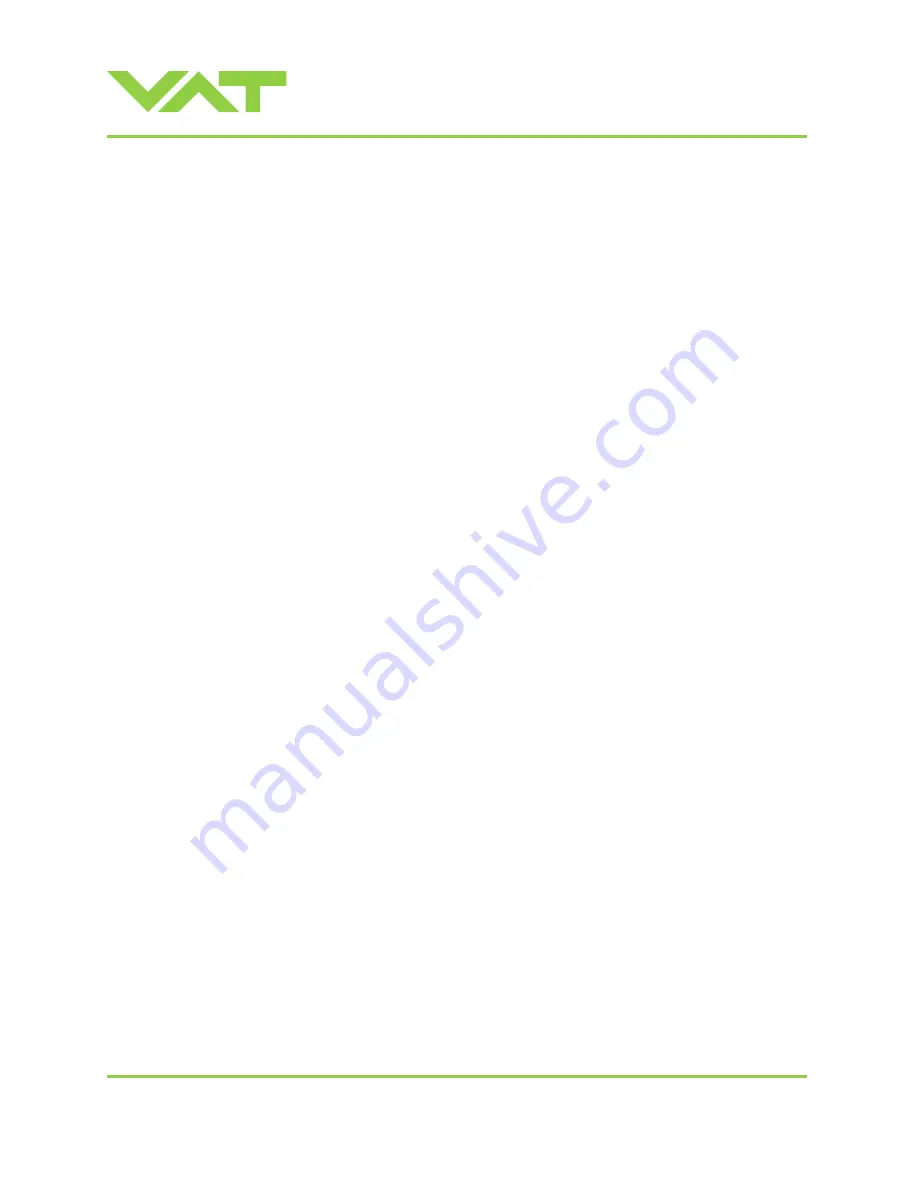
Installation, Operating & Maintenance Instructions
Series 615 DN 40 (I.D. 1.5”), RS485
VAT Vakuumventile AG, CH-9469 Haag, Switzerland
Tel +41 81 771 61 61 Fax +41 81 771 48 30 [email protected] www.vatvalve.com
289111EB
2013-02-05
44/96
3.11.2.3 Optimizing P gain and I gain
Introduction
PI controller mode is used if for any reason (e.g. too long system time constant) the adaptive control mode does not
provide satisfying control performance.
In PI controller mode the parameters P gain and I gain have to be set according to the systems characteristics. The best
set of parameters can be found by using the empiric method below.
1.
Optimizing P gain
and I gain
1.1
Pressure and gas flow for optimization
A PI controller delivers the best results for a certain working point (pressure/gas flow). If there is only one working point,
this pressure and gas flow has to be used for optimizing P and I gain. If there are several working points that have to be
covered, the pressure for optimizing is the medium pressure between highest and lowest pressure to be controlled, the
gas flow for optimizing is the highest flow out of all working points.
Two different pressure set points are necessary for optimization. Set point 1 (SP1) is the pressure for optimizing as
determined above. Set point 2 (SP2) is about 10 - 20% lower than SP1.
Example:
pressure range:
4
– 10 Torr
Flow range:
2
– 4 slm
Pressure set points and gas flow for optimization:
SP1
=
7 Torr
SP2
=
6 Torr
Gas flow
=
4slm