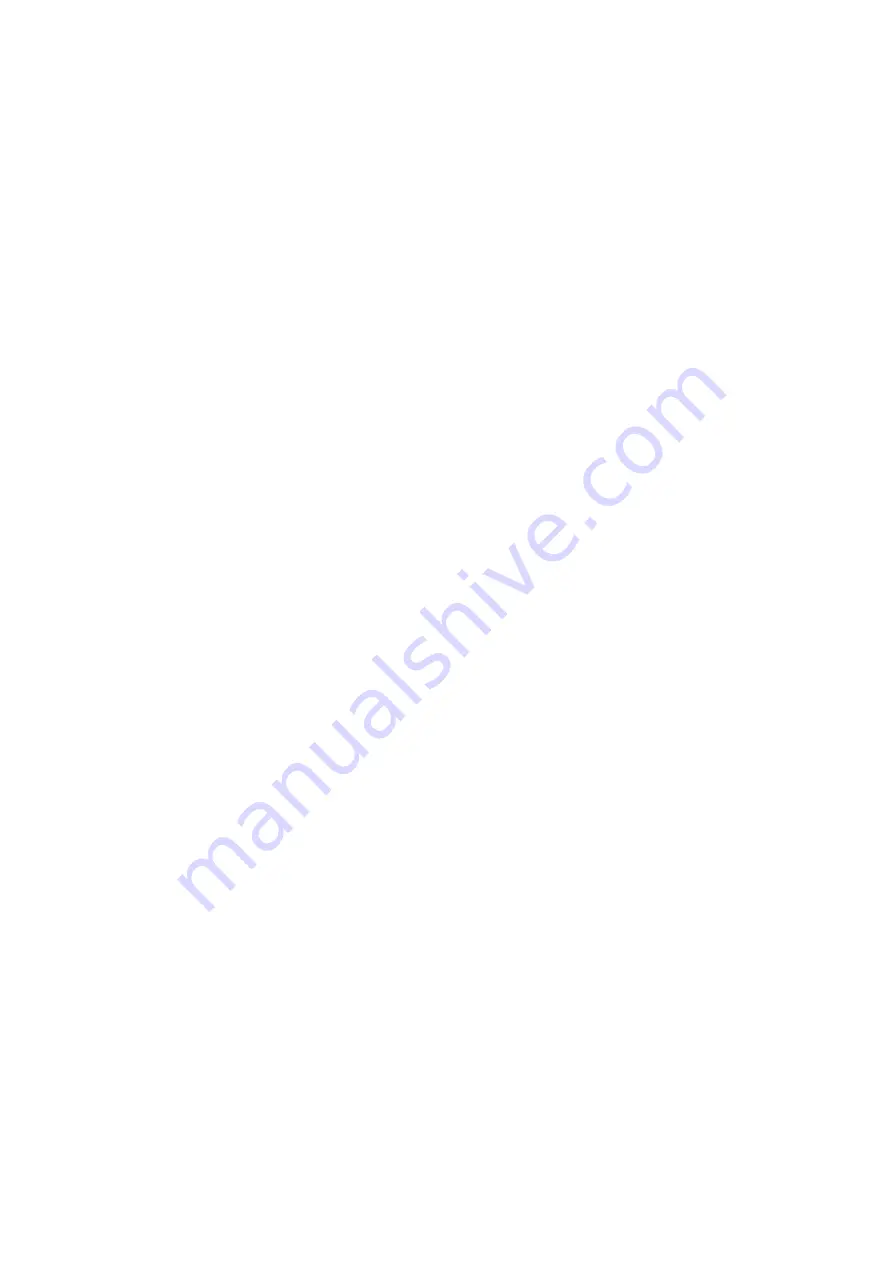
195
The set of a tappet (Ref. Pig. 9) includes guide bushing (3), tappet (4), tappet end piece (2), spring
(1), roller (5), roller bushing (6), roller pivot (7).
Tappet (4) is a steel cylindrical rod having a slot, in its lower part with holes for the pivot carrying a
floating bronze bushing and the roller. Installed in the upper part of the tappet is a spring and end piece with
spherical recess for the push rod end.
The tappets, push rod ends, adjustment screws and valve rockers have passages to supply oil to the
valve case mechanisms.
Tappet guide bushing (3) is made of steel, has an oval flange with two holes for securing to the
intermediate crankcase. The guide bushing lower part is made with a slot equal in width to that of the roller
and fixing the latter relative to the cam plate raceway.
The guide bushings of the tappets of inlet valves in cylinders Kos 1, 2, 8 and 9, as well as of the
exhaust valves in cylinders Nos 1, 2, 3, 8 and 9 have slots and holes to supply oil under pressure.
Tappet push rod (1) (Ref. Pig. 10) is made of a seamless steel pipe with steel end pieces having
spherical ends pressed into its bored ends.
Spherical ends of the push rods enter respective recesses of the rocker adjustment screw and the
tappet. Each push rod is arranged in casing (4).
The push rod casing is a thin-walled aluminium pipe flared at one end and having a bead at the other.
All casings and push rods are interchangeable.
The flared end of the push rod casing is attached by union nut (5) to the connection on
the cylinder valve case, while its other end is attached by rubberized fabric hose (2)
with the guide bushing of the tappet.
Thrust tapered ring (6) is installed under nut (5) to press by its surface the end of casing (4) to the
connection. The rubberized fabric hoses are fastened with clamps (3).
Valve rockers (Ref. Pig. 11) serve to transmit motion from the push rods to the valves at opening and
from the valves to the rods at closing of the valves.
The rockers are made of steel forgings and are installed on needle rollers (8) which rest on steel axle
(10) inserted in the cylinder valve case holes. One end of the rocker is forked. The fork has roller (2) mounted
on pivot (3) to transmit force to the valve stem during operation of the engine. The other end of the rocker has
an adjustment screw which is secured by lock nut (7) after the required clearance between the rocker roller
and the valve stem is adjusted.
Summary of Contents for M-14P
Page 6: ...19 Engine M 14P Front View Figure 1...
Page 7: ...20 Engine M 14P Rear View Figure 2...
Page 27: ...40 Arrangement of Airborne Tools in Case Figure 1...
Page 39: ......
Page 44: ...57 Engine M 14P Test Run Chart Figure 201...
Page 67: ...80...
Page 163: ...176 Crankshaft Thrust Ball Bearing Front Cover Figure 1 Intermediate Crankcase Figure 2...
Page 166: ...179 Intermediate Grankcase Front Portion Figure 3 Intermediate Crankcase Rear Portion Figure 4...
Page 173: ...186 Front view Cylinder Figure 1 Rear view...
Page 180: ...193 Timing Mechanism Schematic Diagram Figure 6 Cam Plate Figure 7...
Page 189: ...Blower Longitudinal Section View Figure 1...
Page 191: ...Rear view Mixture Collector Figure 2 Diffuser Figure 3...
Page 194: ...1 Plate 2 Spring 3 Plate 4 Gear 5 Accessory Drive Shaft Blower Coupling Figure 4...
Page 204: ...Oil Sump Figure 4...
Page 216: ...Engine M 14P Gear Train Figure 1...
Page 247: ...Carburetor AK 14P Operation Diagram Figure 1...
Page 249: ......
Page 274: ......
Page 282: ......
Page 283: ......
Page 288: ...T t en 0 CO 0 T K D fi h0 Ol f 01 3 0 F4...
Page 293: ......
Page 344: ...Generator Electrical Connection Diagram Commutator Side View Figure 3 1 Main Pole 2 Interpole...
Page 355: ......
Page 358: ......