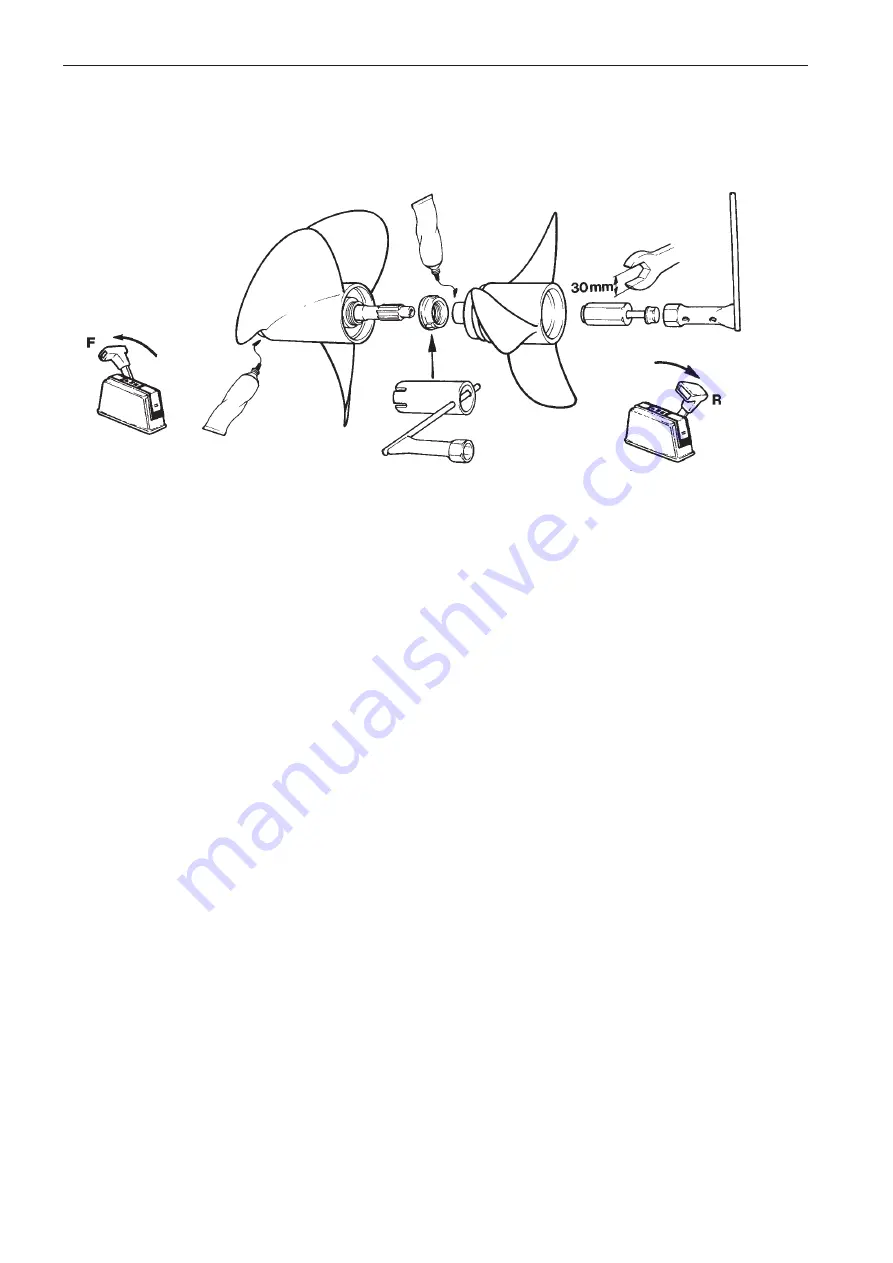
60
Propeller installation. DPX
1. Control lever in “Ahead” position.
2. Use the tool supplied when removing and install-
ing propellers.
3. Lubricate both propeller hubs. Use Volvo Penta
grease 828250-1.
4. Push the front propeller onto the shaft. Screw on
large locknut and tighten with tool. Tightening
torque 50–70 Nm (5–7 kpm).
5. Control lever in “Astern” position.
6. Push rear propeller onto the shaft and tighten with
nut. Use a 30 mm socket and tighten to 25–35 Nm
(2.5–3.5 kpm)
7. Screw in the lock screw and tighten to 70–80 Nm
(7–8 kpm).
Summary of Contents for KAD44P
Page 1: ...INSTRUCTIONBOOK KAD44P KAMD44P ...
Page 2: ......
Page 79: ......
Page 80: ...7737719 0 English 7 1997 ...