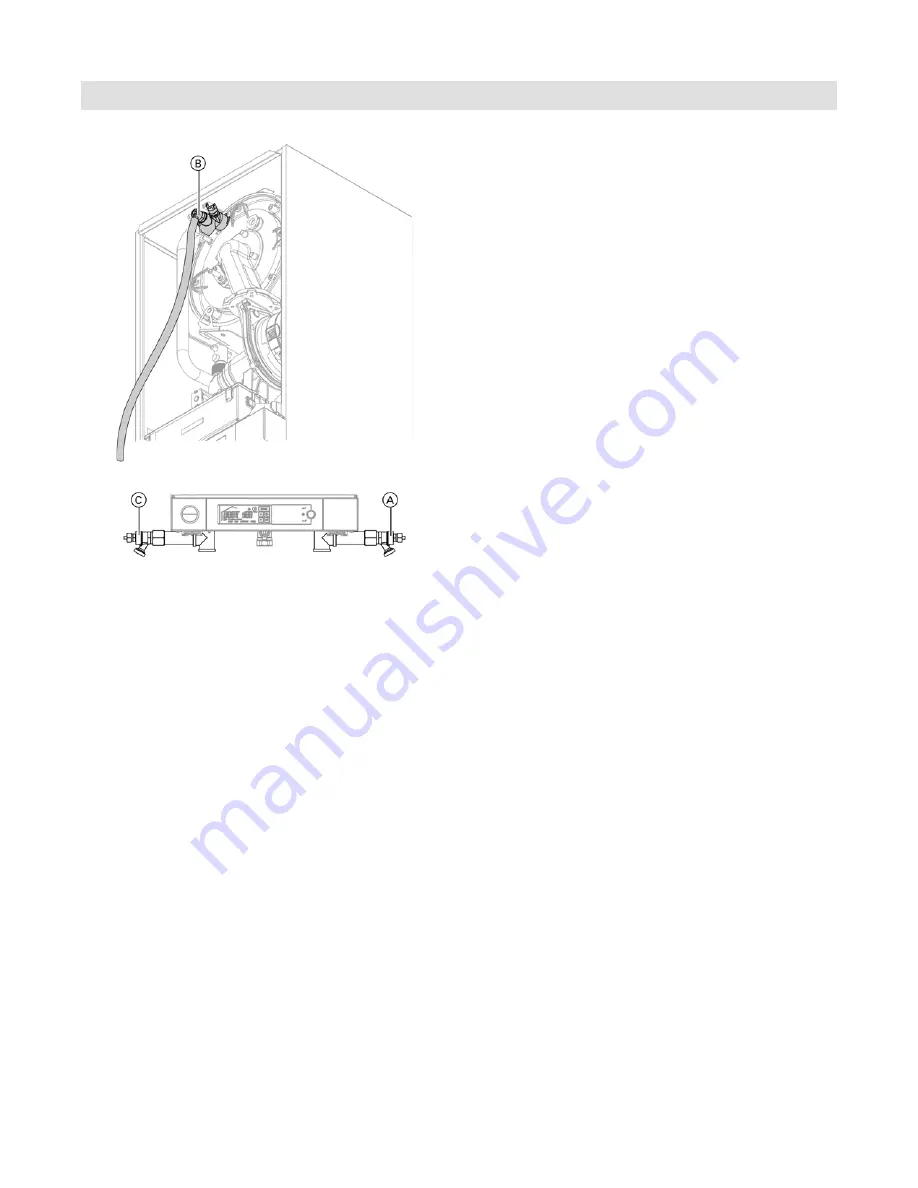
45
5784 568 - 13
Vitodens 100-W, B1HA/B1KA 26 to 125 Combi Installation/Service
Start-up, Inspection and Maintenance
Filling and Bleeding the Heating System
(continued)
1. Open system isolation valves (if installed).
Note:
Before filling the heating system with water,
check that all necessary flow check valves are
installed.
2. Check inlet pressure of the diaphragm expansion tank.
Note:
If the nitrogen pressure of the precharged
expansion
tank is less than the static pressure
of the system, inflate membrane pressure to
slightly exceed pressure of system. The static
pressure required at the tank is based upon the
static height of the system. The system fill
pressure value must be equal to the expansion
tank pressure value at approx. 60ºF (15.6ºC).
3. To remove debris and/or sludge ensure that the
system piping is flushed out. Failure to do so may
cause sediment in the boiler causing overheating
and damage not covered by warranty.
Note:
System fill pressure must be approximately
3
psig
higher than the static head when the
system is cold.
4. Optional:
Fill the heating system with water at the boiler filling
tap
A
and drain air completely from the drain tap
C
.
Note:
Water treatment should be considered in areas
where it is known that boiler feed water
contains
a
high mineral content and hardness.
In areas where freezing might occur, an
antifreeze may be added to the system water
to protect the system. Please adhere to the
specifications given by the antifreeze
manufacturer. Do not use automotive silicate-
based antifreeze. Please observe that an
antifreeze/water mixture may require a backflow
preventer within the automatic water feed and
influence components such as diaphragm
expansion
tanks,
radiation, etc. A 30% antifreeze
content will provide freeze-up protection to
-10°F (-23°C). Do not use antifreeze other than
specifically made for hot water heating systems.
System also may contain components which might
be negatively affected by antifreeze. Check total
system frequently when filled with antifreeze.
5. Check system pressure.
6. Ensure proper / adequate fuel supply exists.
Open gas shutoff valve.
Max. boiler operating pressure.......................45 psig
Min. boiler operating pressure........................12 psig
Pressure relief valve.....................................30 psig
To fill and remove air from the heat exchanger:
Connect a hose to the boiler filling tap
A
and connect
the other end to fresh water supply (or heating medium).
Connect the hose (supplied with the boiler) to the
bleeding
port
B
on top of the supply pipe.
Open the fresh water supply valve and then open the
boiler filling tap
A
slowly to fill the boiler with water.
Isolation valves (not shown) to isolate system
components must be closed during fill/bleed process.
Using the supplied key, open the bleeding port
B
on the heat exchanger until no sound of escaping air is
heard. Open valve
C
to release the remaining air. Close
the
valves.
Flush the boiler heat exchanger via the boiler supply
and return (for at least 10 min.) until all air has
been removed from the boiler.
When the drain tap
B
begins to bleed water, close
the boiler drain valve and open system isolation valves
(field
supplied).