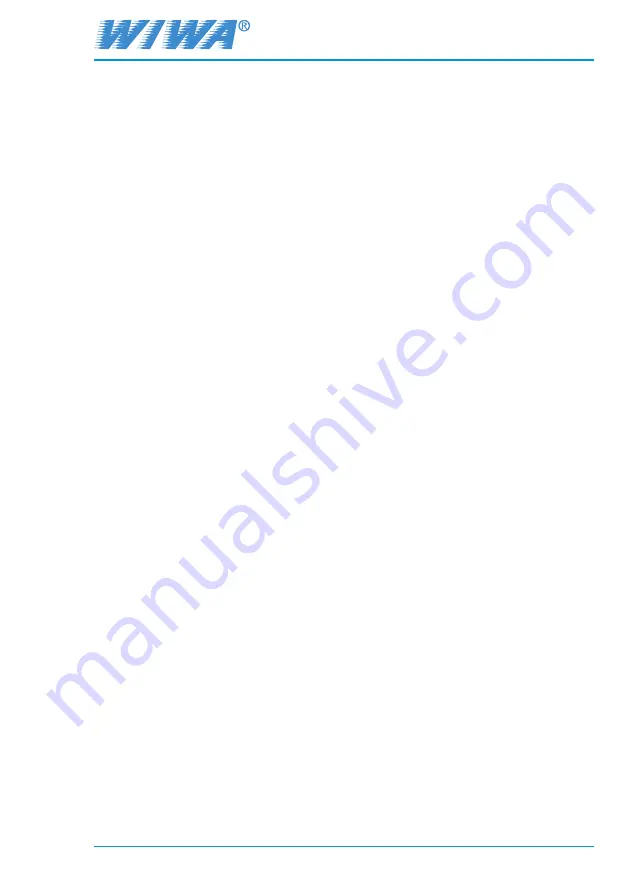
Translation of the original operation manual
5
Airless 270_BAoDB_en_1405 • 0550022 • jw
6 Maintenance ............................................................................. 40
6.1 Regular inspections ............................................................. 41
6.2 Maintenance plan ................................................................ 41
6.3 Maintenance unit ................................................................. 42
6.3.1 Checking the water separator and cleaning the
container ........................................................................ 43
6.4 High pressure pump ............................................................ 43
6.4.1 Checking release agent for material residue ................. 43
6.4.2 Fill in release agent and check the fill level ................... 44
6.4.3 High pressure filter ........................................................ 44
6.4.4 Cleaning the filter element ............................................. 44
6.4.5 Filter elements for high pressure filters ......................... 46
6.5 Recommended operating materials..................................... 46
6.6 Special tools ........................................................................ 47
7 Rectification of faults .............................................................. 48
8 Technical information ............................................................. 51
8.1 Technical data...................................................................... 51
8.2 Equipment card ................................................................... 52
8.3 Type designation ................................................................. 52
8.4 Type plate ............................................................................ 52
8.5 QR code .............................................................................. 53