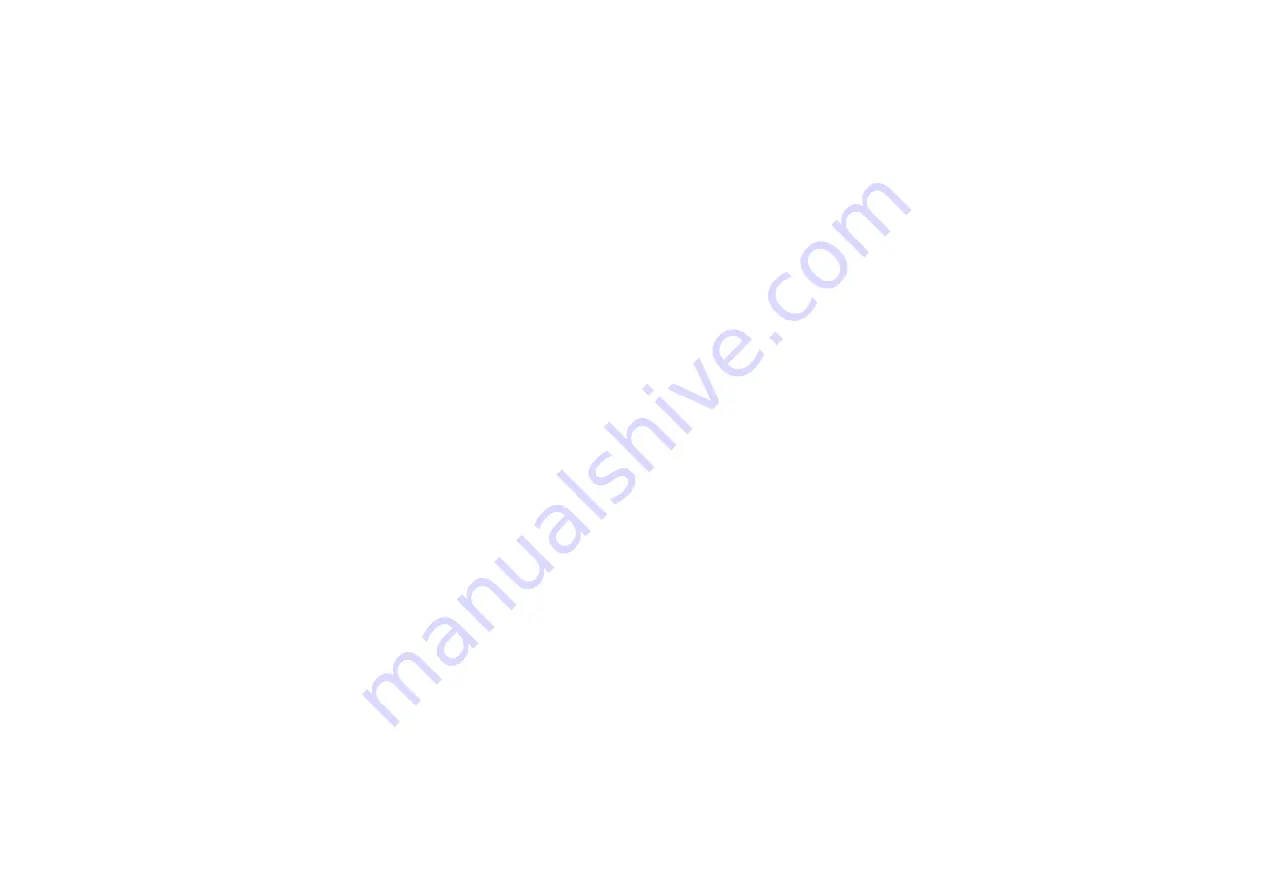
Lower cover (2) (Ref. Pig. 2) has a locating collar and is attached by six studs (18) to the delivery section housing. The cover
has a flange with four studs (1) to mount the fuel pump and a seat for rubber seal with metal insert (3) which precludes leakage of oil
from the oil pump and fuel pump.
The shafts and gears are of steel and have cemented teeth.
Pump drive shaft (5) has a gear rim, splines for connecting with vertical shaft (13) rotating the pump, slot for key (11) of
scavenging section gear (12), radial and central holes for delivery of oil through the pump drive shaft to the engine, a square hole shank
whereby the fuel pump is rotated.
