
7
7
8
9