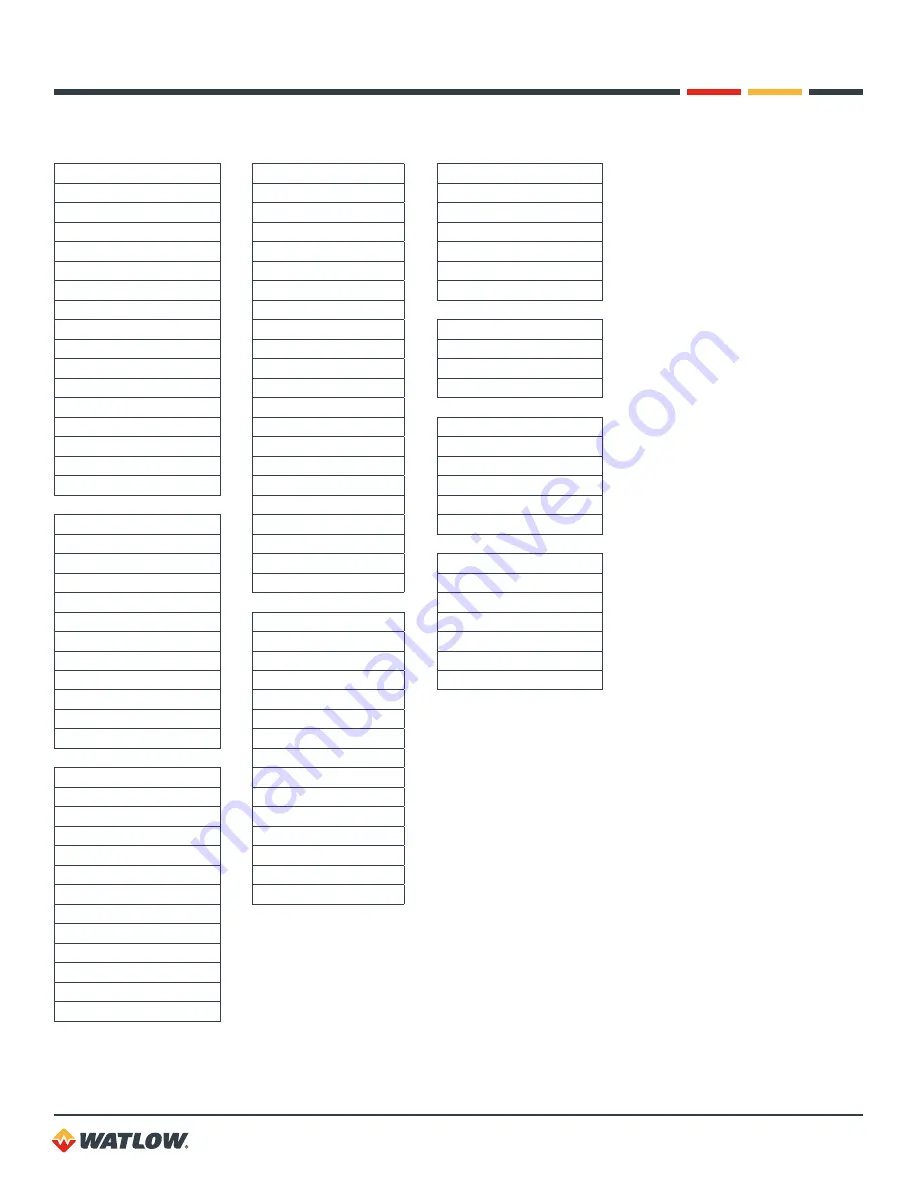
D8 Series User’s Guide
177
Menu Structure
GLOBAL SETUP
OUTPUT
PV RETRANS
Load Setup from job
Heat output
Heat output retrans PV
Save setup as job
Heat cycle time
Ht retrans LowPV
BCD job load
Heat SDAC signal
Ht retrans HighPV
BCD job load logic
Ht SDAC low signal
Cool output retrans PV
Mode override
Ht SDAC hi signal
Cl retrans Low PV
Mode override D/I active
Heat action
Cl retrans HighPV
Power up alarm delay
Heat power limit
Keypad lock
HtPwr limit time
CASCADE
TC short alarm
Sensor fail heat output
Cascade prim loop
AC line freq
Open T/C ht out average
Cascade low SP
MAC ID
Heat output curve
Cascade hi SP
Baud rate
Cool output type
Module LED
Cool SDAC signal
RATIO
Network LED
Cl SDAC low signal
Ratio master loop
Bus off count
Cl SDAC hi signal
Ratio low SP
WATLOW D8x Vx.xx cs=xxxx
Cool action
Ratio high SP
Cool power limit
Control ratio
INPUT
ClPwr limit time
Ratio SP diff
Input type
Sensor fail cool output
Loop name
Open T/C cl out average
I/O TESTS
Input units
Cool output curve
Digital inputs
Calibration offset
Keypad test
Reversed T/C detect
ALARMS
Display test
Disp format
Alarm high SP
Test D/O 1
Input range high
Alarm high func
• • •
Input high signal
Alarm high output
Test D/O 20
Input range low
HiDeviation value
Input low signal
HiDeviation func
Input filter
HiDeviation output
LoDeviation value
CONTROL
LoDeviation func
Heat prop band
LoDeviation output
Heat integral
Alarm low SP
Heat derivative
Alarm low func
Heat manual reset
Alarm low output
Heat filter
Alarm hysteresis
Cool prop band
Alarm delay
Cool integral
Cool erivative
Cool manual reset
Cool filter
Hysteresis
RestoreAuto