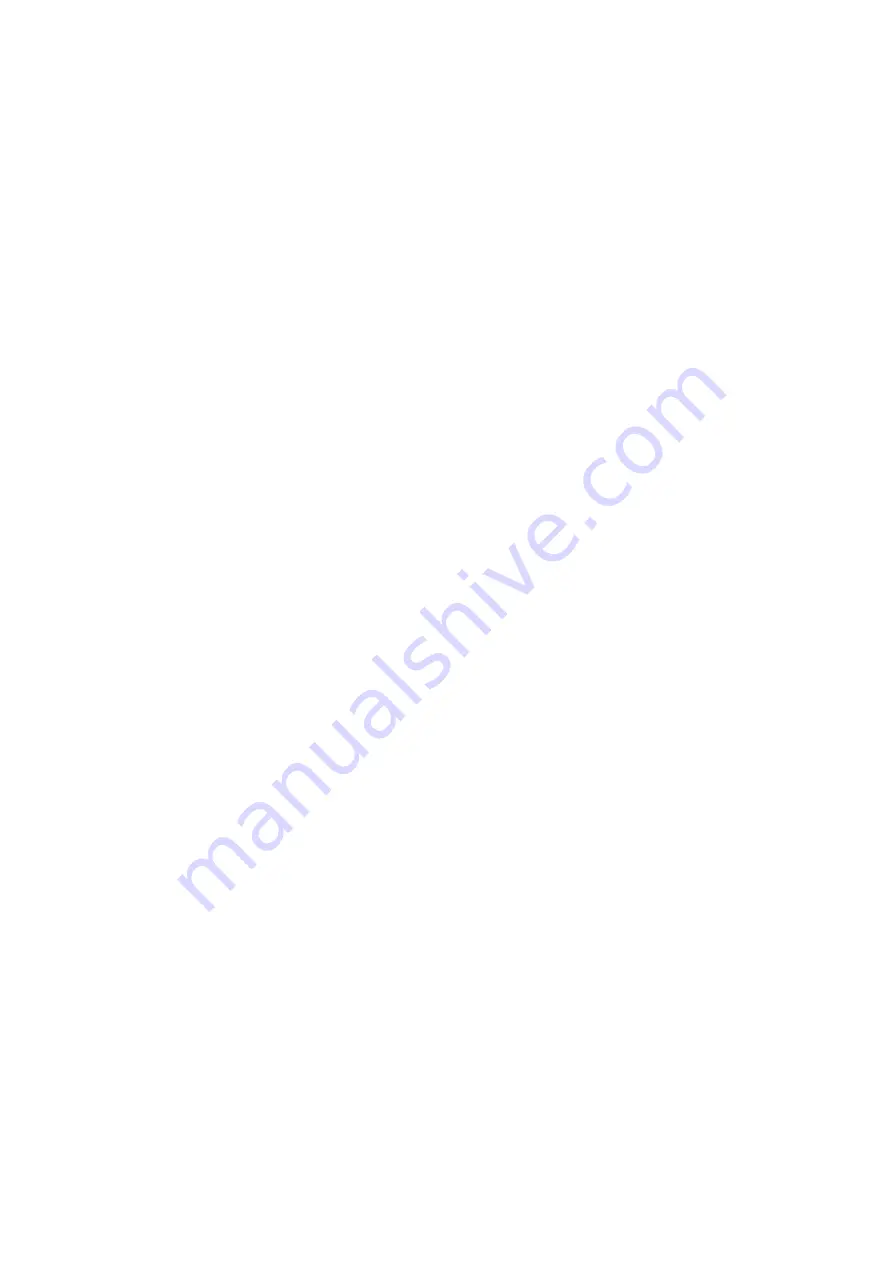
Installation and operating instructions Wilo-Sub TWU 3-...-HS (High Speed) 25
TROUBLESHOOTING AND POSSIBLE SOLUTIONS
English
• Switch off the unit, secure it against being
switched back on again and free the impeller or
clear the suction port
5.
The fluid is too dense
• Contact the manufacturer
9.2.3 Fault: Unit is running but not pumping
1. The “E3” error (dry run) is shown on the display
•
No fluid available: Check inlet, open slide valve
if necessary
• Clean the supply line, slide valve, suction piece,
suction port or suction strainer
•
During standstill, the pressure pipe drains;
check the pipework for leakage and the non-
return valve for contaminants; remedy errors
2. Impeller blocked or slowed
• Switch off the unit, secure it against being
switched back on again and free the impeller
3. Defective piping
• Replace defective parts
4. Intermittent operation (cycling)
• Check switching system
9.2.4
Fault: The unit runs, but not within the specified
operating values
1. Intake blocked
• Clean the supply line, slide valve, suction piece,
suction port or suction strainer
2. Impeller blocked or slowed
• Switch off the unit, secure it against being
switched back on again and free the impeller
3. Incorrect direction of rotation
• Change the direction of rotation via the menu.
4. Air in the system
• Vent the system
5. Defective piping
• Replace defective parts
6.
Inadmissible levels of gas in the fluid
• Consult the plant
7. Excessive decrease in the water table during
operation
• Check the system's supply and capacity
8. “Pmax” value set too high
• Adjust the “Pmax” value according to the pump
curve or install a unit with greater output
9.2.5 Fault: The unit does not run smoothly and is
noisy
1. Unit is operating in an inadmissible range
• Check the operational data of the unit and
correct if necessary and/or adjust the operating
conditions
2. Suction port, suction strainer and/or impeller
clogged
• Clean the suction port, suction strainer and/or
impeller
3. Impeller stiff
• Switch off the unit, secure it against being
switched back on again and free the impeller
4.
Inadmissible levels of gas in the fluid
• Consult the plant
5. Incorrect direction of rotation
• Change the direction of rotation via the menu.
6. Signs of wear
• Replace worn parts
7. Defective motor bearing
• Consult the plant
8. Unit is installed under tension
• Check installation, use expansion joints if
necessary
9.2.6 Fault: Automatic control of the system not
working
1. Taps are closed, unit continues to run or starts up
again immediately
• Difference between Pmax and Pmin too small,
adjust “Dp Start” value in the operating param-
eters
2. Unit constantly switches on and off
•
Leakage in the system; check pipework and
remedy leakage
3. Unit does not shut down
•
Leakage in the system; check pipework and
remedy leakage
• Non-return valve on the pressure port does not
close properly; switch off unit, secure it from
being switched on again, clean non-return
valve
9.2.7 Further steps for troubleshooting
If the points listed here do not rectify the fault,
contact customer service. They can help you as
follows:
• Telephone or written support from customer
service
• On-site support from customer service
• Inspection or repair of the unit at the factory
Please note that you may be charged for some
services provided by our customer service! For
more details, please contact customer service.