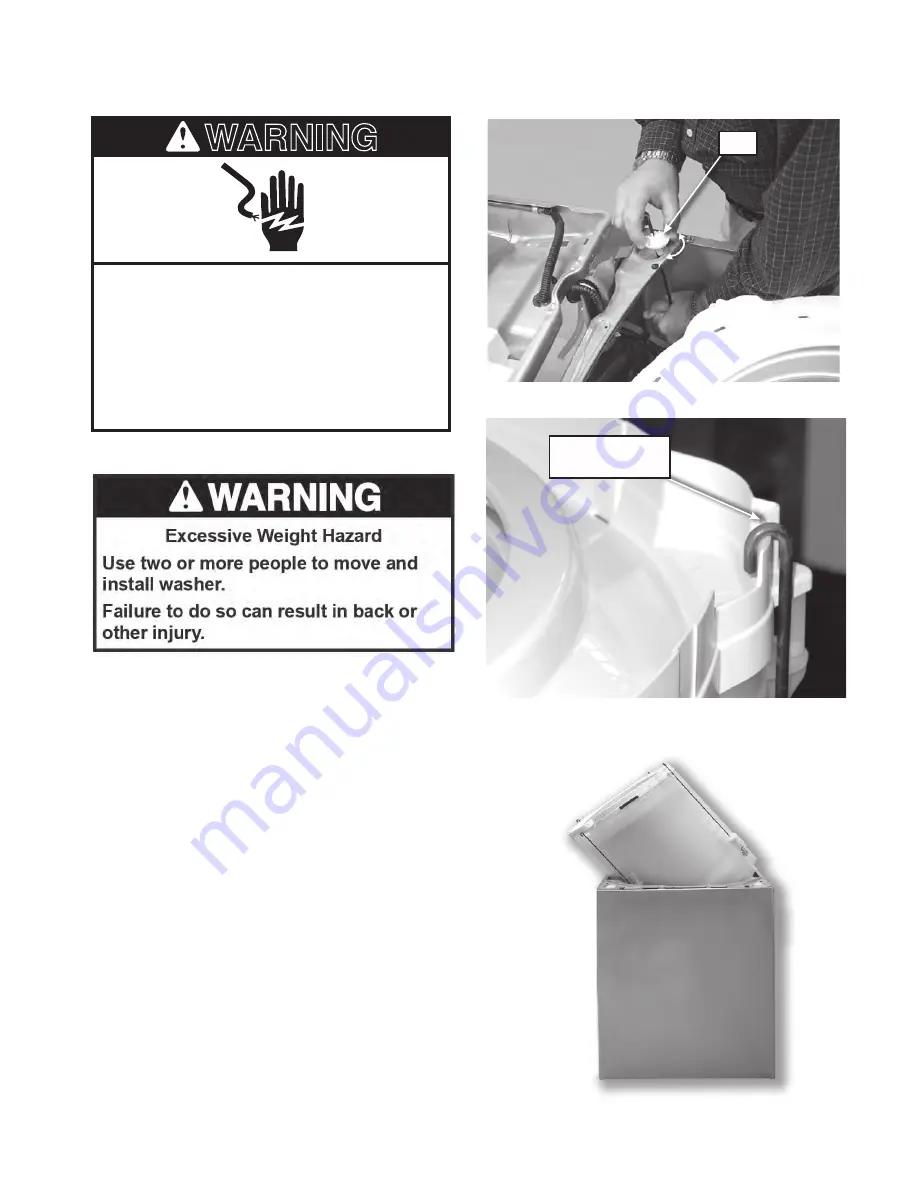
4-21
Figure 3
REMOVING THE TUB
Electrical Shock Hazard
Disconnect power before servicing.
Replace all parts and panels before
operating.
Failure to do so can result in death or
electrical shock.
WARNING
1. Unplug washer or disconnect power.
Figure 1
Figure 2
Ball
Hang Suspension
Rod Here
2. Turn off the water supply to the washer.
3. Raise the top on the hinges. See the
section: “REMOVING THE TOP”.
4. Remove harness from control and water
valves to set the top aside.
5. Remove the basket. See the section
REMOVING THE IMPELLER BOLT AND
BASKET.
6. Remove suspension rods from balls, see
figure 1.
11. Hang the rods on the top edge of the
tub ring.
12. Lift tub out, see figure 3.
Summary of Contents for Cabrio WTW5700XW
Page 58: ...4 22 NOTES ...
Page 84: ......