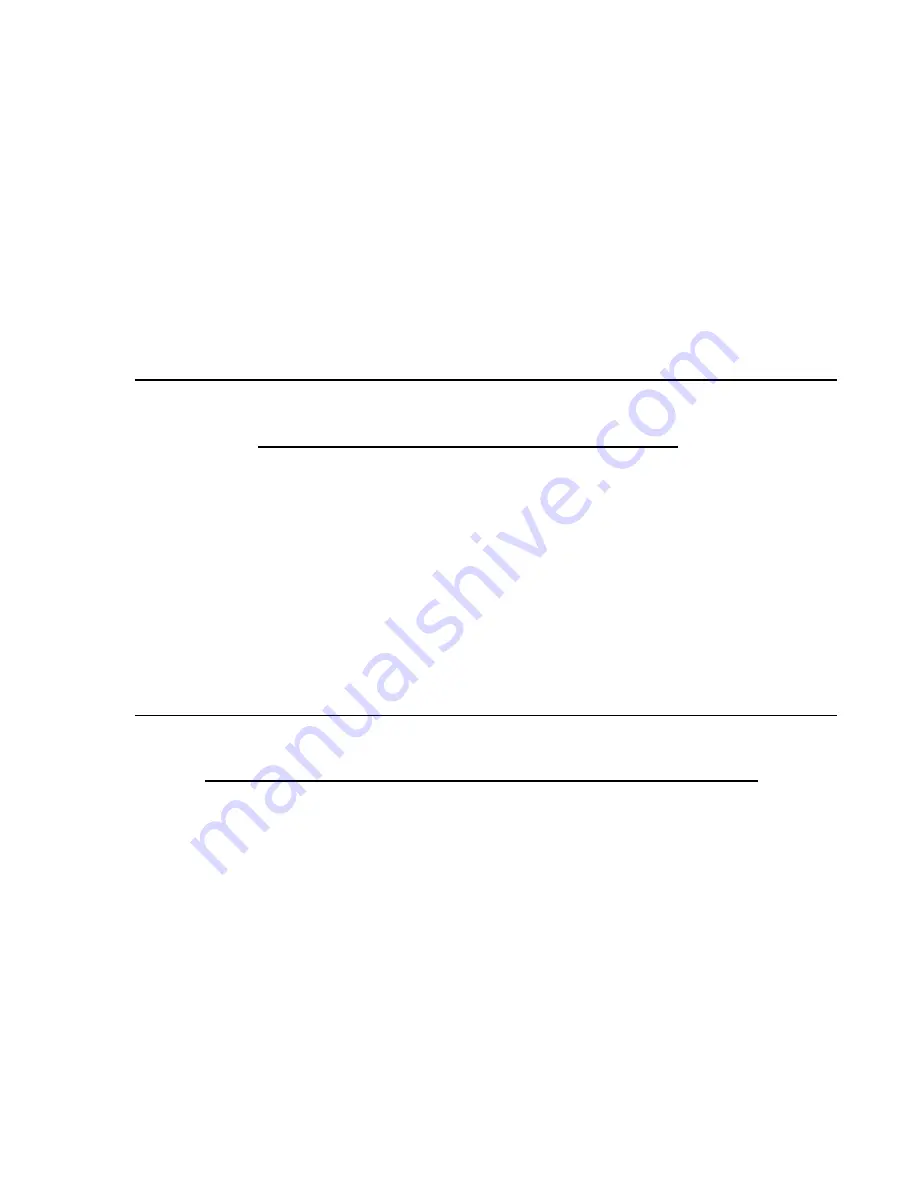
Section 2.4 Service
MT 1 CALIBRATION PROCEDURE
Step 4 CONTINUED....
ORIGINAL PCB COMPLIANCE TEST:
(taken from A-00848 SHEET 1 OF 2, ITEM #6,TABLE 1 AND 2.)
(3 VDC STILL CONNECTED) WITH SWITCH 1 OPEN, AND COUPLED TO A 2cc CAVITY, TEST
POINT 3 (BLACK WIRE) SHALL BE SET TO 3.0 VDC +/- .05 BY ADJUSTING R33. SWITCH 1 IS
THEN CLOSED AND THE 3VDC IS DISCONNECTED FROM TP2. OPEN AND CLOSE SWITCH 1
TEN TIMES AND RE-CHECK THE 3V LEVEL AT TP3.
