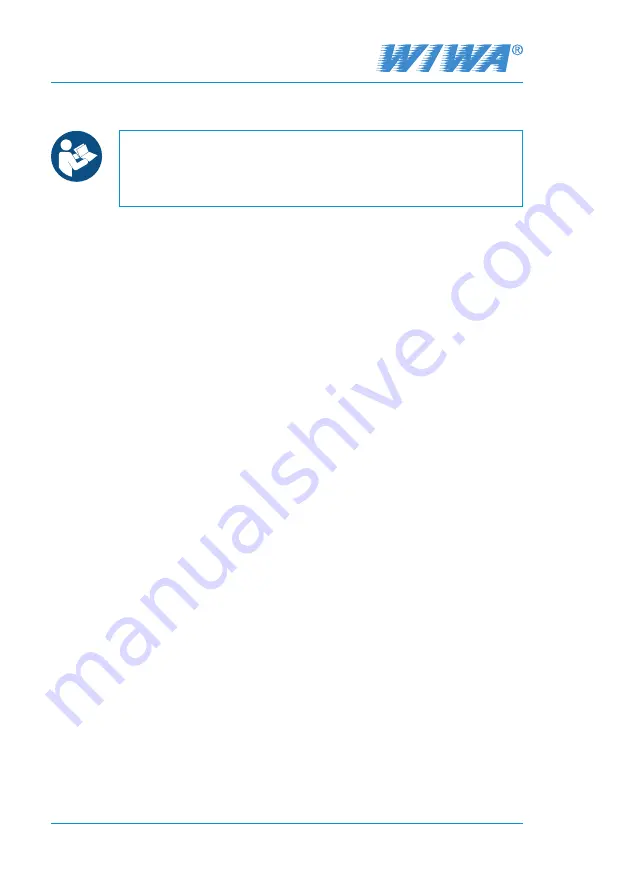
22
Original operation manual
AirlessPhoenixGX_BA_en_1803 • 0550010-en • jw
Safety
2.6 Warranty and liability
Except when otherwise stipulated,
➤
our General Terms and Conditions (GTC) apply for deliveries
within Germany,
➤
our Orgalime SE 01 apply for deliveries to all other countries.
2.6.1 Spare parts
➤
When repairing and maintaining the machine, only original spare
parts from
WIWA
may be used.
➤
If spare parts are used, that have not been produced or supplied
by
WIWA
, the guarantee is voided and all liability shall be
excluded.
2.6.2 Accessories
➤
If you use original accessories from
WIWA
that are designed for
the working pressure, their suitability for use in our machines is
guaranteed.
➤
If you use third-party accessories, these must be suitable for the
machine – in particular with respect to the working pressure, the
current connection data and the connection variables.
WIWA
will not be liable for any damage or injuries due to these parts.
➤
It is essential to observe the safety provisions applicable to
the accessories. You can find these safety provisions in the
separate operation manuals for the accessories.