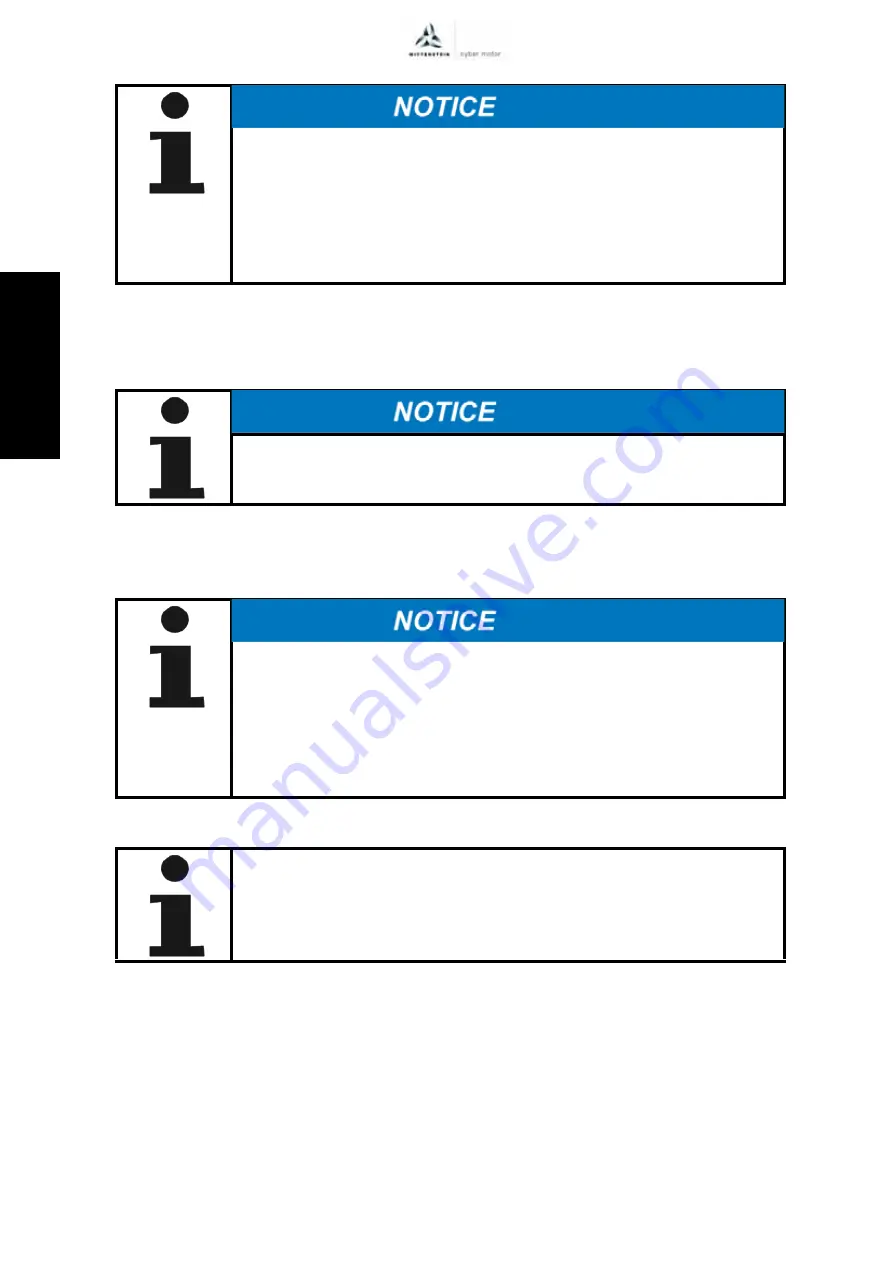
Startup and operation
cyber
®
dynamic line
en-20
5022-D029179
Revision: 04
6.4 Operation
deutsch
english
italiano
français
español
日本語
Please contact our Sales department for additional information. Always enter the serial
number (SN, current designation) or the product identification number (PIN, previous
designation).
6.4
Operation
Circumferential radial forces on the shaft are not permitted.
If this requirement cannot be fulfilled, please contact our sales department. Always enter the
serial number (SN, current designation) or the product identification number (PIN, previous
designation).
If a stop occurs as a result of the switch-off due to excessive heating, a pause between the
individual stroke cycles is recommended.
Moving the motor during the switch-on process of the encoder system
can lead to malfunctions.
When commissioning the motor, make sure that the motor is not moved
during the switch-on process of the encoder system.
The switch-on process is completed as soon as the encoder system
supplies valid position data.
The motor may be moved.
Due to oxygen in the air, UV rays, and cable movements, the bearing
grease and the insulation materials age.
Consult our sales department in case of
excessive wear
.
Due to various components and seals, a new drive can be noticeably
more difficult to move. To ensure optimum grease distribution and
running-in of the moving components, the drive should run in as
follows:
15 min at slow speed load-free (approx. 10% vmax)
10 min at medium speed load-free (approx. 30% vmax)
5 min with increased speed load-free (approx. 60% vmax)
Due to the stroke movement of the piston rod, a certain amount of lubricant
leakage is possible with the ALxx version.
Summary of Contents for cyber dynamic 17
Page 30: ......