A. USING A 1cc CAVITY ADJUST R70 PER TABLE 1
B. USING A 3cc CAVITY ADJUST R69 PER TABLE 1
C. REPEAT STEPS A AND B UNTIL ACCURATE READINGS ARE OBTAINED
D. USING A 2cc CAVITY COMPLIANCE SHALL BE WITHIN LIMITS AS PER TABLE 2
E. USING A .2cc CAVITY COMPLIANCE SHALL BE WITHIN LIMITS AS PER TABLE 2
ORIGINAL PCB ONLY
BAROMETRIC PRESSURE / COMPLIANCE CALIBRATION POINT
RANGE (Mbar)
3 CC
1 CC
947 - 952 ................... .C5 - C6 ..................... 73 - 74
953 - 959 .................... C4 - C5 ...................... 72 - 73
960 - 968 .................... C3 - C4 ...................... 72 - 73
969 - 975 .................... C2 - C3 ...................... 72 - 73
976 - 983 .................... C1 - C2 ...................... 71 - 72
984 - 993 .................... C0 - C1 ...................... 71 - 72
994 -1000 .................... BF - C0 ...................... 71 - 72
1001 -1008 .................. BE - BF ..................... 70 - 71
1009 -1017 .................. BD - BE ..................... 70 - 71
1018 -1025 .................. BC - BD ..................... 70 - 71
1026 -1031 .................. BB - BC ..................... 6F - 70
ORIGINAL PCB ONLY
TABLE 1 Calibration Points (from A-00848)
ORIGINAL PCB ONLY
BAROMETRIC PRESSURE COMPLIANCE CALIBRATION POINTS
RANGE (Mbar)
3 CC
2 CC
1 CC
.2 CC
947 - 952 ..............C4 - CC ......... 9B - 9F .......... 70 - 76 .......... 4A - 52
953 - 959 ..............C3 - CB ......... 9A - 9F .......... 6F - 75 .......... 49 - 51
960 - 968 ............. C2 - CA ......... 99 - 9E .......... 6F - 75 .......... 49 - 51
969 - 975 .............. C1 - C9 .......... 98 - 9D .......... 6F - 75 .......... 49 - 51
976 - 983 .............. C0 - C8 .......... 98 - 9D .......... 6E - 74 .......... 49 - 51
984 - 993 .............. BF - C7 .......... 97 - 9C .......... 6E - 74 .......... 49 - 51
994 -1000 .............. BE - C6 .......... 96 - 9B .......... 6E - 74 .......... 49 - 51
1001 -1008 ............ BD - C5 ......... 96 - 9B .......... 6D - 73 .......... 49 - 51
1009 -1017 .............BC - C4 ......... 95 - 9A ......... .6D - 73 ......... 49 - 51
1018 -1020 .............BB - C3 ......... 95 - 9A .......... 6D - 73 .......... 49 - 51
1021 -1025 .............BB - C3 ......... 94 - 99 .......... 6D - 73 .......... 49 - 51
1026 -1031 ............ BA - C2 ......... 94 - 99 .......... 6C - 72 .......... 49 - 51
ORIGINAL PCB ONLY
TABLE 2 Calibration Points (from A-00848 sheet 1 of 2)
GO TO STEP 5
pg 13
Summary of Contents for Micro Tymp 1
Page 10: ......
Page 11: ......
Page 12: ......
Page 22: ...Section 2 4 Service MT 1 CALIBRATION PROCEDURE CALIBRATION NOTES date____ ____ ____ pg 19...
Page 47: ......
Page 51: ......
Page 52: ......
Page 54: ......
Page 56: ......
Page 67: ......
Page 68: ......
Page 69: ......
Page 70: ......
Page 71: ......
Page 72: ......
Page 73: ......
Page 74: ......
Page 75: ......
Page 76: ......
Page 77: ......
Page 78: ......
Page 79: ......
Page 80: ......
Page 81: ......
Page 82: ......