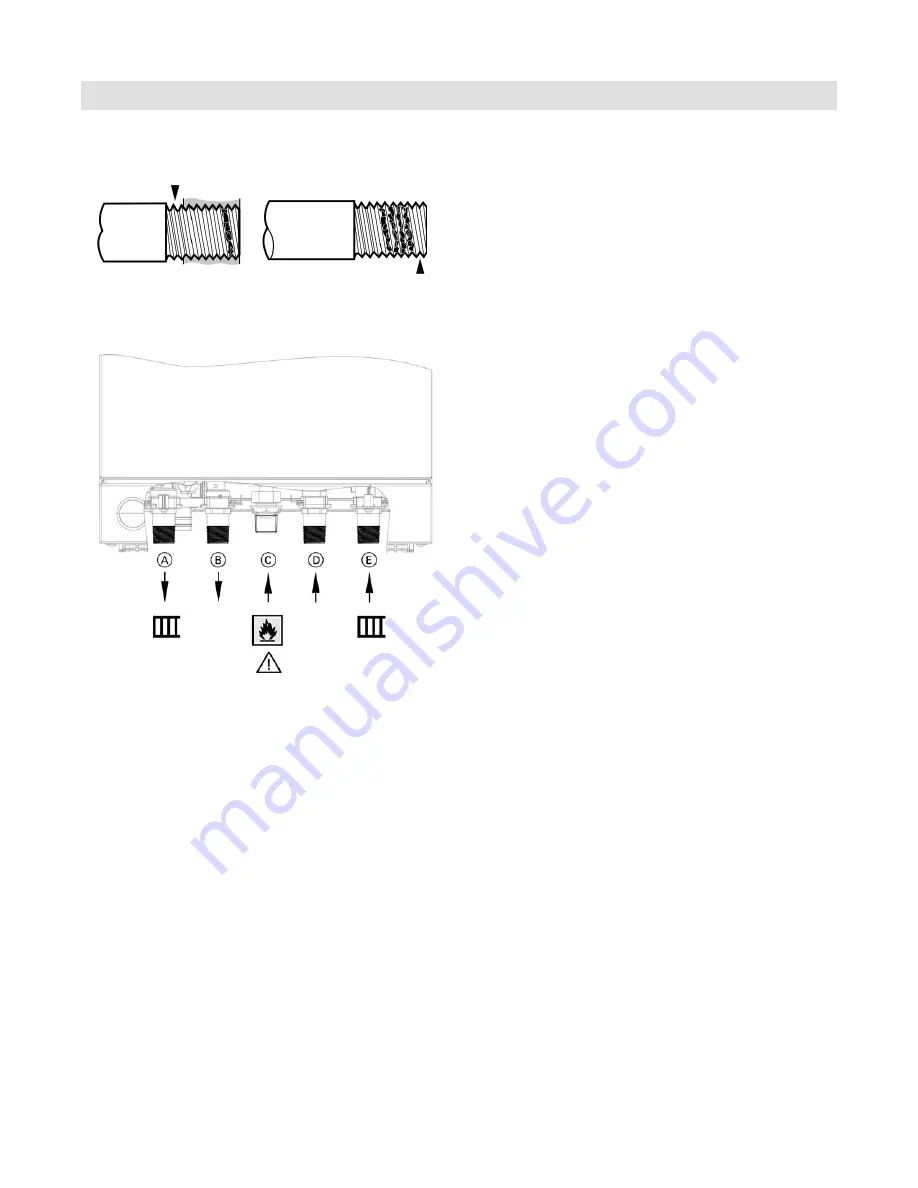
18
5784 568 - 13
Vitodens 100-W, B1HA/B1KA 26 to 125 Combi Installation/Service
Connections
Boiler
Connections
(continued)
Proper piping practice
Gas connection and piping
Support piping by proper suspension method.
Piping must not rest on or be supported by boiler.
Legend
A
Boiler water supply connection NPT ¾ in. (male thread)
B
DHW tank heating supply NPT ¾ in. (male thread)
(for B1HA) or DHW connection NPT ½ in. (male thread)
(for
B1KA)
C
Gas connection NPT ¾ in. (male thread)
D
DHW tank heating return NPT ¾ in. (male thread)
(for B1HA) or DCW connection NPT ½ in. (male thread)
(for
B1KA)
E
Boiler water return connection NPT ¾ in. (male thread)
1. Make gas connection in accordance with codes
CAN/CSA B149.1 or 2 in Canada. In the United
States, use the National Fuel Gas Code ANSI Z223.1/
NFPA 54, as well as local codes where applicable.
2. Close gas shutoff valve on boiler.
3. Perform leak test.
4. Bleed air from gas supply pipe.
See following page for details on gas connection and piping.
2 imperfect threads Use moderate amount of dope
Leave 2 threads bare
Note:
The B1HA DHW supply and return connections are
supplied capped. For installations that require DHW
tank connections remove caps. For installations that
do not require DHW tank connections leave caps
installed.