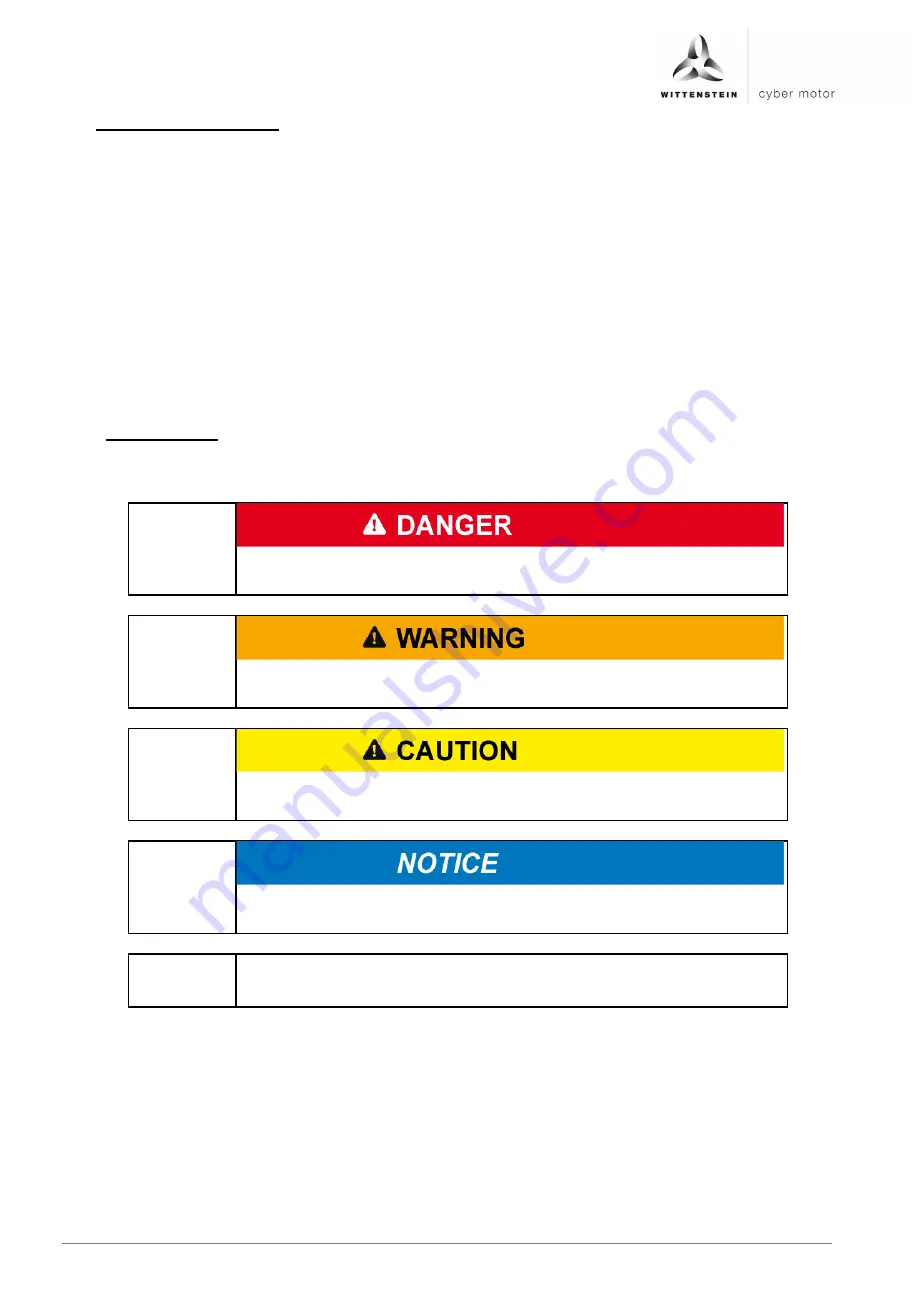
cyber
®
simco
®
drive 2 operating manual
en-4
5022-D057946
Revision: 02
1 About this manual
This manual contains information which is necessary for the safe use of the drive amplifier
cyber
®
simco
®
drive 2
, hereafter known as drive amplifier.
The operator must ensure that this operating manual is read through by all persons assigned
to install, operate, or maintain the drive amplifier, and that they fully comprehend it.
If this manual is supplied with amendment sheets (e.g. for special applications), then the
information in the amendment is valid. Contradictory specifications in this manual are
therefore void.
The operator must ensure that this operating manual is read through by all persons assigned
to install, operate, or maintain the drive system, and that they fully comprehend its content.
Store this manual within reach of the drive amplifier.
Inform colleagues who work in the area around the machine about the
safety instructions
so that no one sustains injuries.
The original was prepared in German, all other language versions are translations of the
original instructions.
1.1 Signal words
The following signal words are used to indicate hazards, things that are forbidden and
important information:
This signal word indicates an imminent danger that will cause
serious injuries or even death.
This signal word indicates a potential hazard that could cause
serious injuries and even death.
This signal word indicates a potential hazard that could cause
minor or serious injuries.
This signal word indicates a potential hazard that could lead to
property damage.
A note without a signal word indicates application hints or
especially important information for handling the product.
Summary of Contents for Cyber Simco Drive 2
Page 1: ...5022 D057946 Revision 02 cyber simco drive 2 Operating manual ...
Page 2: ......
Page 56: ......