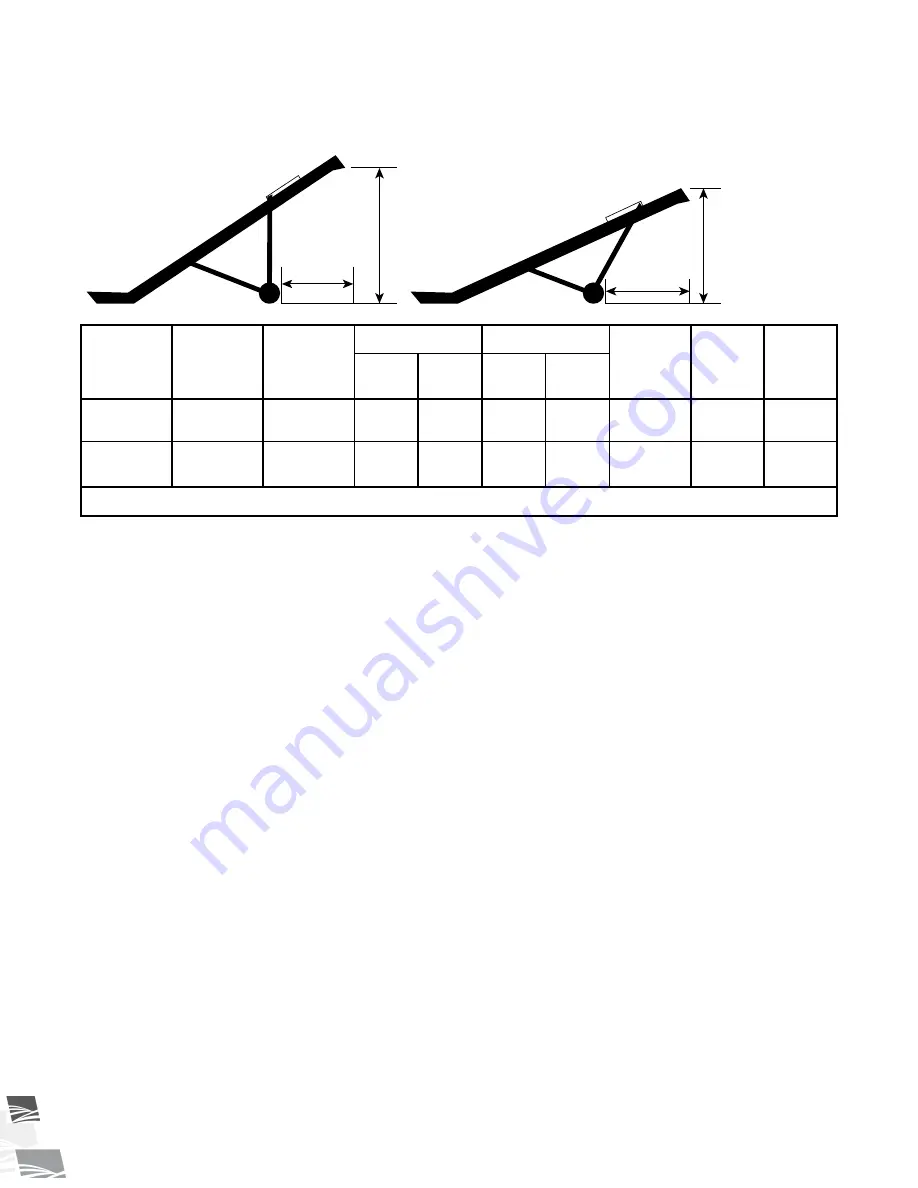
58
30998 R1
5
5.. S
Sp
pe
ec
ciiffiic
ca
attiio
on
ns
s
B
A
B
C
Model
Belt Length
Weight
lbs
Up-Operation
Down - Transport
Width
(ft)
HP Elec
HP HYD.
(in
3
)
A
(ft)
B
(ft)
C
(ft)
B
(ft)
WCX 1335 —
Electric
72'
995
17
12.5
10.5
13
10.5
5
N/A
WCX 1335 —
Hydraulic
72'
995
17
14
10
15
10.5
N/A
4.5*
*Hydraulic motor supplied with hydraulic drive kit. H Series motor (4.5in
3
) requires 12 — 16 gal/min.
5. SPECIFICATIONS
WCX 1335 TOP-DRIVE CONVEYOR – PORTABLE GRAIN BELT CONVEYOR