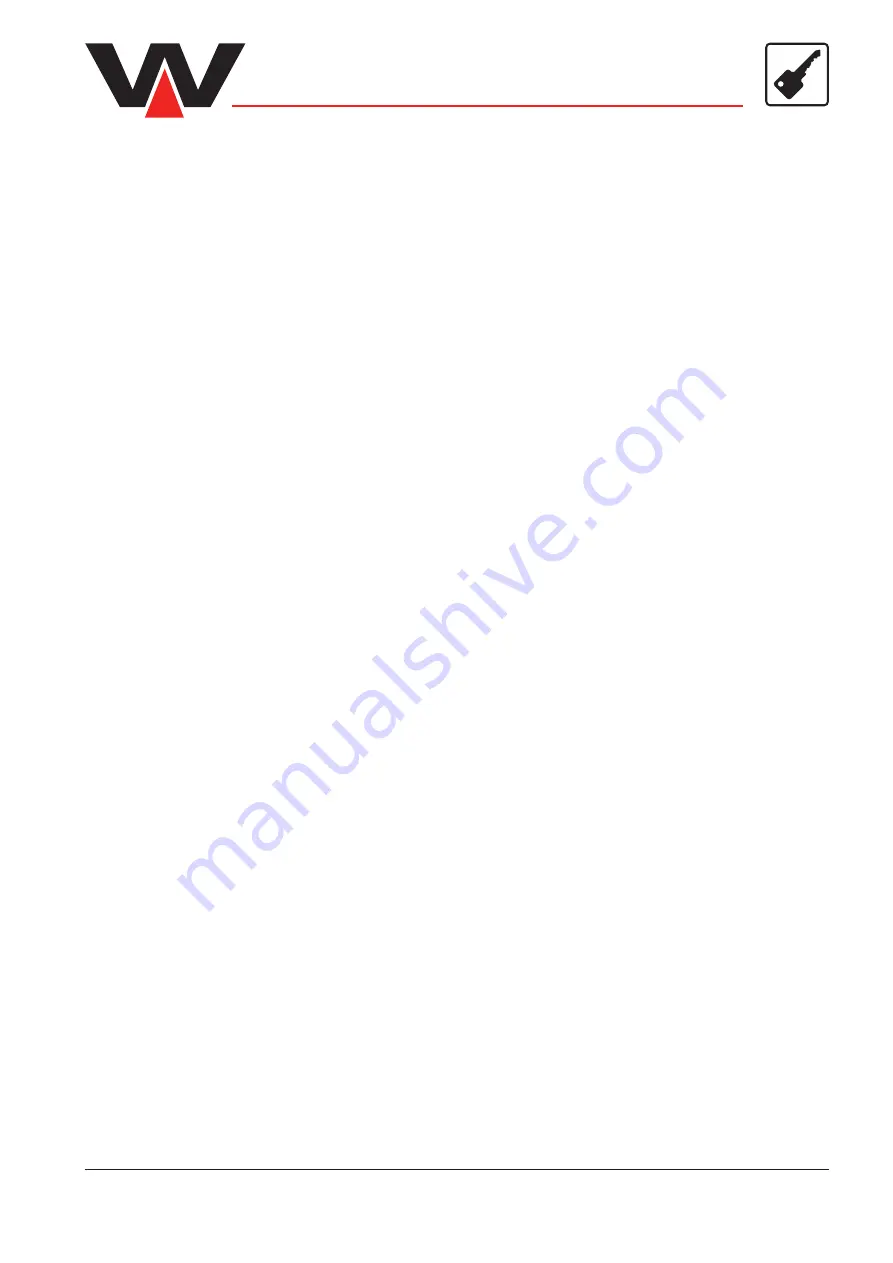
S
TARTING
UP
AND
OPERATING
C
HAPTER
7
THP 94/42 R 4 XXT
THP 125/42 R 4 XXT
THP 140 H/42 R 4 XXT
GB-07.2005
7-25
•
If a blockage occurs, immediately pump the concrete back into the hopper and mix it. Only switch over to
forward conveying when the conveying cylinder and transfer tube are correctly switching over automatically.
Carefully start pumping through again.
7.6.1.1
Causes of blockages
•
Laitance too thin or with insufficient cement
•
Insufficient laitance used
•
S-valve leaking (wear plate worn and ring too large: replace the parts)
•
Leaking pipework (concrete bleeds out)
•
Set concrete residues in the transfer tube or conveying pipes
•
Unsuitable concrete composition
7.6.2
General instructions for pumping
•
Whilst pumping, be sure not to draw any air in, since compressed air can emerge violently at the discharge
hose, causing concrete to spray out. Therefore keep the hopper filled at least up to the level of the agitator
shaft.
•
When pumping, keep the agitator running.
•
Avoid long pauses during which no concrete is pumped.
During pauses in pumping the concrete, observe the following points:
•
Do not leave the conveying pipework under pressure
•
Depressurise the conveying pipework by briefly reversing the pump
•
Keep the concrete moving by briefly pumping through and back
•
If there is a long pause in pumping, pump the concrete back into the hopper and mix it again before pumping
it through the conveying pipework.
If the distributor boom whips around, determine the cause of this.
The following causes may lead to this:
•
The outriggers may have moved – repeat the outrigger set-up procedure, see section 7.3.4
WARNING: Before restarting, determine the reason why the outriggers had moved.