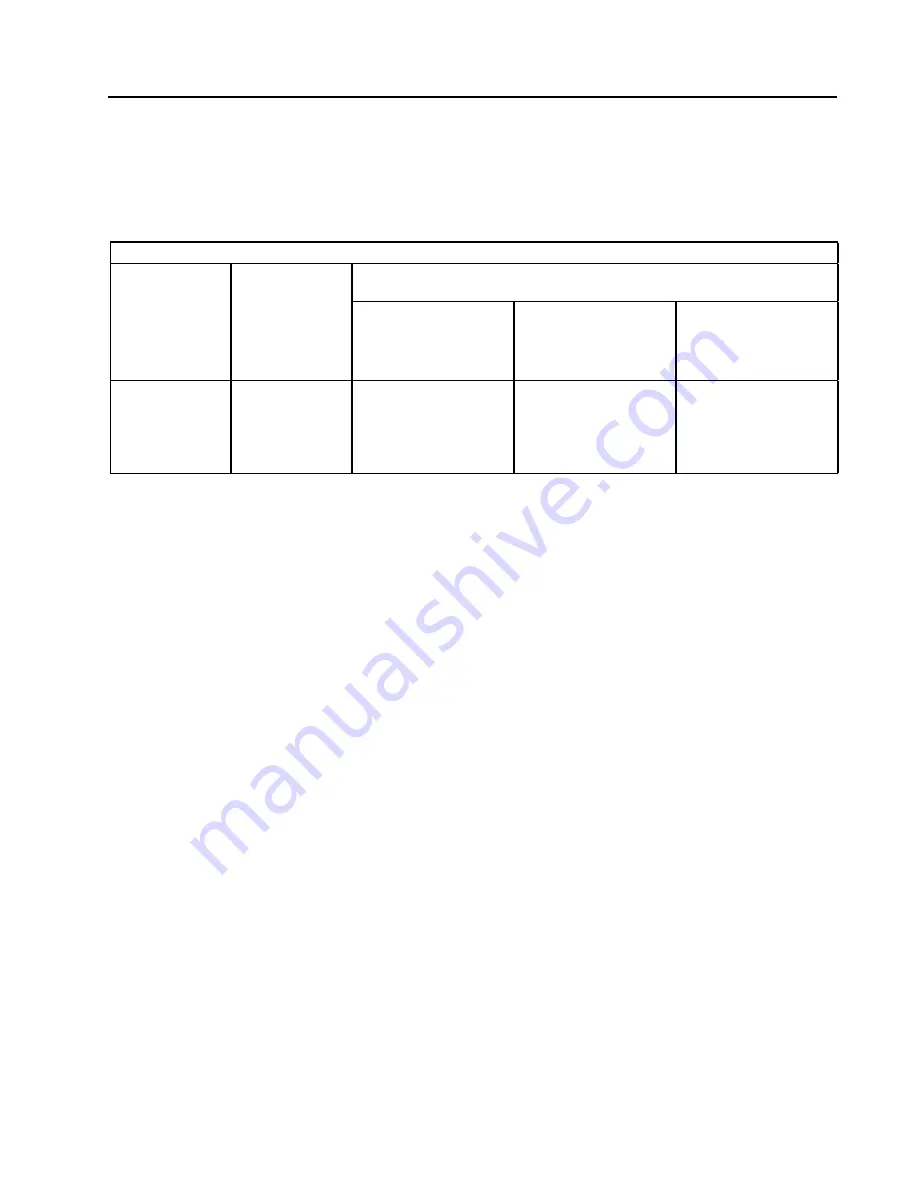
Safety
Valley ClassicPlus Control Panel
9
Minimum Working Clearance
To reduce the risk of injury, all persons require adequate working clearance around the electrical panel or other
electrical equipment. The table below identifies the minimum working clearance needed. Refer to U.S. Occupa-
tional Safety & Health Administration (OSHA) Regulations (Standards - 29 CFR) Safeguards for personnel pro-
tection. -1910.303(g)(1)(i), or any other applicable national, state or local regulations, for additional information.
Concrete, brick or tile walls shall be considered as grounded.
Qualified Person
A Qualified Person is one who, by possession of a recognized degree, certificate, or professional standing, or
who by extensive knowledge, training, and experience, has successfully demonstrated his/her ability to solve or
resolve problems related to the subject matter, the work, or the project.
Only qualified persons may work on electric circuit parts or equipment that have not been de-energized.
Refer to U.S. Occupational Safety & Health Administration (OSHA) Regulations Standards - 29 CFR 1926.32(m)
and 1910.333, or applicable national, state or local regulations for additional information.
Irrigation Equipment near Airports and Crop Dusting Aircraft
• If any part of the irrigation machine comes within 3200 ft (975 m) of an airport runway, especially the ap-
proach (ends) of the runway, additional warning markers may be required. In the United States, CFR Title 14,
Chapter I, Subchapter E, Part 77 – Safe, Efficient Use, and Preservation of the Navigable Airspace describes
when marking is needed.
This document is available at: www.ecfr.gov
• Marking requirements vary depending on the location of the irrigation equipment relative to the runway, the
type of airport (Civil, Military, or Heliport) and other factors. Contact the local airport authority for guidance
and specific recommendations. In the United States, guidelines for marking structures near airports are
published by the Federal Aviation Administration in Advisory Circular AC 70/7460-1L – Obstruction Marking
and Lighting.
Available here: www.faa.gov/regulations_policies/advisory_circulars
• For irrigation machines near private or unregulated airfields, including farm-based airstrips, Valley strongly
recommends complying with the same standards and requirements as Civil airports as shown in Part 77.
• Regulations vary by country, contact your local aviation authority for guidance.
Overhang cables, including overhang back cables are a particular danger. In locations where low-flying
aircraft are likely, such as within 1,500 ft (457 m) of an end of an airport runway, or where crop dusting aircraft
are common, Valley recommends adding obstruction markers to overhang cables to improve their visibility.
For large overhangs (36 ft / 10.97 m Heavy Duty and longer), five 12 in (300 mm) or 20 in (500 mm), aviation
orange marker balls are sufficient. One near the rabbit ears, two in the middle of the back cables and two in
the middle of the highest overhang cables. Refer to Section 3.5 in AC70/7460-1 for additional details. Aviation
marker balls are available online and from a variety of aviation and airport safety equipment providers.
MINIMUM WORKING CLEARANCE 0-600 VOLTS
WIDTH
OF WORKING
CLEARANCE
AREA
HEIGHT
OF WORKING
CLEARANCE
AREA
MINIMUM WORKING CLEARANCE
IN FRONT OF ELECTRICAL PANEL/EQUIPMENT
EXPOSED LIVE PARTS
ON ONE SIDE OF WORK
SPACE AND NO LIVE
GROUNDED PARTS ON
THE OTHER SIDE.
EXPOSED LIVE PARTS
ON ONE SIDE OF WORK
SPACE AND LIVE
GROUNDED PARTS ON
THE OTHER SIDE.
EXPOSED LIVE PARTS
ON ONE SIDE OF WORK
SPACE AND EXPOSED
LIVE PARTS ON THE
OTHER SIDE.
30 in (760 mm)
MINIMUM OR
WIDTH OF
ENCLOSURE,
WHICH EVER IS
GREATER
78 in (1980 mm)
MINIMUM OR
HEIGHT OF
ENCLOSURE,
WHICH EVER IS
GREATER
36 in (915 mm) MINIMUM
42 in (1065 mm) MINIMUM
48 in (1220 mm) MINIMUM