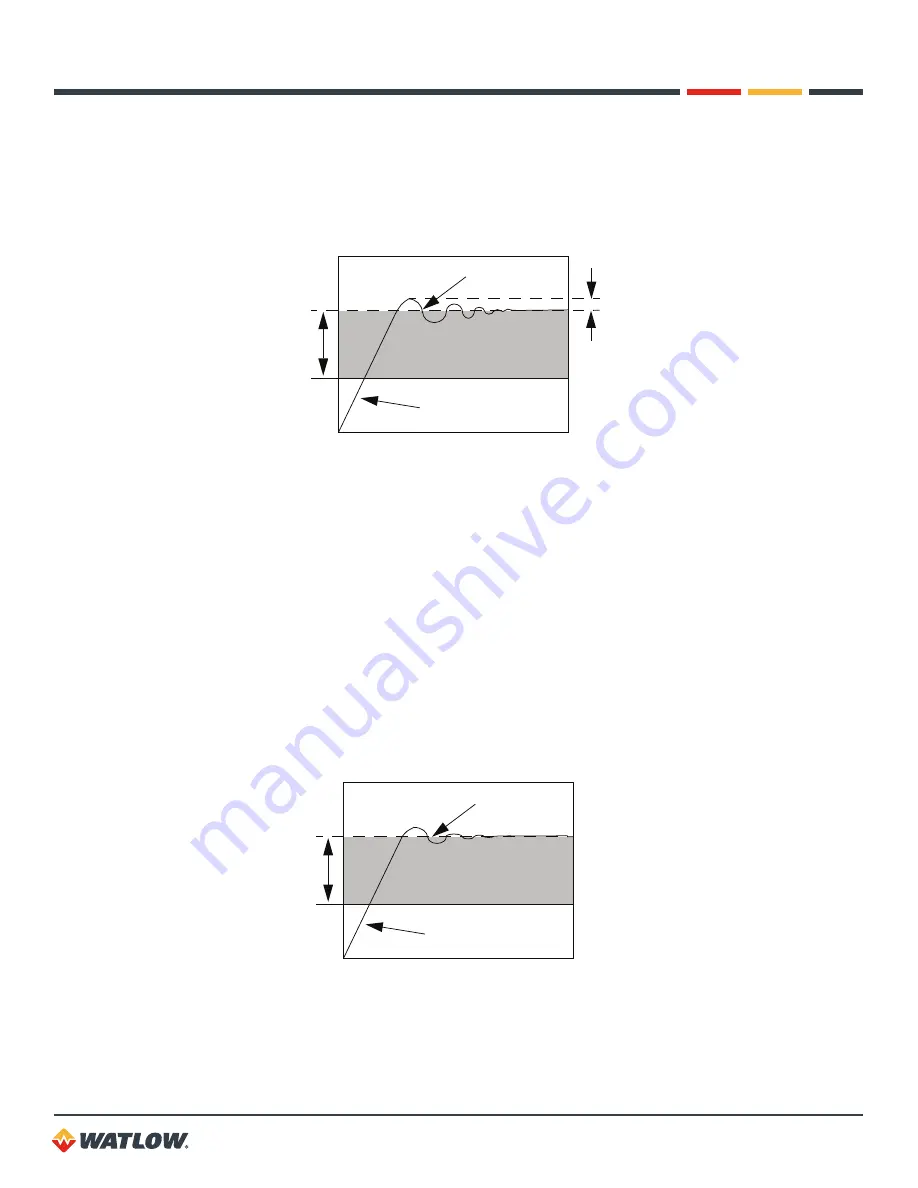
D8 Series User’s Guide
Chapter 5: Tuning and Control
89
Proportional and Integral Control (PI)
With proportional and integral control, the integral term corrects for offset by repeating the
proportional band’s error correction until there is no error. For example, if a process tends to
settle about 5°F below the set point, appropriate integral control brings it to the desired setting by
gradually increasing the output until there is no deviation.
Proportional
Set Point
Process Variable
Band
Overshoot
Figure 5.3
– Proportional and Integral Control
Proportional and integral action working together can bring a process to set point and stabilize it.
However, with some processes the user may be faced with choosing between parameters that
make the process very slow to reach set point and parameters that make the controller respond
quickly, but introduce some transient oscillations when the set point or load changes. The extent to
which these oscillations cause the process variable to exceed the set point is called
overshoot
.
Proportional, Integral and Derivative Control (PID)
Derivative control corrects for overshoot by anticipating the behavior of the process variable and
adjusting the output appropriately. For example, if the process variable is rapidly approaching the
set point from below, derivative control reduces the output, anticipating that the process variable will
reach set point. Use derivative control to reduce the overshoot and oscillation of the process variable
that is common to PI control.
Figure 5.4 shows a process under full PID control.
Proportional
Set Point
Process Variable
Band
Figure 5.4
– Proportional, Integral and Derivative Control