Driven shaft (16) is made integral with gear (15), its lower end has a splined ahank on which gear (17) is installed, meshing with
the gear rim of drive shaft (5).
Scavenging section gears (10) and (12) have central holes for mounting on shafts (5) and (16).
Gear (12) includes a slot for key (11) whereby it is connected with drive shaft (5) of the pump.
Pressed in gear (10) are two bronze bushings which allow free rotation of the gear on shaft (16).
Delivery section gear (6) has a central hole with a bronze bushing which allows free rotation of the gear on shaft (5).
The reducing valve assembly (Ref. Pig. 3) comprises a seat pressed in the pump housing, valve (1), bushing (3), spring (2),
adjustment screw (7), lock nut (5), cap (8) and gaskets (6). The oil in the delivery section (outlet line) is adjusted to the required
pressure by the adjustment screw. If the delivery section pressure exceeds the permissible limit, the valve opens and by-passes
excessive oil to the delivery section inlet, thus maintaining constant pressure of oil in the oil system during normal operation of the
engine.
The check valve comprises a body, a valve, a guide and a spring. The valve is made of bronze and has a spherical collar
whereby it is pressed to the seat in the housing by the spring.
The valve is installed on its guide by the cylindrical hollow shank. The valve body is a hollow steel part pressed in the delivery
section housing.
The valve body has four cutouts on each of two sides to pass flow of oil during operation of the engine.
With the engine inoperative, the check valve precludes flow of oil from the tank to the engine.
When the engine is running, the valve is opened by the oil pressure to pass oil from the pump delivery section to the engine oil
system.
3.2. OIL SUMP
The oil sump (Ref. Pig. 4) cast of magnesium alloy is installed between cylinders Nos 5 and 6 and serves as a container to
receive oil from the engine.
The oil sump is attached to the intermediate crankcase by two flanges and studs driven into the intermediate crankcase. The
flanges have passages to drain oil from the intermediate crankcase.
Besides, the rear flange of the oil sump has an outlet hole of the passage for scavenging oil from the sump, connected to the
passages in the intermediate crankcase, mixture collector, diffuser and rear cover.
The top front portion is provided with a flange for mounting the bellows and a round hole to drain oil from the gearbox housing.
y The lower part of the oil sump has a flange with three studs to install the adapter of
the filter with chip detector and a flange with two studs to connect the pipeline to breath the engine in inverted flight.
3.3. FILTER WITH CHIP DETECTOR
Summary of Contents for M-14P
Page 6: ...19 Engine M 14P Front View Figure 1...
Page 7: ...20 Engine M 14P Rear View Figure 2...
Page 27: ...40 Arrangement of Airborne Tools in Case Figure 1...
Page 39: ......
Page 44: ...57 Engine M 14P Test Run Chart Figure 201...
Page 67: ...80...
Page 163: ...176 Crankshaft Thrust Ball Bearing Front Cover Figure 1 Intermediate Crankcase Figure 2...
Page 166: ...179 Intermediate Grankcase Front Portion Figure 3 Intermediate Crankcase Rear Portion Figure 4...
Page 173: ...186 Front view Cylinder Figure 1 Rear view...
Page 180: ...193 Timing Mechanism Schematic Diagram Figure 6 Cam Plate Figure 7...
Page 189: ...Blower Longitudinal Section View Figure 1...
Page 191: ...Rear view Mixture Collector Figure 2 Diffuser Figure 3...
Page 194: ...1 Plate 2 Spring 3 Plate 4 Gear 5 Accessory Drive Shaft Blower Coupling Figure 4...
Page 204: ...Oil Sump Figure 4...
Page 216: ...Engine M 14P Gear Train Figure 1...
Page 247: ...Carburetor AK 14P Operation Diagram Figure 1...
Page 249: ......
Page 274: ......
Page 282: ......
Page 283: ......
Page 288: ...T t en 0 CO 0 T K D fi h0 Ol f 01 3 0 F4...
Page 293: ......
Page 344: ...Generator Electrical Connection Diagram Commutator Side View Figure 3 1 Main Pole 2 Interpole...
Page 355: ......
Page 358: ......